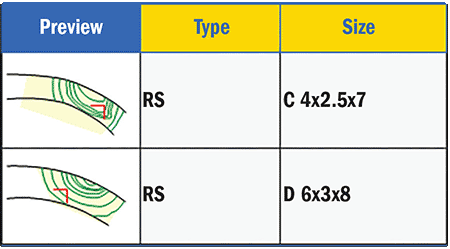
Feedwater pumps are at the heart of any boiler system, and just as the human heart supplies blood throughout the body, these pumps supply feedwater to the boiler. Any opportunities to improve the efficiency of feedwater pumps should be taken advantage of to ensure a healthy, long-lasting boiler system.
Once pumps are installed within a system, there are a few things that can be done to increase efficiency. During the engineering and procurement phase is when there is the most opportunity to improve efficiency within a boiler feedwater system. Sizing the pump correctly, planning how to protect the pumps against low-flow conditions and discussing how the pumps will operate with the pump applications engineer is a great place
to start.
Often the person who is tasked with sizing a boiler feed pump is given the flow, the required head, net positive suction head available (NPSHa) and the temperature of the fluid. While this information is vital, a conversation discussing normal operating conditions compared to the rated conditions and the specifics of the application can be invaluable. If the pumps must be rated for 400 gallons per minute (gpm) for peak demand, but the normal operating point is only 300 gpm, this may change the pump selection. Giving the applications engineer (AE) as much information as possible up front allows them to select a pump that will operate efficiently at normal operation as well as at peak demand. This conversation will result in a correctly sized pump that will result in longer pump life, energy savings and longer mean time between failures.
Image 1 shows possible selections based solely on the rated condition of 400 gpm. When given this information alone, a pump applications engineer may select the Size D 6x3x8 pump. Image 2 shows that two operating points are plotted, the rated condition of 400 gpm as well as the normal operating condition of 300 gpm. This information shows that one would be operating further away from the best efficiency point (BEP) and back on the curve with the size D pump, whereas the size C pump would operate in a great spot. This seemingly small piece of information completely changes pump selection and saves users from a bad selection.
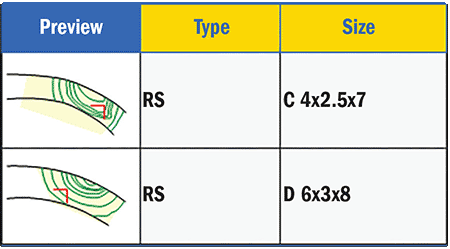
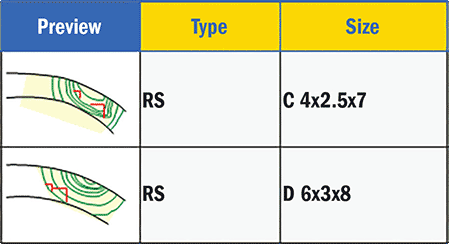
Another way to increase the efficiency of a boiler feed pump is to plan for how minimum flow will be handled. A sure-fire way to shorten the life of boiler feed pumps is to run them below the manufacturer’s published minimum flow or minimum continuous stable flow (MCSF). When a centrifugal pump is operated below the recommended flow, it can suffer from overheating, cavitation and can be permanently damaged if run dry. There are many ways to avoid this and protect
the pump.
The most common way is to size an orifice and recirculation line for the minimum flow and continuously recirculate the minimum flow back to the deaerator. This is probably the simplest way to ensure the pump will never operate below its minimum flow, but there are costs associated with this.
First, the additional flow must be added into the sizing calculations. If the boiler requires 100 gpm and the min flow for the selection is 35 gpm, the pump must be sized for 135 gpm.
This small increase can lead to selecting a larger pump, more stages in a multistage pump and even an increase in NPSH required (NPSHr). This larger pump means increased front-end cost.
Second, there is an energy cost associated with pumping an additional 35 gpm continuously. The energy cost per hour for pumping water can be calculated as shown in Equation 1.
Another way to handle the minimum flow is through use of an automatic recirculation (ARC) valve. The primary purpose of an ARC valve is to ensure that minimum flow is always guaranteed through the boiler feedwater pump. ARC valves are sized specifically for the pump they are paired with. As flow decreases, pressure increases. The valve is sized so that a spring-loaded bypass opens as the pressure increases. This allows the minimum flow to bypass only when the pressure is high enough to open the valve. ARC valves can be an added expense on the front end, but pay for themselves in energy savings rather quickly.
Some users will take the principles used for an ARC valve but use modulating valves with a dedicated pressure transducer to perform the same function. When a pressure transducer reads that the pump is producing less flow/more pressure, it triggers a modulating valve to open and allow a minimum flow to recirculate back to the deaerator.
Another option would be to use variable frequency drives (VFDs) to slow down the pump as less demand is required to the boiler. Pumps require less flow at reduced speed, and VFDs with some programming can protect the pump while offering energy savings at the same time.
If a VFD is planned for use, this information should be shared with whomever is sizing the pump. If the applications engineer knows that VFDs will be used, this can sometimes allow them to use full diameter impellers instead of trimmed impellers. A pump with a VFD can be slowed down to meet a condition point rather than impellers being trimmed. Sticking with full diameter impellers allows the pump to be a little more efficient, as there will not be as much room for internal recirculation at each stage.
Once it has been decided how minimum flow will be handled and how the pump will be operating (fixed speed vs. VFD; rated flow vs. normal operating flow), a selection can be made. A good selection for a boiler feed pump should have its normal operating point as close to the BEP as possible and a good margin between NPSHa and NPSHr.
It is easy to rush through the request for quotation process, especially in emergency situations, but taking a few minutes to communicate with a professional about the sizing and operation of the next boiler feed pump can save technicians from headaches and save the company money.