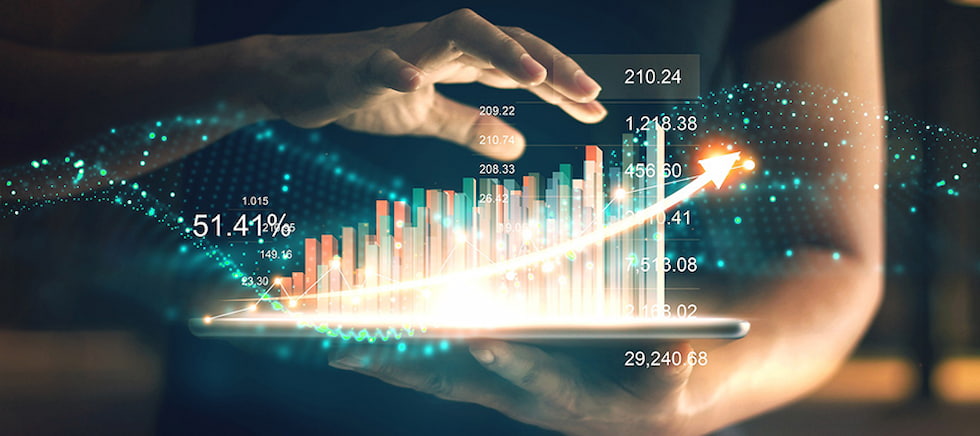
For plants with critical industrial processing machinery like pumps and valves, utilizing a condition monitoring platform has become synonymous with saving money, reducing downtime and keeping operators and the environment safe from corrosive materials and faulty equipment. However, many companies still rely on their reliability or equipment engineers to gather and analyze the vibration data that is collected by these sensors, adding an important and time-consuming task to their list of responsibilities and risking inadequate analyses of information by those who do not have specialized knowledge.
That is where the concept of full-service monitoring comes into play. As innovations make monitoring more precise, more complex and faster in data collection, relying on qualified analysts is more important than ever to mitigate potential risks of disruptions or machinery malfunctions in plants across the oil and gas, chemical processing and power generation industries. Due to this, leading sensing and monitoring service providers are expanding their offerings to include full-service, premium solutions, which include the frequent analysis of data by specialized, highly trained analysts who are able to debrief users on potential issues and solutions before operations are interrupted.
This service is offered as an upgrade when purchasing monitoring sensors, and there are countless benefits of taking advantage of this full-service solution.
Benefits of Opting for Premium Service
The most significant benefit of utilizing a premium service from a sensing and monitoring provider is it allows users to identify an issue and receive counsel on the best solution so it can be swiftly remedied. Better yet, it allows engineers to focus on other, more important responsibilities than keeping track of the data collected by modern day monitoring solutions, which now track data in near real-time.
Another plus to utilizing this service is that, while most sophisticated systems auto-generate recommendations about potential ways to mitigate detections of a machine malfunction, the insight does not compare to the level of detailed investigation users receive from an experienced analyst. Service provider analysts can bring their broader experience across industries and collective knowledge from multiple users to the machine condition monitoring needs of each site.
Due to their exclusive focus on this role, they will automatically stay updated on the latest methodologies and best practices. Analysts regularly comb through data and inform the user on the health of their pumps and systems, including raising concerns about unusual data sequences that should be further investigated and how. While overall site status is typically reviewed in a monthly cadence, analysts are alerted in real-time by sensors when there is an urgent issue, allowing them to act immediately to determine the issue and counsel users on urgent action.
Premium monitoring offerings also include field service needs. In lieu of sending sensors and instructions for setup to the user, engineers and technicians will come on-site to install the full system and make sure it is set up optimally for that location and delivering the data needed to make the most accurate analyses. Any hardware that is not functioning optimally or needs maintenance can be promptly handled by the provider’s field service department.
The service team can ensure the proper facility personnel are trained on how to use the system and service while guiding them on how best to utilize the information they are now getting. This will improve facility efficiency and uptime without employees getting overwhelmed or frustrated.
Having access to specialized user care allows support teams to grow, so more in-house engineers will not have to be hired to stay on top of monitoring needs as business expands. Furthermore, in the time it would take an operator to collect and decipher data and identify a machinery malfunction, specialized analysts can review the data, identify the issue and send relevant information directly to the repair/maintenance department to troubleshoot the issue and order replacement parts, significantly reducing overall downtime.
Real-World Risk Mitigation
Many processing plants, especially those that deal with corrosive materials, are already utilizing premium monitoring services to ensure the safety of their employees and the environment. In one notable instance, an oil and gas user had a main pump conducting processing, with a couple of backup pumps available for the application should they be needed. Specialized service analysts were conducting a regular review of the main pump’s performance data when they identified a series of high vibrations that were collected by the sensor, which indicated an equipment failure.
Analysts brought it to the user’s attention right away, and they determined immediate action should be taken to avoid catastrophic damage to the pump. The analysts swiftly coordinated with their repair shop to have the main pump removed from the service line for repairs, while the user switched to a backup pump in the interim.
Repair professionals determined that part of the pump’s impeller had broken off and was still inside the pump, which could have caused the pump to come apart completely had there been further increases in flow or pressure. Because this client had opted for a full-service solution, a potential safety and environmental incident was completely avoided and there was little to no interruption to operations.
The Future of Full-Service Solutions
As premium services are utilized more frequently by industrial users, it is likely the convergence of data will continue to evolve. Right now, monitoring solutions separate vibration and process data into different domains and analyze them individually. In the future, it is likely this data will come together, prompting the use of tools like artificial intelligence (AI) to aid in the processing of large amounts of data more efficiently. This will allow for more flexibility of operations than ever before.
Another potential innovation on the horizon is the creation of one central location to store performance data. This may include the interoperability of systems from one provider or multiple providers to access data in real-time and across several locations. The standardization of tools like wireless networks and gateways will enable users to collect and share data across their plants faster than ever before, potentially allowing for monitoring software to perform centralized analytics and effectively share that data back with the user.
However, in order for data convergence like this to be conducted accurately, suitable infrastructure is required. For that reason, it is likely these capabilities will be available primarily to new plants and users who build their facilities with cutting edge data processing capabilities in mind.
Machinery and data collection continue to become more sophisticated, creating a greater need for oversight by specialized experts to ensure the continued health of industrial equipment. Opting for a premium, full-service monitoring solution allows users to reduce downtime and equipment costs while mitigating issues at the first sign of risk, all without monopolizing time from on-site engineering staff. Asking a monitoring platform provider about full-service options can keep employees and bottom line, as well as the environment, safe from the consequences of costly equipment malfunctions.