The construction, seals and protective monitoring contribute to the motor’s ability to operate in and under water.
04/01/2014
A basic electrical safety rule is that water and electricity do not mix. However, alternating current (AC) induction motors must function in or under water to operate pumps, mixers and aerators in industrial water and wastewater applications. Submersible motors must be specially designed and manufactured to prevent water from contacting any part of the electrical circuit while providing long life in these harsh applications.
Design
A submersible motor is completely enclosed and non-ventilated. It does not have an external shaft-mounted fan to cool and dissipate the heat from the frame. In wet pit applications, it relies on the liquid in which it is submerged to dissipate the heat from the frame. Its duty cycle is continuous in water with a 15-minute capability in air. In dry pit applications, the motor may run for prolonged periods of time in air and submerged. Because the air does not dissipate heat as well as liquids, the frame usually must be oversized so that more surface area is available to move the heat away from the motor. The potential for the presence of flammable gases or liquids and combustible dusts can also affect the design of motors that operate in water and wastewater applications. Methane gas is formed by decomposing solids. It is potentially explosive when present all or some of the time and could require a motor to carry a Division 1, Class I, Group D certification. The user is responsible for specifying the hazardous area certification requirements of the motor. They can reference the National Electrical Code (NEC) National Fire Protection Association (NFPA) 70, which defines the hazard rating of the space or envelope. They can also reference the Standard for Fire Protection in Wastewater Treatment and Collection Facilities (NFPA 820), which defines the hazard and classification for the process areas.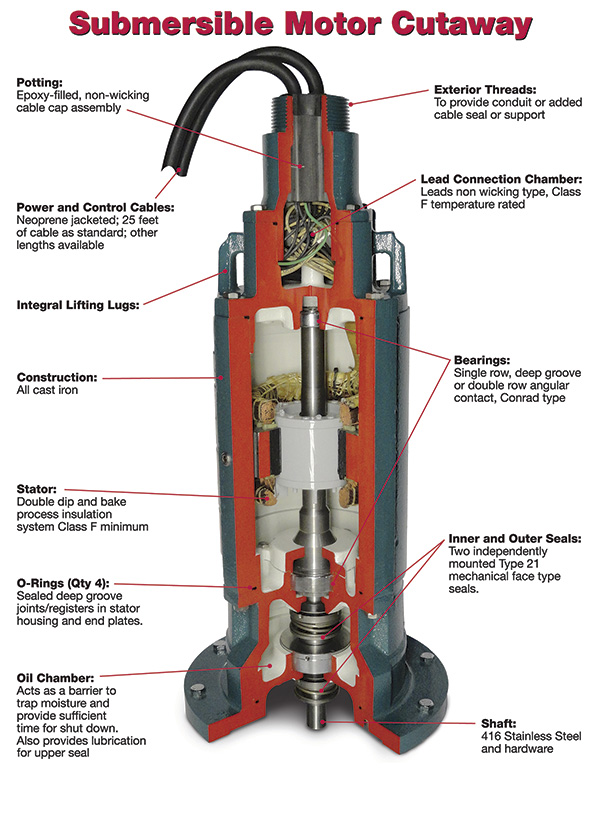
Construction
Heavy-duty cast iron frames should be used when constructing submersible motors. Cast iron provides good protection in an industrial environment because it does not dent, deflect or bend easily, which could cause failure of the sealed enclosure. The frames are precision machined for tight fits between parts. All machined fits have groove and O-rings to prevent water from entering the motor. A non-wicking cable cap assembly securely attaches and seals the power leads to the frame. The power cable entering and exiting the cable cap should be separated by a butt splice, and the whole cap assembly is then filled with an epoxy rubber grommet to seal it. The cable cap seal must be robust because the cable will be flexed in many directions during motor transport and installation. The cable should never be used to help pull or lift the motor because this could cause the seal to fail, allowing water into the motor.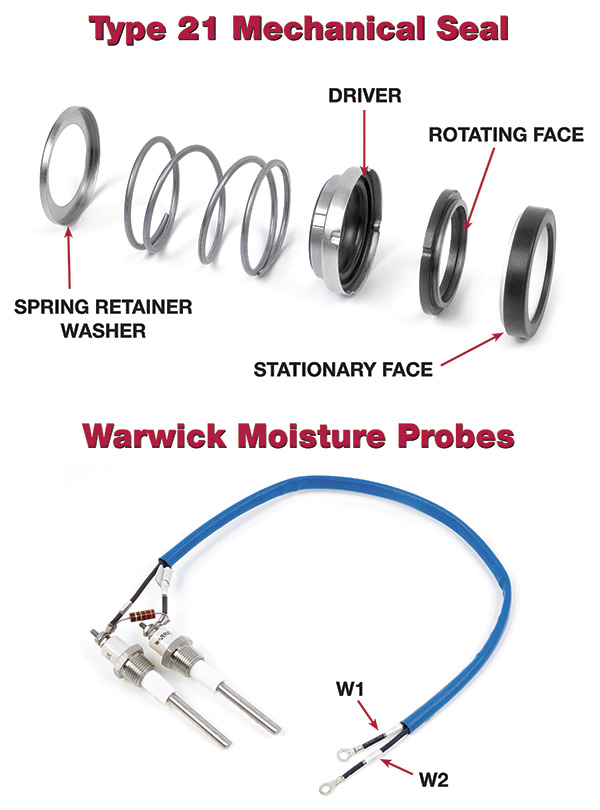
Seals
Type 21 mechanical shaft seals are often used for submersible motors. This all-purpose seal rotates with the shaft against a stationary mating face and eliminates adhesives by using mechanically crimped components. To securely seal the output shaft and protect the motor, submersible motors have an inner and outer seal arrangement on the drive-end plate. The drive-end plate on submersible motors is different from that of a standard induction motor. A submersible motor’s drive-end plate is hollow and designed to contain an oil chamber and moisture probes. An inner seal is mounted inside the oil chamber where the shaft enters the stator frame, and lubrication is maintained by the oil in this chamber. The outer seal is mounted outside the endplate where the shaft exits the frame and is coupled to the pump. It is lubricated by the pumped liquid. The outer seal must tolerate surface abrasion on its outer surface that results from contact with the pumped liquid. The higher the viscosity of the liquid, the more abrasion occurs. Type 21 seals are available in several stocked materials to meet specific operating conditions. The pump manufacturer typically specifies the seal material that is best-suited for the pumping application and will provide the longest seal life. Typical type 21 seal materials include:- Carbon ceramic-faced seals are general purpose, stainless steel seals that are typically used in food processing, petrochemical and wastewater applications with relatively clean effluent.
- Tungsten carbide-faced seals are popular types that provide harder seal faces for more demanding applications in more viscous fluids.
- Silicon carbide-faced seals are typically used for the most demanding slurry type (highly viscous fluid) applications.