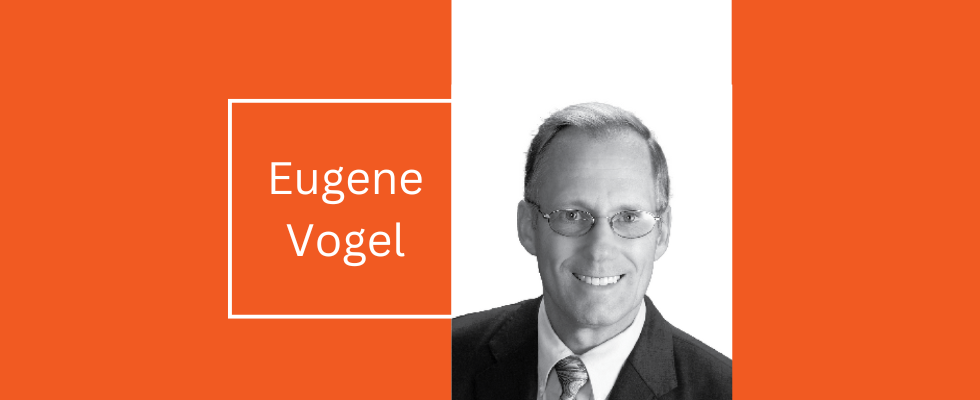
Maintenance departments and service centers often repair submersible pumps, almost all of which have dual seals—an upper (inner) seal and a lower (outer) seal—separated by a chamber (cavity) filled with a barrier fluid (Image 1). Usually, the barrier fluid is oil, but some models use a glycol solution. When refilling the chamber, best practice is to use the barrier fluid and procedure specified in the OEM pump manual, but if the OEM manual or the specified fluid is unavailable, here are some general guidelines.
Barrier Fluid Selection Criteria
There are many criteria for selecting barrier fluids, but only a few apply to submersible pumps. For instance, submersibles seldom operate in high ambient temperatures, which makes such concerns irrelevant. For submersibles, the primary purpose of the barrier fluid is to lubricate and cool the contacting seal surfaces, so these are the key selection factors. Since oil and glycol solutions offer good lubricity and cooling properties, OEMs specify those types of barrier fluids for most submersibles.
Another important factor for barrier fluid selection is compatibility with the seal materials, especially the elastomer components. Most seal vendors can provide the compatibility requirements for elastomers and various other seal materials.
A final concern is compatibility with the pumpage and the environment in general. Seals sometimes fail, and barrier fluid can leak into the pumpage. In one case, seal oil from a leaky submersible contaminated a city fountain, necessitating a costly cleanup.
The barrier fluid that pump manufacturers specify most often is turbine oil (sometimes called paraffin oil because of its paraffinic base). The oil must have good lubricity yet flow freely at the pump operating temperature. Since most submersible pumps operate in relatively cool ambient temperatures (Image 2), an International Organization for Standardization (ISO) 32 turbine oil is a good choice. For submersible applications where the pumpage is quite hot or cold, select the appropriate ISO viscosity using the operating temperature data available from oil vendors.
If the application has the potential to contaminate the pumpage with barrier fluid, as in the public fountain example above, food processing applications or similar situations, determine its National Sanitation Foundation International (NSF) classification at nsf.org. Based on that, vendors can recommend barrier fluids with the correct rating and viscosity. Often, submersible pumps for these applications specify an ethylene glycol or a propylene glycol solution (Image 3).
Filling the Chamber
Filling the oil chamber on a submersible pump is not difficult, but there are procedures specific to each pump model that, if done incorrectly, can have severe consequences. For example, when the pump is running, the fluid level must be high enough to flood the upper seal, providing lubrication and cooling. If it is too low, the upper seal will overheat in minutes and be ruined. There must also be an air pocket above the fluid level to accommodate thermal expansion of the fluid. If the chamber is overfilled and the air pocket is eliminated, excessive pressure will cause seals to blow out and fail. Always follow the filling procedures in the OEM manual for the specific pump.
Filling a submersible pump to the correct level with the proper barrier fluid is one of the easier tasks for pump repair. But it is not a task that should be ignored. Consulting the OEM pump manual, adhering to the guidelines offered here and working with barrier fluid and seal vendors will ensure the simplest part of the repair doesn’t result in a premature failure.