Upgrading a system at a dam while also protecting the fish and wildlife in an area can be a challenge. The San Francisco Public Utilities Commission (PUC) recently faced this dilemma at Cherry Dam, which is part of the Hetch Hetchy Regional Water System, located three and a half hours east of San Francisco on the border of Yosemite Valley, California. Cherry Lake provides drinking water for the greater San Francisco Bay Area. The outlet facilities at Cherry Dam, which were built in 1956, reached the end of their service life and, to satisfy stream-release requirements established by the U.S. Department of Interior, the 66-inch hollow-jet valves had to be removed and replaced. PUC contracted Anvil Builders, a San Francisco-based general contractor, to coordinate the Cherry Dam Project. According to Anvil, the initial project involved removing and replacing two large 66,000-pound valves and also the replacement of various ancillary components. This included the installation of reinforced-concrete deck gussets and overhead pipe supports in the valve-house; demolition of the existing instream flow-release system; installation of the new downstream flow-release system, including piping, valves and fittings; and the removal and replacement of the alternating current (AC) distribution panel and lighting systems. But as Anvil’s team prepared to work on the replacement of the two hollow-jet valves, they discovered a problem. “In order to replace the hollow-jet outlet valves, we needed to close two other butterfly valves that were holding the reservoir water back,” said Caleb McWaters, Anvil project manager for the Cherry Dam Project. “In the beginning of the project, we discovered that the butterfly valves were not working, so we had to get in to fix them as well.” For safety, the reservoir had to be drained below the intake tower, allowing dry access to the butterfly valves. However, with the water level lowered below the intake tower, no water was flowing over the dam. The challenge was to keep water flowing into the stream below the dam to support the downstream fish and wildlife while diverting water away from the repair work being performed on the valve system.
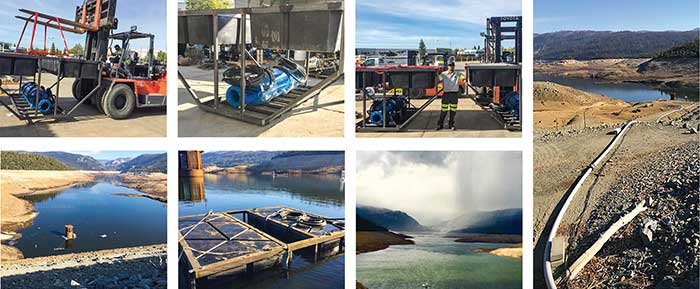