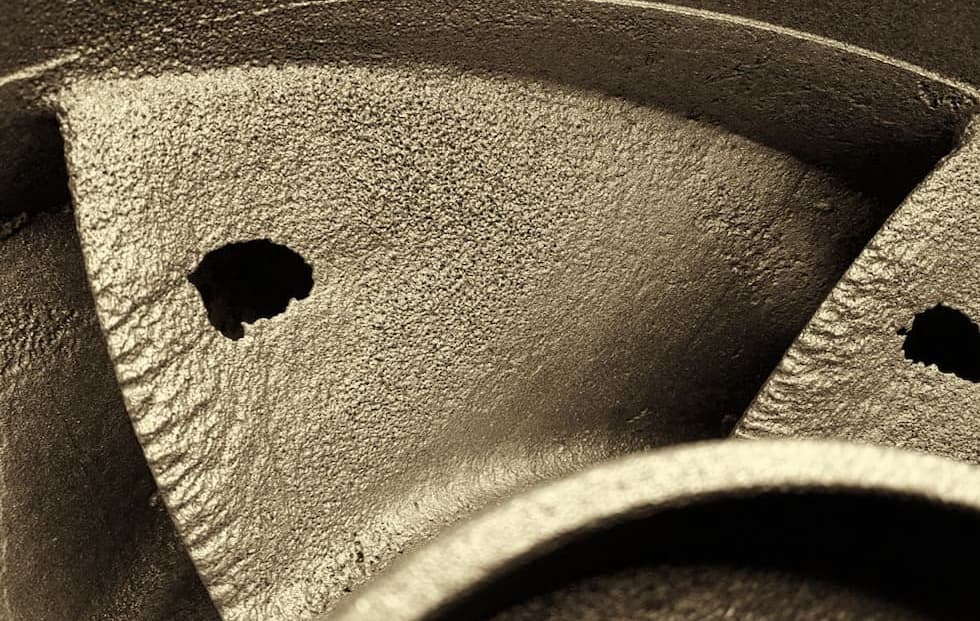
Most pumps used in different industries have been centrifugal pumps. This is because of their flexibility, reliability, favored head-flow curves and reasonable prices. This article discusses key aspects of centrifugal pumps such as suction piping, net positive suction head (NPSH) and cavitation.
Suction piping systems of pumps have always been challenging due to the sensitivity of the pump to the flow pressure drop on the suction and the relatively larger size of the piping used in the suction. On one hand, the suction piping should be straight, simple and short, which is unique to suction piping, to mitigate issues associated with NPSH, and a mandatory minimum pressure should be maintained at the pump entrance to ensure the proper operation of the pump. On the other hand, the piping is relatively larger in diameter, so nozzle load limits are more challenging.
NPSH
NPSH is particularly important to dynamic pumps such as centrifugal pumps. These pumps are vulnerable to cavitation. If cavitation occurs, the drag and friction in impeller vanes increase drastically, seriously restricting the flow and interrupting the operation. Cavitation has many adverse effects on impellers and generally on pumps. Prolonged exposure to cavitation can damage the impellers. NPSH refers to two quantities:
- NPSH available (NPSHa): a measure of how close the liquid at a given point is to boiling, and so to cavitation. NPSHa is usually calculated at the suction flange of the pump.
- NPSH required (NPSHr): the head value at a specific point (usually the inlet of a pump) required to keep the liquid from cavitation in a pump.
An appropriate NPSH margin (NPSHa minus NPSHr) should always be provided for the entire operating range. In other words, the NPSH margin is the NPSH that is available more than the pump’s NPSHr.
Cavitation & NPSH
When a liquid enters the eye of a pump impeller, it accelerates as it is drawn into the impeller. This acceleration creates a pressure drop in the liquid at the impeller eye. If the liquid is close to its boiling point (bubble point), the pressure drop may be great enough to cause some of the liquid to boil. The bubbles that are formed by the boiling liquid enter the pump impeller along with the liquid. As the liquid (and bubbles) flow toward the tip of the impeller, the pressure rises and the bubbles collapse or implode. When these bubbles collapse, a large amount of energy is transferred from the fluid to the impeller at a very small point on the impeller. This energy is sometimes great enough to damage the impeller and is frequently enough to cause vibration and noisy pump operation. This process is called cavitation, and it must be avoided in the operation of any pump.
The damage caused by cavitation depends on several factors such as pump speed, impeller material, amount of cavitation, type of liquid, etc. The type of liquid is particularly important. For example, cavitation in water pumps is usually more serious than in hydrocarbon pumps. This is because water has a much higher latent heat of vaporization than hydrocarbons (say, three to eight times higher). As a result, when the bubbles collapse, far more energy is released causing more damage to the impeller.
Cavitation can be prevented by making sure that the pressure at the suction of the pump is sufficiently above the bubble-point of the liquid to prevent the liquid from boiling as it enters the impeller eye. Pump manufacturers publish NPSHr values for their pumps. It should be ensured that NPSHa is greater than NPSHr at all times.
NPSH Margin
It is necessary to have an operating NPSH margin that is sufficient at all possible flows—from the minimum continuous stable flow to the maximum expected operating flow—to protect the pump from damages caused by cavitation. A key concern is to provide a suitable margin for the maximum expected flow at the right side of the curve where NPSHr is higher compared to its value at the rated flow.
It is difficult to give general advice for required NPSH margin. As a very rough example, an NPSH margin of 2 meters (m) or 2.5 m might be used for ordinary pumps. As another rough guideline, the formula NPSHA = 1.2 × NPSHr + 2 m can be used for NPSH margins and the relation between NPSHa and NPSHr. NPSH margins of 2 m, 2.5 m or 3 m have widely been accepted for small/medium pumps or low-/medium-energy pumps. For high-energy pumps, higher factors and margins should be used. For example, for some high-pressure and high-energy pumps NPSHa = 1.5 × NPSHr + 3 m might be used.
Difficulties & Challenges
NPSH calculations should be done with great care. During the early stages of the development of a plant or facility, the layout is not yet firm. Hence, NPSHa for the pump(s) cannot yet be calculated with confidence. However, preliminary NPSH can be estimated using information from a preliminary layout and elevations. NPSH margins can be changed by later modifications to the layout and particularly the elevations. NPSH plays an important role during the pump selection and could significantly impact the overall cost of the pump if a lower NPSHr pump is specified, since pumps with a lower NPSHr tend to be more expensive. At this stage, the goal usually is to calculate a preliminary NPSH value and provide it to pump manufacturers to get feedback, proposals and values of NPSHr. This allows all involved parties to determine whether a pump with the specified NPSHr can be selected or not. It can be achieved with some modifications to the pumping system layout (higher NPSHa), or it might be achieved by selecting a pump with lower NPSHr. Based on the manufacturer’s feedback, the layout can be modified to have a suitable NPSH margin.
A Booster Pump: Last Solution
For high-speed pumps, such as boiler feed water pumps or high-pressure pumps, NPSHr can be high. High values for NPSHr, as high as 30 m or more, are not unusual for some applications. In these cases, there might not be a way to provide enough NPSH margin and a booster pump might be used to provide NPSHr. All other options should be considered before this expensive solution is employed. This might be the case in revamp, renovation or upgrading developments where elevations are fixed and cannot be increased. Booster pumps are typically low-speed centrifugal pumps with a low NPSHr. They are typically installed to provide 40 to 80 m of head to the liquid.
Considerations for Suction Piping
For pumps, the suction piping is almost always more critical and challenging than the discharge piping, even though the discharge piping operates at much higher pressure and temperature differences than the suction. The diameter of suction piping is more than the diameter of discharge piping. Also, the suction piping is relatively shorter and stiffer than the discharge piping. A discharge piping of a pump can be provided with different loops and flexibility provisions. However, this is not the case for the suction piping.
Often, a simple layout of preliminary suction piping is not adequate to reduce the piping load at the pump suction nozzle and bring them below allowable limits. In many cases, some flexibilities should be included in the suction piping, keeping an eye on pressure loss and NPSH margin. Flexibilities should be accounted for and the required piping length and added bends, loops, etc., should be minimized to keep pressure drop under control.
A Stop at Suction Piping
In some cases, the piping-imposed load on the pump can be reduced by placing stops at strategic locations. The exact location of the stop is determined by the configurations of the piping and nozzle load/piping stress analysis. There have been cases where a stop for the vertical direction was included to limit the reaction load on the vertical direction. This is effective as many pumps have suction piping with a relatively long vertical run.
A Loop in Suction Piping
In some cases, a loop might be needed in the suction piping to deal with extreme temperature differences. Such a loop on suction piping is only acceptable as the last resort. The location of the loop is very important. One may think to place a loop at a higher elevation due to better space and support structure availability. However, when handling near saturated liquid, the high elevation loop can be the cause of many operational problems.
The loop, as the last resort, should be placed at the low elevation section (bottom portion) of the suction piping. Although this portion of piping is generally more congested, the loop should still be placed at the bottom portion in combination with the original bends. Such a combination reduces the number of elbows required. This reduces the pressure loss of the loop.