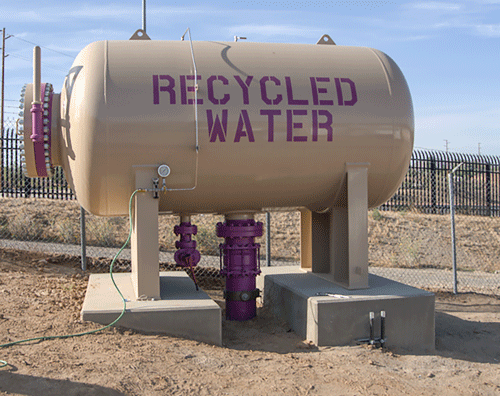
Surge vessels, also called hydropneumatic tanks, are often found on the discharge header of pumps, especially in water systems. Their primary purpose is to mitigate problems with pressure changes when pumps start, change speed and, most critically, when they trip. To be effective, surge vessels must be properly sized, with pre-charge pressures that will work in all operating scenarios. A surge vessel’s pre-charge pressure is the air pressure inside the vessel when the vessel is empty of all liquid. This pre-charge pressure correlates to a specific gas-to-liquid volume ratio during normal operations: high pre-charge pressures result in high gas-to-liquid volume ratios and vice versa.
Vessel size and pre-charge pressure is determined in the design phase with a transient analysis using a specialized computer simulation program that models system pressure and flow changes during transient conditions. Conducting a transient analysis can be tedious, as there are a number of variables and different operating scenarios to consider.
Engineers will often take an iterative approach when conducting a transient analysis, adjusting both the size of the vessel and pre-charge pressure to solve for different scenarios. A common problem with this method occurs when an initial gas volume is specified in the model instead of a single pre-charge pressure that works for all scenarios. Specifying an initial gas volume can inadvertently lead to model results with negative pre-charge pressures or wide varying pre-charge pressures, either of which would be impractical in the field. This pitfall can be avoided by specifying a single pre-charge pressure that will work with all scenarios.
When modeling for different operating scenarios, engineers will analyze the vessel’s liquid volume to determine whether the vessel is becoming too full under high-pressure conditions or too empty under low-pressure conditions. The general rule is to maintain at least 20% liquid by volume and not exceed 80% liquid by volume.
Under high-pressure conditions, a surge vessel may have little room for gas compression and therefore be less capable of mitigating high pressure surge waves, leading to system pressures that exceed design pressure ratings. Additionally, high-pressure conditions put the bladder in bladder-type vessels at risk of damage. In “gas in the bladder” applications, the bladder will compress in on itself, whereas the bladder in “liquid in the bladder” applications will expand and push into open spaces such as couplings or nozzles.
Under low-pressure conditions, the risk of air being introduced into the pipeline exists if the vessel is too empty. This is true for bladderless (air over water) tanks but can also occur in bladder vessels where the bladder is damaged—a likely occurrence in an empty vessel, as the system effectively works to pull the bladder out of the vessel.
In the Field
Surge vessels should be sized such that the pre-charge pressure can vary within an acceptable range so as not to impact the vessel’s performance in the field. One way to accommodate for a broader range in pre-charge pressure variances in the field is to increase the vessel’s volume in the design phase. A broader range in variances is highly recommended, as pre-charge changes in the field will occur due to temperature fluctuations, trapped air, slow air leaks and even the speed at which the vessel fills or empties.
Temperature. Changes in ambient temperature and system operating temperature can be demonstrated mathematically using Gay-Lussac’s Law:
Using this formula, if the pre-charge pressure was initially 20 psig at 60 F and the temperature increased to 80 F, the pre-charge pressure would increase to 21.3 psig under standard atmospheric pressure.
Trapped Air. For bladder vessels, trapped air on the fluid side of the bladder is a factor that leads to lower-than-expected liquid levels—i.e., a higher gas-to-liquid volume ratio. Trapped air also leads to faulty readings in the field, such as pressure and liquid level readings. To avoid problems, operators will often burp the bladder periodically to release any trapped air.
Air leaks. Operators routinely inspect surge vessels for small air leaks. One basic method to identify leaks is to monitor the liquid level over time. If the liquid level rises steadily even though the line pressure is consistent, a slow leak in the pre-charge is likely. Another way to inspect for leaks is to perform a bubble test on the vessel and any connections. It is of note that often, especially in water applications, small leaks over time can lead to a negative pre-charge. In the field, as the vessel drains, operators may observe intermittent moments where no fluid is coming out and a loud whooshing sound occurs as the vessel draws air in. Much like the walls of an inverted two-liter bottle of soda are drawn in as the soda glugs out, the walls of a surge vessel will attempt to contract and expand as it equalizes to atmospheric conditions during the draining process. For this reason, it is common for surge vessels to be designed to full vacuum.
Liquid Fill/Empty Rate. Another factor contributing to pre-charge pressure variances is how quickly a vessel fills or empties during normal operations, and more importantly, during transient conditions. Although less intuitive than other factors, the rate of gas compression or expansion impacts the gas volume and pressure ratios. If the change in gas volume is rapid enough, the gas will heat or cool (an adiabatic process), and then the polytropic constant comes into play. Engineers will use estimates in the transient analysis, such as the typical values as shown in Image 2, for diatomic gases like air or nitrogen.
Going Forward
Understanding the importance of pre-charge pressure, advice for managing the design or field operations of a surge vessel is to not only expect change in the pre-charge pressure, but to design for it, actively look for it in the field and have a response plan when the pre-charge pressure is outside the preferred range.