In the remote Libyan desert, an oil and gas producer reduced diesel transport costs and accident risks by upgrading their power plant.
09/21/2015
A subsidiary of BASF, Wintershall is Germany's largest global petroleum and natural gas producer. The company has been active in oil exploration and processing (E&P) in Libya since 1958. Today, more than 1,000 kilometers (km) south of Tripoli in the Libyan Desert, eight onshore oil fields are producing in the C 96 and C 97 concessions. The company also has a share in production from the Al Jurf offshore platform off the northwest coast and holds a license for another exploration area in the southeastern region of the country.
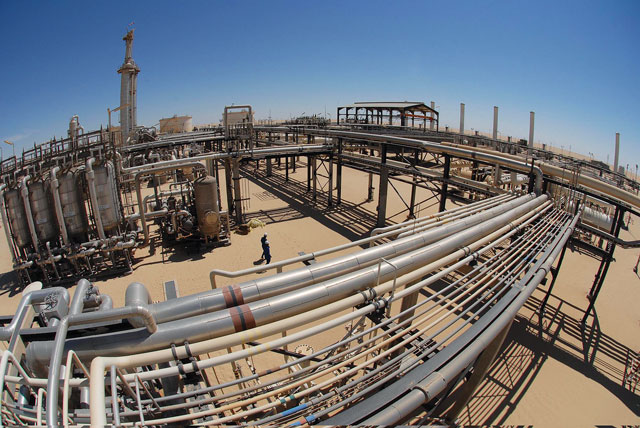
Power in the Desert
A new water injection process spiked energy demand at the Nakhla and Hamid sites. The Hamid plant consumed 40,000 liters of diesel per week—all transported by truck. Truck transport costs and the risk of accidents increased exponentially as energy demand grew. If a truck did not arrive on time, the resulting power outage would lead to costly production shutdown. Rather than upgrading the remote diesel power plant at the Hamid site, Wintershall centralized electricity generation at the Nakhla site only 26 km away. The site's GOSP used the associated gas available for electricity generation. A new high-performance gas turbine with a rated power of 7 megawatts (mW) equipped with a synchronous generator was installed to handle the increased demand. High temperatures and frequent sandstorms led to stringent requirements for the electrical equipment. Sand deposits in the generator had to be prevented, and fine sand particles, which can penetrate even the smallest cracks, had to be removed immediately to prevent damage. The site's remote location meant that spare parts were not readily available. All building materials had to be transported to the site—even concrete, which could not be mixed on-site because the sand was too salty.Continuous Power
With a capacity of 10.2 megavolt-amps (MVA), the synchronous generator runs autonomously and has already run for more than 20,000 hours in continuous duty. A custom model, the generator took approximately one year to build. It features a top-mounted air/air heat exchanger and external fans. The air filter is designed to prevent sand accumulation, with all sand particles removed directly through slits. Additionally, the four-pole generator—with IP55 protection rating—is designed for a voltage of 6,000 volts (V) at a frequency of 50 hertz (Hz) and for temperatures up to 55 degrees Celsius. The white paint further minimizes heat absorption. A 30 kilovolt (kV) overhead line connects Nakhla to the diesel power plant at the Hamid site, providing power supply redundancy. The GOSP can now be operated from the gas turbine and generator or from the conventional diesel power plant in case of emergency. The 14 mW of surplus heat from the gas turbine is now used to heat the extracted oil up to 70 C in place of five hot water boilers. "High operational reliability and availability were our main concerns when selecting the generator," said Rainer Bleich, project manager at Wintershall. "In part, that's because electricity generation is vital for the continuous operation of our GOSP in Nakhla. Every day of downtime can cost us millions of Euros."Adaptable to Harsh Conditions
Since switching to the gas turbine and synchronous generator solution, Wintershall has experienced significant benefits. The site's overall operational security has improved with reliable, autonomous and redundant electricity generation. In addition, the new generating system requires considerably less maintenance than the previous diesel power plant.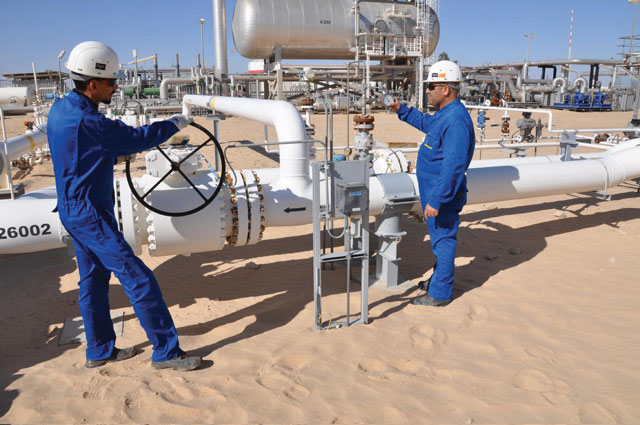