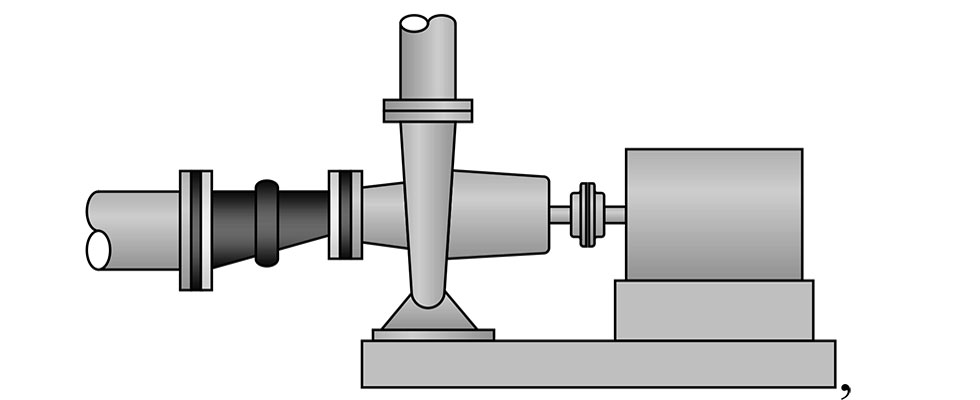
Elastomeric expansion joints, unlike piping expansion joints of other materials, can be manufactured with concentric or eccentric tapers, transitioning from a larger diameter on one side and smaller on the other. These expansion joints are normally hand-built on a mandrel and not of the molded variety. The low volume requirements and nonstandard lengths do not support the high cost of mold tooling.
Before moving forward, it is important to define and clarify the difference between concentric and eccentric tapered reducers:
The concentric design is where the center of each flange is concentric or in line with each other (Image 1).
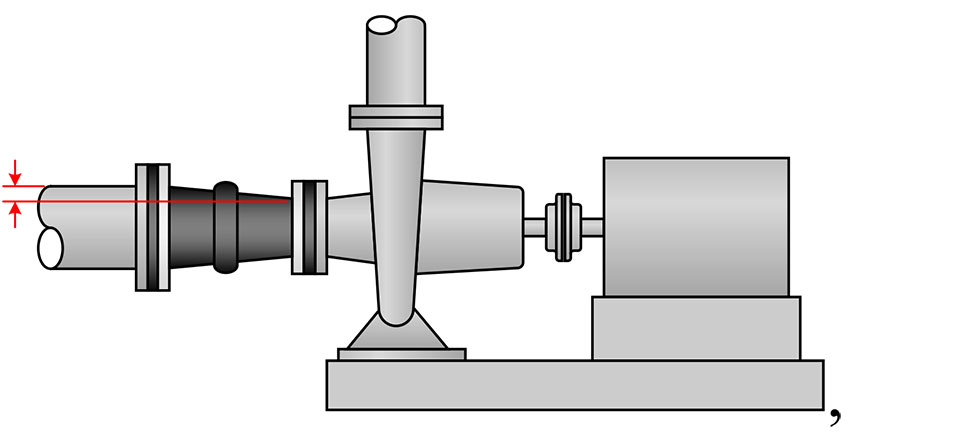
The eccentric design is where the center of each flange is eccentric or offset with each other (Image 2).
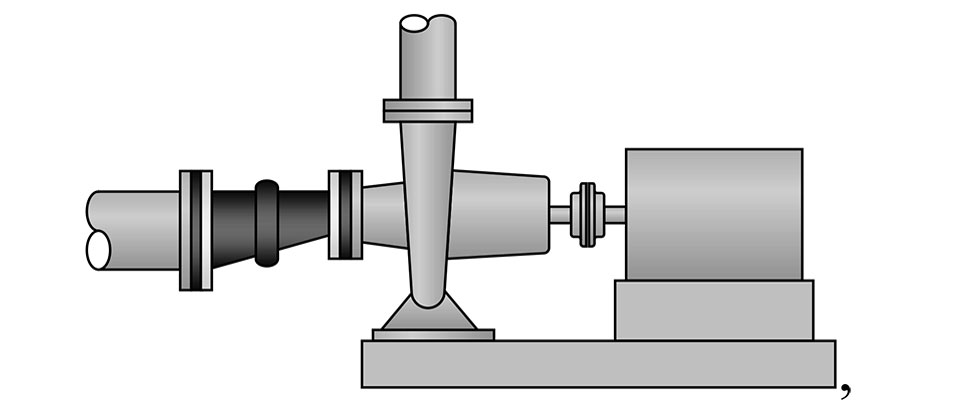
A concentric reducer tapers equally around the full circumference of the joint. Eccentric reducers taper on one side only. The maximum taper angle is twice that of an equivalent concentric reducer since the taper is on one side only.
Concentric reducers are usually found on the discharge side of a pump and eccentric reducers on the inlet. The eccentric expansion joint prevents the formation of an air pocket in a pump’s suction piping, an undesirable scenario that can result in pump cavitation.
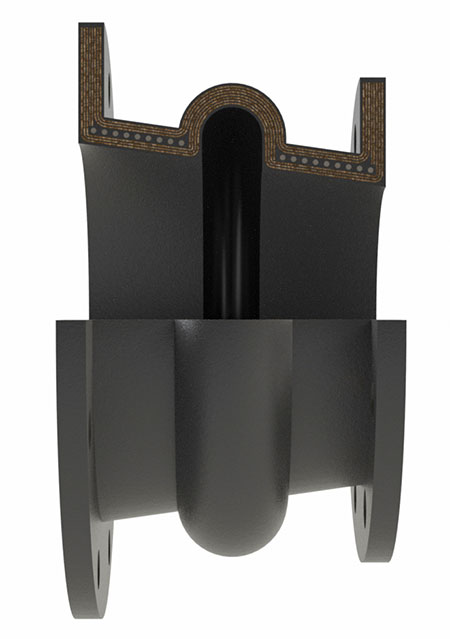
Flow interruption and high-pressure drop dictates that the taper in the expansion joint should never exceed 20 degrees for concentric and 10 degrees for eccentric reducers. This also holds true for standard steel tapered reducers. Exceeding the taper angle would most likely lead to a system malfunction or premature failure in the rubber joint itself.
Like most innovations, tapered rubber expansion joints have both advantages and disadvantages in real life applications. One advantage is that users can accommodate for pipe motion/vibration and pipe size reduction with one product. This can lead to possible cost reduction, which in some cases may be true. Both functions can be accomplished in a shorter face-to-face dimension. This shorter face-to-face requirement is often just a necessity. In some instances, the combined length of a standard steel pipe reducer and a standard straight rubber expansion joint is too long to be implemented in the piping system.
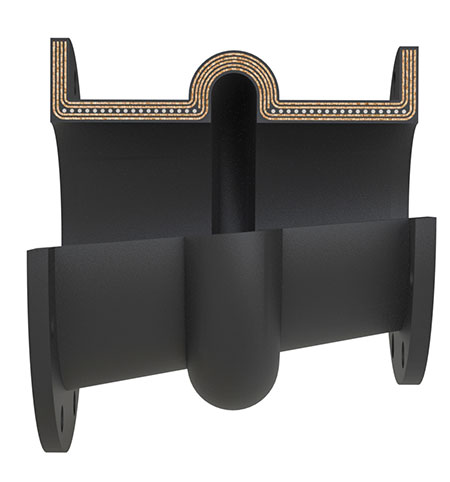
A disadvantage in rubber tapered reducers is the expansion joint arch is not perpendicular to the pipeline. The result of this is it cannot accommodate the same movements as that of a standard straight expansion joint. There are ways to overcome this potential deficiency. Higher degrees of engineering input, such as consideration of reinforcement ply angle and testing to deal with the uncentered arch, are available.
Since tapered expansion joints are hand-built, the cost of these products can be quite high. In some instances, even though one product handles both requirements, cost may exceed that of a steel reducer plus a standard molded straight joint. If the pipe material is more exotic than carbon steel, it is likely that the rubber tapered joint cost will be below that of the combination of a hard pipe reducer and a standard straight expansion joint.
One disadvantage with the use of elastomeric reducers is product availability. Since the product is hand-built and labor intensive and the wide variability of size and dimensions means little or no inventory, the chances of finding the exact reducer that is needed are difficult.
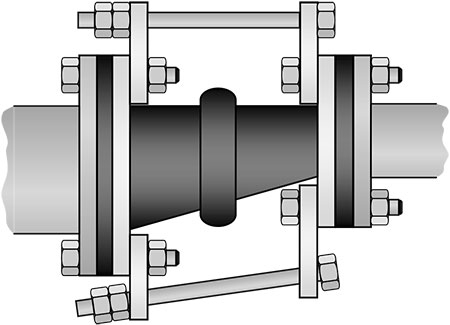
It is not unusual for deliveries of tapered reducers to be in the eight- to 10-week range. That will not work if a failure occurs. If a spare is not available, then overtime can come into play, which can almost double the cost of a normal lead time part. There are some important things that an operator needs to consider when incorporating or replacing elastomeric reducing expansion joints into the piping system. At the top of the list is, “Is the reducer concentric or eccentric?” Attempting to replace a reducer with the incorrect taper can be disastrous.
When considering the pressure capability of a reducing expansion joint, use the pressure rating of the large end or lowest rating of the two dimensions. Installation considerations for reducing expansion joints are the same as that of standard straight joints.
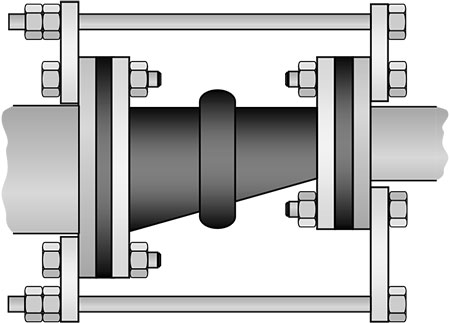
An important consideration is situations where control rods are required. In order for the control rods to function correctly, it is important that the triangular gusset plates are sized correctly to maintain the same outside plate diameter at each end of the expansion joint. A control rod that is installed at an angle can cause binding upon compression, extension and lateral offsets. Image 5 shows an improper installation of the gusset plates with mating flange interferences. The expansion joint supplier should know what gusset plate heights are needed to accomplish this. These heights are pre-engineered and are standard no matter who the manufacturer is.
The ability to manufacture one product to achieve flexibility plus a concentric or eccentric reducer is unique using elastomeric materials. Use of reducers is often determined by available space or simply a replacement of an existing product. Like most things, personal preference comes into play. There is really not a right or wrong choice, but hopefully some of the things mentioned in this article will help in the decision-making process. Ending up with a product that accomplishes the system requirements with the longest life span possible is the ultimate goal.
We invite your suggestions for article topics as well as questions on sealing issues so we can better respond to the needs of the industry. Please direct your suggestions and questions to sealingsensequestions@fluidsealing.com.
Read more FSA Sealing Sense articles here.