At first glance, the sleek and sculptural 21-story Astor Place tower in New York City appears out of place in the heart of the bohemian East Village. But true to the spirit of the neighborhood, Astor Place is challenging convention and advancing the ideals of energy conservation and sustainability. These advancements were accomplished through a collaboration among a water technology company, building manager Related Management Co. and the Sustainable Engineering Lab at Columbia University, to test assumptions of energy efficiency in a retrofit of the building’s hydronic heating, ventilation and air conditioning (HVAC) system, later documented in a doctoral dissertation. The Astor Place Energy Improvement Project consisted of three primary steps: conducting an initial energy assessment of the hydronic system, updating the system with technologically advanced pumps and controls and adjusting the system in real time to evaluate the effects of the HVAC modifications. The impact of energy efficiency improvements is often difficult to demonstrate at the individual system level because buildings typically get billed for energy use at the building level. According to Luke Falk, assistant vice president at Related and an adjunct professor at Columbia University, the partnership among the water technology company, building manager and Columbia University allowed stakeholders to gain a granular understanding of exactly how much energy they would save by implementing a complex HVAC enhancement. The key finding from the testing was that right-sized pumps paired with variable frequency drives (VFDs) powering the chilled water portion of a hydraulically balanced system can deliver a 95 percent reduction in pumping energy, far exceeding the team’s expectations.
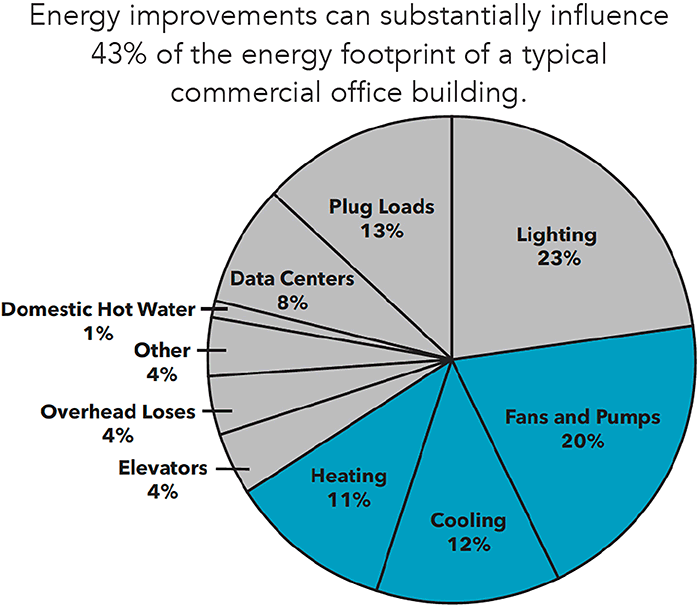
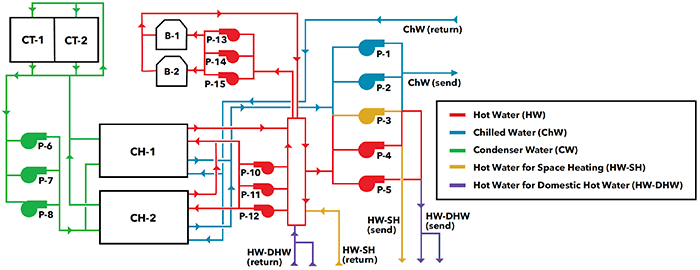
The Test Subject
Astor Place was developed by Related Companies and completed in 2005. It includes 39 residential units with commercial space on the building’s first and second floors. The HVAC system uses hydronic space heating through boilers and cooling with central absorption chillers. Fan-coil units provide HVAC to residential floors; HVAC in the common and commercial spaces employs air-handling units. Only the central plant equipment and air handling equipment in the commercial and common spaces were included in the retrofit and subsequent evaluation. The approach to the ChW and hot water (HW) systems was nearly identical, though monitoring was more comprehensive on the ChW systems, the details of which are outlined here.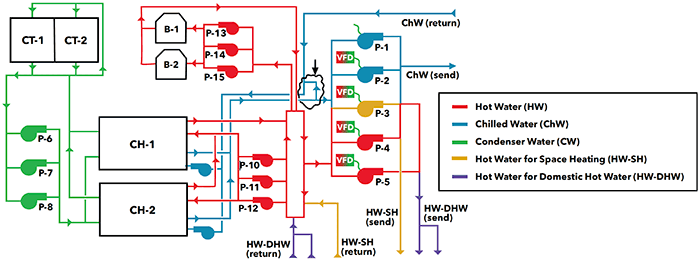
Energy-Savings Opportunity
Prior to the retrofit, nearly 30 percent of the building’s common system utility costs were for pumping electricity, due primarily to the pumps being oversized for the demands of the system and the constant speed operation at partial loads. Oversized pumps were found to cause unnecessarily high pressure differentials and flow rates in the system. Oversizing pumps is a common industry practice. There are a number of reasons why, including adding safety margins beyond those factored into the design by pump manufacturers and accounting for marginal over performance at system peak loads. However, this common practice comes at a cost—namely increases in the system’s operation, maintenance and capital costs over the system’s life cycle. When considering both heating and cooling, the retrofit resulted in a computed annual pumping electricity usage of 316 megawatt hour (Mwh), a 41 percent improvement in pumping energy requirements and an estimated 12 percent reduction in the building’s central operations’ energy bills. Commercial buildings account for 36 percent of all U.S. electricity consumption and cost more than $190 billion in energy every year, according to the U.S. Department of Energy. With more than 80 percent of the existing commercial and institutional buildings in the U.S. expected to operate beyond 2030, as reported by the Colorado-based Rocky Mountain Institute, demand for HVAC system retrofits will be great. The existing environment presents an opportunity for saving energy, creating better value for building owners and promoting sustainability. In addition, the populous states of New York and California have in place some of the country’s most stringent environmental policies—much stricter than existing federal rules—dictating that efficiency will continue to be a major consideration in selecting equipment for retrofit projects, regardless of potential federal policy changes.The VFD Story
Centrifugal pumps installed in HVAC systems typically operate in variable load applications that see a fluctuation of flow requirements based on the heating or cooling load of a building at any given time. The original pumps specified for Astor Place were running at constant speed along with being oversized for the true operational demands of the building. VFDs were the perfect solution to address the pump oversizing. Even at peak cooling load, electricity reduction was more than 50 percent compared to constant-speed pumps, according to the test data. VFDs do bring the most benefit in terms of energy consumption. The pumps consumed just enough energy to provide proper service for that part of the cooling loop.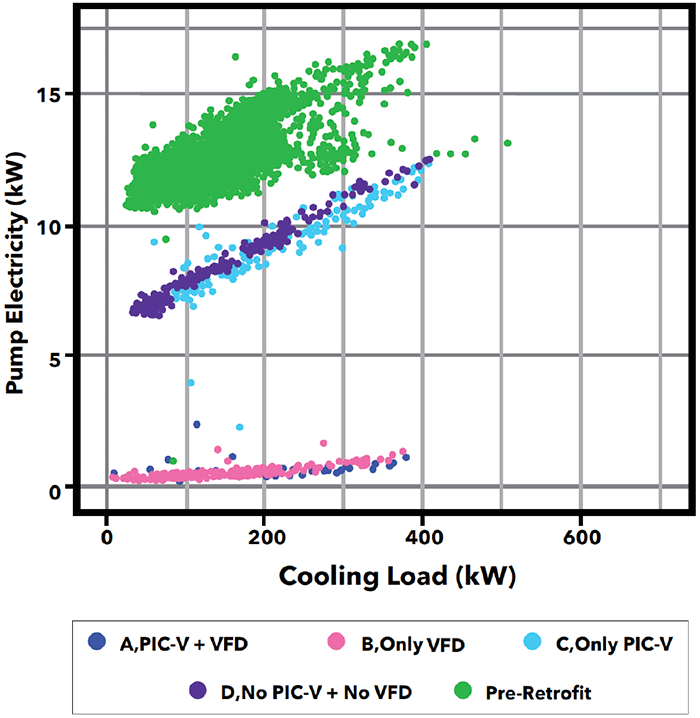
- VFD and pressure independent control valves (PICVs) in operation (final post-retrofit condition)
- VFD in operation; original air handling unit (AHU) valves
- VFD bypassed; PICVs in operation
- VFD bypassed; original AHU valves (replacement pumps and primary-secondary loop modification only)
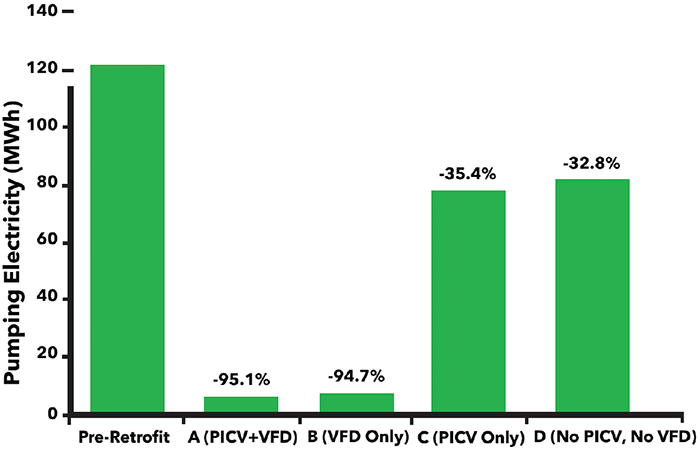
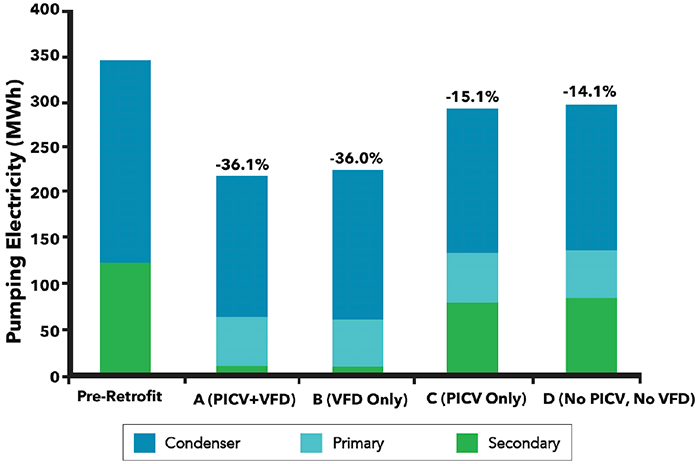
Doing the Math
With all retrofits considered, the total annual cooling pumping energy reduction was computed to be 36.1 percent compared to the original system (see Image 6). The data analysis of the pre- and post-retrofit conditions formed the basis for the mathematical model to assess energy consumption, calculating the following:- pump power at thermal loads within monitoring range
- pump power at loads beyond monitoring range
- system hydraulic behavior
- pump power