Hawker—located in Ooltewah, Tenn.—is a manufacturer of industrial, lead-acid batteries. Hawker manufactures batteries for applications as diverse as telecommunications and aircraft, uninterruptible power supply systems and submarines. Industrial lift trucks of different sizes and capacities are also a major application. “The sulfuric acid we used to make the batteries was an extremely corrosive liquid,” says Kelly Hogan, plant manager. “The conventional metal pumps we previously used to handle it required frequent maintenance, resulting in downtime and lost production. Since we replaced them with thermoplastic cantilevered run-dry pumps (see Image 1), we have saved an average of $3,000 to $5,000 per month on maintenance and parts replacement. Not only is the solid polypropylene of which they are constructed completely inert to sulfuric acid, but their cantilevered design eliminates immersed bearings and allows run-dry operation for extended periods of time without damage.” Each application requires a battery with different characteristics. Pallet jacks and light lift trucks, for example, require a lower power output than those that make long runs and high lifts under harsh conditions or have attachments that require additional power. For applications with limited accessibility, Hawker’s batteries require watering just four times per year. Its valve-regulated, lead-acid batteries contain a gel electrolyte in a sealed chamber that never requires adding water.
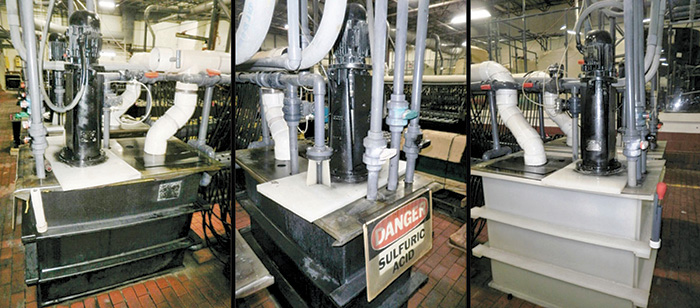