This alternative technology is ideal for petrochemical applications.
06/16/2016
In certain applications, alternating-current (AC) variable speed drives (VSDs) can offer several advantages over traditional methods of process control, including energy savings, reliability and process improvement. Petrochemical drive applications, however, often require the motor to be located long distances from the drive. In some cases, this distance can lead to premature motor failure and negate these advantages. Conventional 480-volt (V) pulse width modulated (PWM) AC drives switch 650V direct-current (DC) power to make a variable voltage, variable frequency AC output. The resulting output is a two-level waveform.
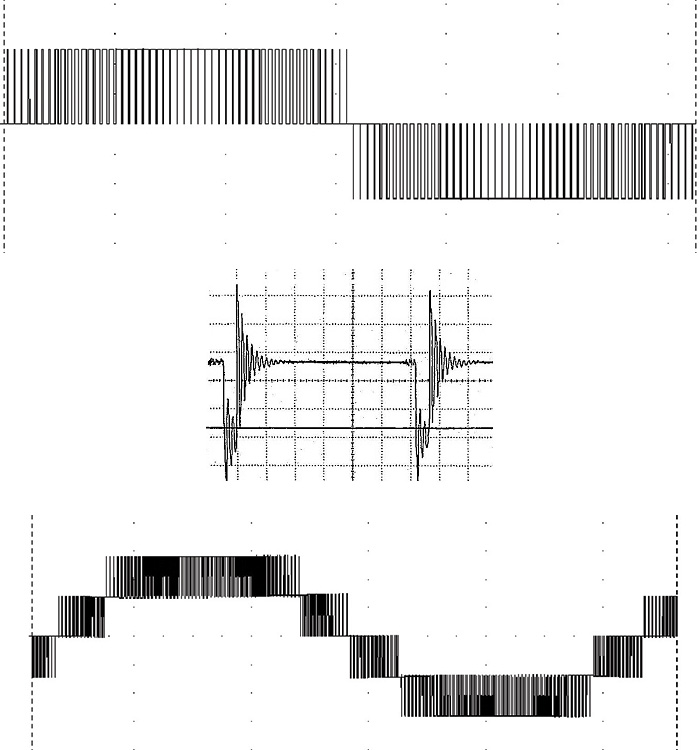