08/29/2014
In my July 2014 column, I demonstrated that three-phase voltage variation can significantly affect several alternating current (AC) motor characteristics. If that variation is large, it can also reduce motor life. Voltage unbalance can be an even bigger problem and is one of the major causes of premature motor failure. A relatively small unbalance of just 2 percent can reduce expected insulation life by half.
Calculating Voltage Unbalance
Unlike voltage variation, unbalanced voltage occurs when the three phases are not at the same voltage. An example of perfectly balanced phase voltage is L1/L2 = 460 V, L2/L3 = 460 V and L3/L1 = 460 V. The average voltage is 460 volts. An example of unbalanced phase voltage is L1/L2 = 462 V, L2/L3 = 468 V and L3/L1 = 450 V. Again, the average voltage is 460 V, but the unbalance is 2.2 percent. Voltage unbalance is calculated by the following equation: Percent unbalance = 100 x (maximum voltage deviation from average / average voltage) In the example above, the maximum voltage deviation from the average voltage is 10 V (460 minus 450). Motors from member companies of the National Electrical Manufacturers Association (NEMA) are designed to tolerate no more than 1 percent of voltage unbalance. Why does voltage unbalance shorten motor life? One percent of voltage unbalance can result in 6 to 10 percent of current unbalance. The phase with the lowest voltage exhibits the highest current, which increases the operating temperature of the winding serviced by that phase. It will also increase the overall operating temperature of the motor. Figure 1 shows the increase in operating temperature versus voltage unbalance. As shown, an unbalance of just 3 percent can increase operating temperature by almost 20 percent. At 5 percent unbalance, operating temperature will increase by 50 percent.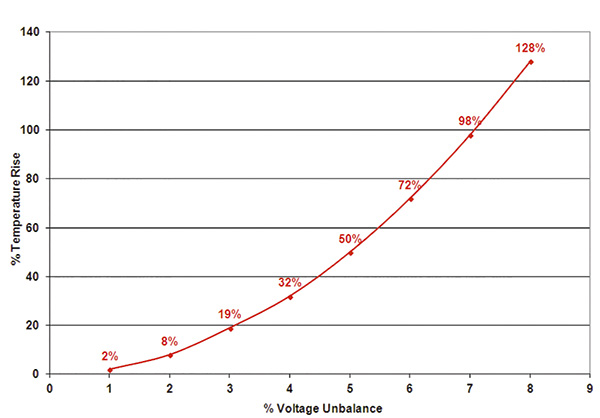
Temperature Rating & Insulation Class
Motor operating temperature is the sum of the ambient temperature surrounding the motor and the temperature rise due to the motor load. The temperature rise is usually measured using the resistance method. Each insulation class has a specific temperature rating. For example, Class F is rated at 155 C (311 F). The temperature rating is the maximum operating temperature allowed in order to meet an average insulation life of 20,000 hours. Of that rating, 10 C is reserved for the hot spot allowance. The resistance method measures the average temperature rise in the stator windings, but at some places—such as the stator slots—the temperature can be higher than the average measurement. The hot spot allowance is reserved to protect these areas. This reduces the actual operating temperature (ambient plus measured average) to 145 C. For every 10 degrees over 145 C, insulation life is reduced by half. For every 10 degrees below 145 C, insulation life doubles. Suppose a motor with Class F insulation operates at an ambient temperature of 40 C. The measured temperature rise at full load is 90 C. Therefore, the operating temperature is 130 C. The expected insulation life would be about 50,000 hours or about 2.5 times the life at 145 C. But at 3 percent phase voltage unbalance, the operating temperature increases by 19 percent (155 C) and insulation life is reduced by 50 percent. Image 1 shows the windings of a motor that failed because of high voltage unbalance. When a motor loses one phase (single phasing), the other two phases have to carry the entire load. As a result, two sets of phase windings are destroyed, and the one that lost power is unharmed.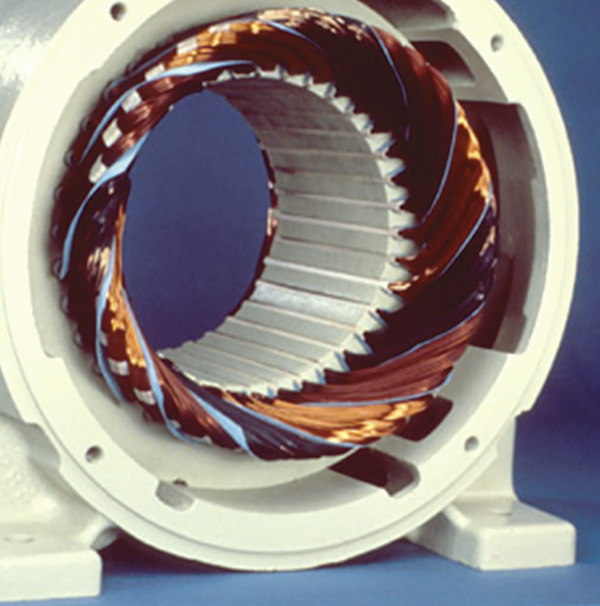