02/01/2016
Q. What is the estimated time between repairs for common wastewater pumps? A. The optimal performance or life of pumping equipment will be achieved when the equipment is correctly designed, sized and selected for a given application and the units are operated (and maintained) at the specified conditions. The design life can be different for varying services and equipment types. In any application, shareholders in the overall outcome will influence the type of equipment selected and the way it is applied and maintained. Main shareholders and influencers in the design, selection, application and maintenance of the equipment include the following:
- Project engineers: minimize capital expenditures
- Maintenance engineers: minimize repair hours
- Shareholders/owners/general manager: maximize dividends and/or share price
- Production personnel: maximize uptime hours
- Reliability engineers: maximize equipment reliability to avoid failures
- Accounting staff: maximize project net present value
- Mechanical unbalance of rotating parts
- Mechanical unbalance from abrasive fluids wear
- Pump and driver natural frequency and resonance
- Miscellaneous mechanical problems
- Hydraulic disturbances
- Hydraulic resonance in piping
- Poor structural rigidity
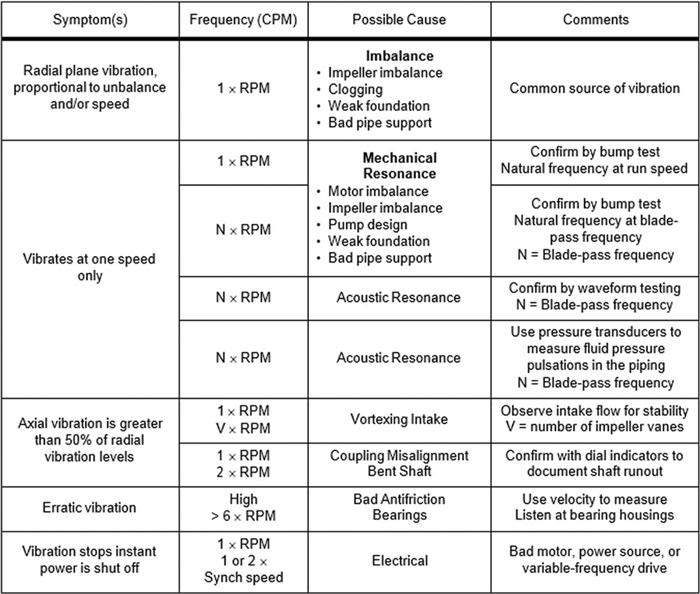
See other HI Pump FAQs articles here.