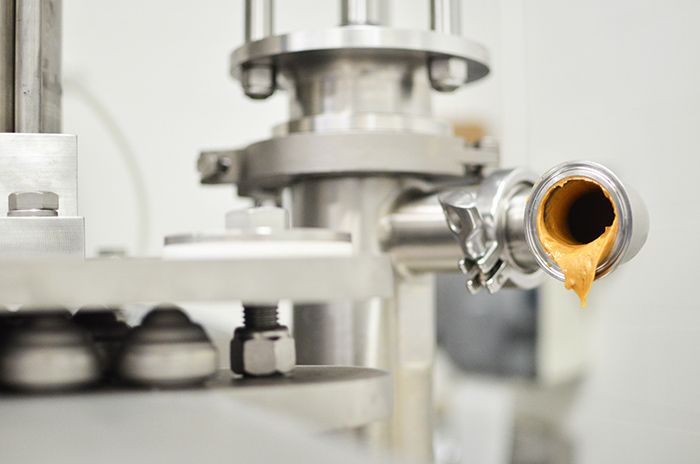
High viscosity fluids can have some interesting effects on systems, especially when centrifugal pumps are involved. Viscosity is a measure of the force that must be applied to the fluid in order to create flow—the higher the viscosity, the more resistance to flow. This can have some serious effects on the performance of pumps and systems. How do engineers account for this during system design? Review various calculation methods that can help estimate the system’s response with viscous flow. Note: If there is actual test data for the system using viscous fluid as the test fluid, these correction methods will not be necessary.
Pump Viscosity Corrections
The most accurate representation for the pump curve would be to use a pump curve generated by the manufacturer using the system fluid as the test fluid. However, this data is rarely available. So it is typically required to perform some type of adjustment to the provided pump data.
American National Standards Institute (ANSI) and the Hydraulic Institute (HI) have developed standards, detailed in ANSI/HI 9.6.7-2010, to adjust head/flow data just for this purpose. There are a few key limitations with applying this standard. It is noted in section 9.6.7.4.2 that the correction factors are highly impacted by impeller design, so this method should be limited to radial impeller pumps with specific speeds (Ns) of Ns < 60 (metric units), or Ns < 3000 (U.S. customary units). In addition, this method should only be used with Newtonian fluids.
Correcting the NPSH3 (sometimes referred to as the net positive suction head required) for the pump is a more difficult prospect as there is not a clear universal relationship between viscosity and NPSH3. The NPSH3 is the suction head at which the pump will sustain 3 percent head loss due to cavitation.
Several sources have indicated that NPSH3 is not affected by varying viscosity, as there are conflicting factors that both increase and decrease the NPSH3, so that the overall impact on NPSH3 is often balanced. ANSI does provide a correction factor based on theoretical thermodynamics. However, a simpler, more conservative approach would be to simply increase the required NPSH margin at the pump.
Pump manufacturers may have more specific recommendations for viscosity correction based off the geometry of the pump, which can have large effects on the correction factors. Failure to properly account for the effects of viscosity at the pump can result in undersizing the pump for the system, as well as decreased equipment life.
Modeling tools can help with performing sensitivity analyses and applying correction factors using standards such as this ANSI standard to efficiently apply these corrections to the design.
Minor Fittings & Losses
Minor fittings and losses can have a larger impact than expected for systems with viscous fluids, especially as flow enters the laminar regime occurring at Reynolds numbers less than 2,300. Though sources such as Crane Technical Paper 410 have traditionally treated loss factors such as K factors as being applicable across all flow regimes, several recent sources have shown that this is not necessarily the case. A technical paper “Resolving Operational Problems in Pumping Nonsettling Slurries,” (Daniel W. Wood and Trey Walters published at the International Pump Users Symposium), discusses a case where cavitation issues were experienced in the suction line for a system. Ultimately, the source of the issue was that the K factors used in the system design were not properly accounting for the increased loss under laminar conditions.
Choosing a loss model that can properly account for losses in the line when laminar flow is expected, especially in the suction line, is crucial for system performance. Methods such as the 3K loss method, equivalent lengths, or the adjusted turbulent K factor (ATKF) method are all recognized as more conservative methods than traditional K factors.
The 3K and equivalent length models contain experimental loss factors that can be of limited use if the components being modeled are not similar in geometry to those used to determine the loss factors. The ATKF method applies a correction factor to the turbulent K factor to approximate a laminar flow K factor value. All three methods have produced similar loss values when compared for equivalent components.
Depending on the tool used for calculations, common data for these loss methods can be stored to automate the calculation process for any of these methods, rather than calculating all minor losses by hand or neglecting these losses entirely. For viscous systems, these “minor” losses often can have a major impact on operations.
Variable Losses
Similar to pumps, variable loss components such as control valves will have adjusted operation due to high viscosity fluids. Control valve manufacturers typically provide test data based off water. Unlike with pumps, the valve flow coefficient (Cv) value can be calculated differently depending on the manufacturer, though the general Cv equation used is: Cv=Q√(SG⁄∆P).
There is no global standard for viscosity corrections. Most valve manufacturers will provide information to determine the proper viscosity correction factor for the valve, which is typically found in terms of the Reynolds number.
In general, if the Reynolds number is above 1000, this correction will be relatively small. However, when in doubt, it is always best to calculate what the correction factor will be and test the impact on the piping network as a whole.
If the viscosity correction factor is not applied during the design process, the control valve could be undersized, overly restricting flow to the process. In general, it is recognized that viscosity correction factors for valves can have a high level of uncertainty due to the high dependence on the geometry of the valve. Additional geometry correction factors can help with this issue, though this is something to be aware of during the valve selection process.
Overall, the higher the viscosity and the lower the Reynolds number is, the more severe the impact will be on the system.
All equipment in the system can be affected by viscous flow conditions, not just the pump curve.
Modeling tools can help automate this process and reduce the amount of time needed to take these effects into account for a system design.
Make sure to apply these methods for troubleshooting operational issues in existing systems, or for designing new systems with viscous fluids.