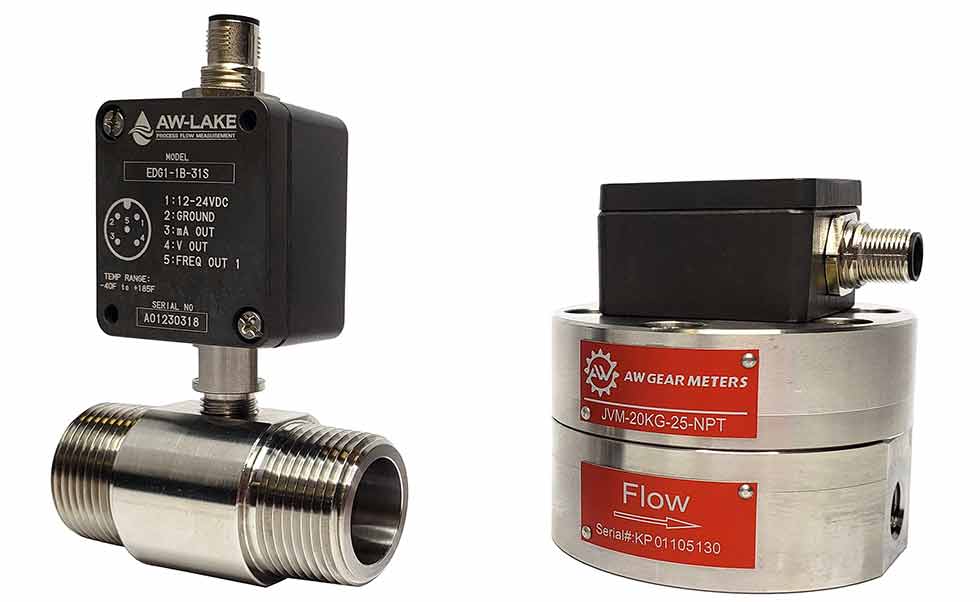
When choosing a flow meter for any application, some performance parameters are more critical than others to determining which meter will work best in an application. Three primary parameters include (in order): accuracy, linearity and repeatability.
These parameters are evaluated after the flow meter installation to determine its performance status and as part of a regular system maintenance schedule. As much as flow meter accuracy is the ultimate requirement, linearity and repeatability are important in determining its best possible performance within the application.
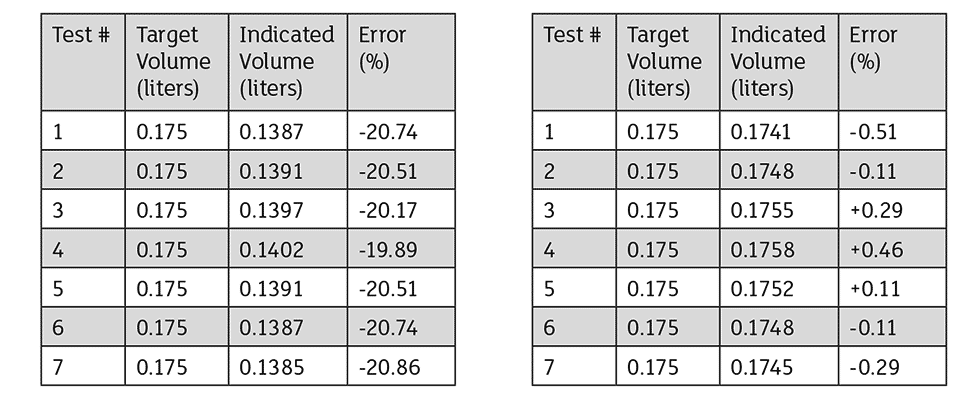
Troubleshooting Inaccurate Flow Readings
Inevitably, a flow meter may not give an accurate reading, either after initial installation or long-term use. Before spending time and money to return the unit for repair or call a technician for help, a bit of careful analysis may quickly solve a simple problem. Inaccurate readings can occur for many reasons. Scaling of the flow meter signal could be off, the measured fluid may not be ideal for the meter or may have changed from initial application, or long-term use may have caused some wear that affected the meter’s performance.
For most flow meters, the application of a scaling factor, almost like a language translator, is needed to convert a meaningless signal from the flow meter into a usable flow reading. Positive displacement and turbine flow meters output their signals as a pulse. Without a scaling factor, the user would not know how much volume each pulse represents. Other meter technologies, such as Coriolis and ultrasonic, use time as their base signal, which again, without a scaling factor would make no sense to a user.
The user has an important role and effect on the accuracy of any flow meter based on the scaling factor converting the raw signal into a meaningful flow value. Entering the wrong value can result in an inaccurate reading. However, that does not mean the meter is defective.
Solving a Flow Meter Problem
Let’s look at a real application of a meter outputting an inaccurate flow reading and how focusing on the repeatability of the meter helped solve the problem.
A positive displacement flow meter used to measure lotion dispensed in small, quick shots was not providing accurate flow output. The signal from the flow meter, derived from a pulse output sensor connected to a programmable logic controller (PLC) that monitored the amount dispensed, had an error indication limit set for +/-2.5% of target dispense volume.
In this new system installation, the end user entered the supplied scaling factor for the flow meter into the PLC and ran some tests to determine the accuracy of the system before starting the production run. Even as the user spent the time to ensure proper setting of system components, it consistently errored out right away.
After performing volume verification shots into a graduated cylinder, operators determined that the flow meter was not giving the correct flow indication. To figure out the problem, the user contacted the OEM. After asking the customer to conduct some basic troubleshooting, the OEM asked for copies of verification data to understand the inaccurate performance of the meter. The data shown in Image 1 was reported.
Taking a Second Look at Test Results
After reviewing the results, it was clear that the meter was not performing well and was far from its expected accuracy of +/-0.5%. The -20.4% error was way off specification. Additional testing generated the same results consistently. After carefully reviewing data, it became evident that although the meter’s reading was not accurate, the results were repeatable.
With the overall repeatability of +/-0.49%, the manufacturer felt comfortable that the flow meter would perform well in the application since the allowable error limit of the system was +/-2.5%. In analyzing the results, the user was asked to change their scaling factor by 20.4% and re-run the tests. The data shown in Image 2 is the new test results with the adjusted scaling factor.
Solving the Problem
The new results proved that with an adjustment in the scaling factor, the data from the meter was well within the required +/-2.5%. The meter was indeed accurate. Further analysis into the application found that the actual system flow rate was lower than initially specified, so the meter used was operating on the lower end of its range. Also, as the lotion under measurement was of wax consistency at room temperature, it was initially heated, lowering its viscosity to 11 centistokes (cSt) and causing greater than typical internal leakage past the gears.
While both of these factors caused the original scaling factor to be invalid in the application, there was nothing wrong with the flow meter. With the proper adjustment to the scaling factor, the meter ran accurately for years.
Simple Analysis Can Solve Flow Problems
As the user in the described situation would typically send back the flow meter due to the inaccurate results, careful analysis solved the problem. Users may find it difficult to understand why a flow meter would not work properly when using its supplied scaling factor. However, scaling factor is simply a means to translate the flow meter’s raw signals into usable data. Scaling includes accounting for any system variables that deviate from perfect conditions.
Determining the actual performance of the flow meter by focusing on its repeatability gives a more accurate picture of its performance. Unless conducting custom calibration to mimic actual application parameters, normal factory calibrations are completed under ideal conditions that may not always be possible at the customer site.
Scale Factor Changes to Achieve Highest Accuracy
Also, in Image 1, the system only ran at one fixed flow rate. Many applications run over a broad flow range. What may happen in these cases are changes in flow meter accuracy at varying rates and not always by the same amount. In such cases, it is a question of changes to the flow meter’s linearity over the flow range.
This also could be compensated for if the readout has a linearization function, meaning it can be programmed with different scaling factors across the flow range. To achieve the highest degree of accuracy and the best possible accuracy, run five to 10 repeatability tests at various flow rates to determine the optimum scaling factor.
The amount of variance in each repeatability test will indicate the best achievable accuracy if applying the correct scaling factor. For many applications, such scaling factor changes may be needed to get a high degree of accuracy. Therefore, the user should ensure that either the flow sensors or electronic readouts have an easy interface to make any required changes.
Today, devices are available with Bluetooth so flow meter performance and scaling changes are executable via phone apps, making it even easier to get a flow meter dialed in for an accurate flow reading.
An inaccurate flow reading is not necessarily an indication that a flow meter is defective. A flow meter’s accuracy often is affected by application parameters and user-programmed scaling factors. Focusing on a meter’s repeatability, and not its accuracy number, is an easy way to determine if a problem does indeed exist with the flow meter or if a simple adjustment to a scaling factor can get the sensor back to an accurate flow reading.
Read more Maintenance Minders articles here.