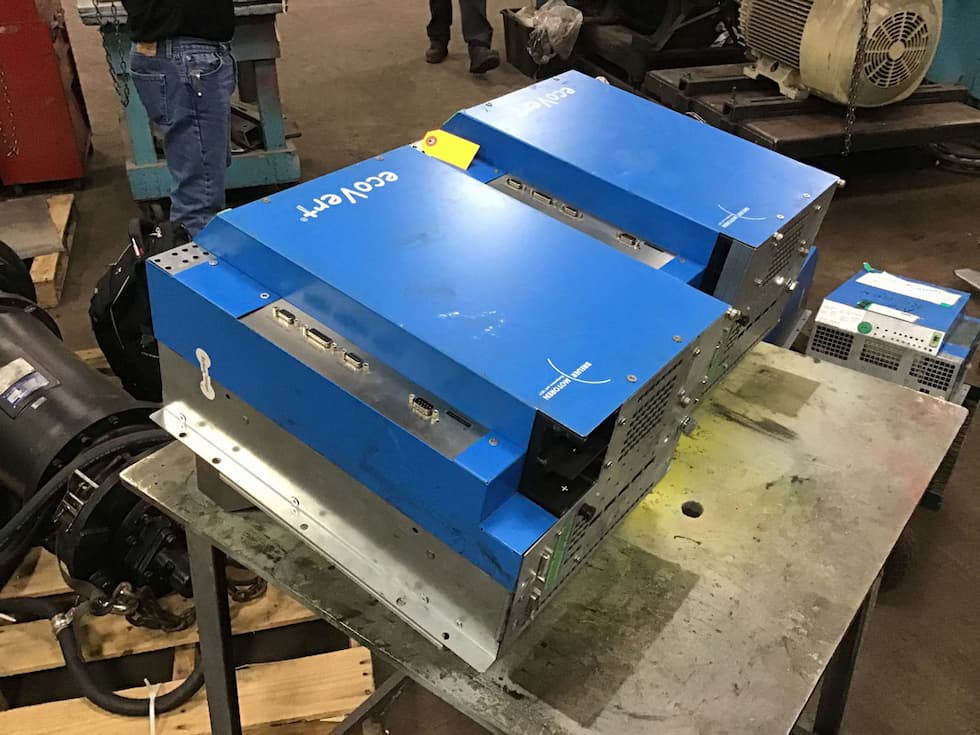
In the world of electric motors and industrial applications, businesses rely on their equipment to function properly and efficiently. Variable frequency drives (VFDs) are used in motor applications like pumps and forced draft fans to control fluid and airflow. They are relied on to keep production lines moving. Whether a system uses a VFD or a throttling control can influence efficiency. Either way, when production stops or slows due to a mechanical failure, the pressure is on to fix the problem and resume efficient production.
What Is a VFD?
A VFD is a type of motor control that drives an electric motor by varying the frequency and voltage of its power supply. The VFD also can control ramp-up and ramp-down of the motor during start or stop, respectively.
A VFD controls the speed of an alternating current (AC) motor by varying the frequency supplied to the motor. The first step in this process is to convert the AC supply voltage into direct current (DC) using a rectifier. DC power contains voltage ripples that are smoothed using filter capacitors. The drive then uses insulated gate bipolar transistors (IGBTs) to switch the DC bus on and off to produce the variable frequency.
Which Applications Use VFDs?
VFDs are used in everything from small appliances to large compressors. Since close to 25% of the world’s electrical energy is consumed by electric motors in industrial applications, the systems that use VFDs can be more efficient than those using throttling control of fluid flow. Because efficiency in applications that use VFDs see improvements, many businesses decide to upgrade from other systems to a VFD.
VFDs are commonly found in wastewater stations that transport sewage. Used to control the flow of sewage through the pumps, they help wastewater treatment plants successfully reach the required flow.
The Benefits of VFDs
VFDs provide improved and precise process control and regulation for motors used in industrial applications. The benefits of using VFDs in industrial applications are numerous, but the biggest benefit is energy savings. VFDs allow the operator to match the speed of the motor to the process requirement. Energy is saved when flow or head pressure is decreased. VFDs also allow for a bypass capability to protect equipment from damage caused by events like power outages and other emergencies. Additionally, VFDs give protection from overload currents and safe, precision-controlled motor acceleration.
Troubleshooting behind the scenes can be a rewarding task. When the steps outlined at right are followed, the problem is found with the VFD, production begins moving and the efficiency rate goes up. Oftentimes, this basic list of troubleshooting tips will resolve the issue. When troubleshooting does not provide the answers, reach out to a reliable repair partner.