In today’s oil and gas market, it is a constant challenge to keep a balance between operations, maintenance and compliance, while delivering production targets on budget and schedule. Oil and gas producers are under pressure to meet stringent environmental regulations. Increasingly, they are seeking solutions for treating produced water and other byproducts at the drill pad without incurring the expense of off-site disposal. Many technologies are used to measure flow rate in oil and gas applications. Differential pressure flow meters are among the most common, but they are sensitive to pressure changes. Coriolis flow meters can provide high accuracy, but they can be large and costly. Turbine flow meters are an especially good choice when ruggedness is needed. They can perform well under extreme conditions. The meters provide highly accurate and repeatable measurement of oils, water and some chemicals with a low cost of ownership.
How the Technology Works
Turbine flow meters excel at measuring clean, steady and medium-to-high speed flows of low-viscosity fluids, particularly those found in “pump-intensive” oil field environments. They maintain measurement accuracy and mechanical integrity in the corrosive and abrasive fluids commonly employed in oil and gas production and many other industries.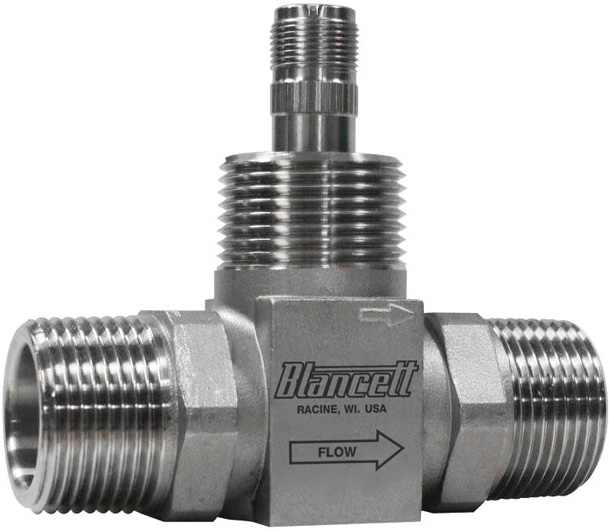
Typical Industry Applications
Turbine flow meters can measure everything from water in hydraulic fracturing operations to gases and liquids from wellheads. Typical oil and gas industry applications for them include: Water injection: Turbine meters are chosen for measuring process water injected into and recovered from wellheads to keep fracking formations pressurized or to help scrub remaining oil out of older wells. Test and production separators: Three-phase separators intended for well testing and production measurement, including those used for bitumen in oil sands operations, require precision instruments like a turbine meter paired with a field monitor to measure water-based fluids. Disposal wells: Produced water from wells goes into the pit or is stored in tanks on-site from where it is piped or trucked to the disposal well site, stored in a tank and injected underground for permanent storage using high-pressure pumps. Final disposal must be in accordance with environmental regulations. Turbine flow meters often measure produced water. Hydraulic fracturing: Oil field fracturing requires accurate and durable flow measurement instruments to monitor several processes during a treatment. Metering of used and reclaimed water is a primary application for turbine flow meters. They can be used to monitor the water as well as the chemicals used to treat the water. Natural gas pipelines: Turbine flow meters work in a variety of pipeline installations including those for metering stations, chemical injection and offloading to smaller pipelines for delivery or truck loading stations. Chemical injection: Petroleum producers require reliable and accurate mass dosing for downhole, pipeline, and oil and water treatment to minimize chemical usage and maximize effectiveness. Turbine flow meters are used to meter liquid and gas additives. Experience has shown that turbine flow meters are well suited to deal with chemicals and corrosive fluids, high pressure and particulate matter in oil and gas production. In addition, they can be supplied with digital readouts and used with heat trace. The biggest benefit of using an inferential technology such as turbine meters for frack and produced water is the initial cost of the unit.Benefits to Operating Companies
- Some of the other advantages provided by turbine flow meters include that the meters are: simple to install, operate and maintain
- in service worldwide as a reliable, cost effective method for obtaining accurate flow data
- designed to maximize throughput and minimize pressure drop
- able to maintain high flow rates over an extended flow range and offer pulse output that is linear to the flow rate
- able to minimize fiscal measurement uncertainty by delivering high-frequency pulse resolution to account for minute increments of the flow rate