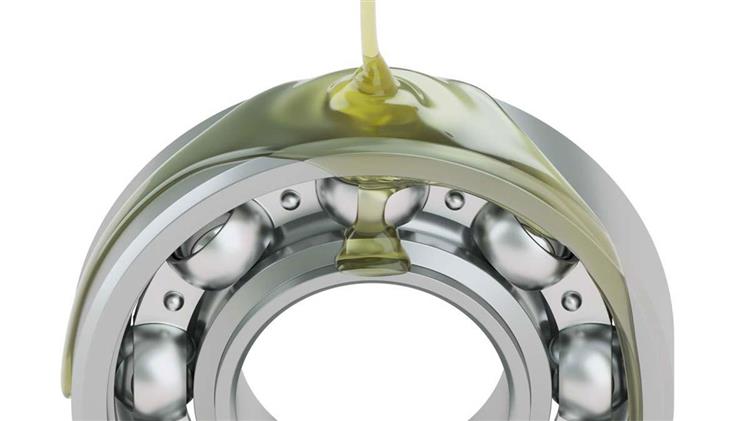
Bearings are an essential part of rotating equipment. The final load, whether it be axial or radial, is finally grounded with the help of bearings. Bearings may be considered analogous to ground connection in the case of electrical circuit. Bearings can be classified depending on various criteria such as the design, loading conditions, arrangements, type of lubrication and so on. Proper selection of the bearing is important, but not as important as proper installation. Following the correct assembly procedure while installing the bearings is paramount to achieving the intended service life of the bearing.
Understanding duplex bearing arrangements during selection as well as assembly is important. Incorrect installation and a failure to understand what the application is could result in problems while running the equipment, such as skidding or overheating.
This article aims to present the underlying concepts and what actually happens when the bearings are preloaded.
Duplex bearings are a set of two bearings that attain greater radial and axial rigidity when arranged on a shaft with the inner and outer rings clamped together with preload. Single-row angular contact ball bearings and tapered roller bearings are generally preloaded axially by mounting them against a second bearing of the same type and size in a back-to-back (load lines diverge) or face-to-face (load lines converge) arrangement.
The bearings are matched pair bearings and the faces of the bearings are precisely machined and grounded to provide preload when installed. As mentioned above, these different types call for the different faces of the bearings to come in contact, causing preload. These arrangements are typically used in connection with angular contact ball bearings and tapered roller bearings. The preloading is achieved either by closing the gap between outer-race faces or inner-race faces, depending on the type of arrangement.
Types of Arrangements
The descriptions for the arrangements include:
- Back-to-back arrangement: Also known as an O arrangement, this is known to give maximum stability and rigidity. In this arrangement, inner ring faces are designed to touch each other to achieve preload, and radial and axial loads in both directions can be taken (see Image 2).
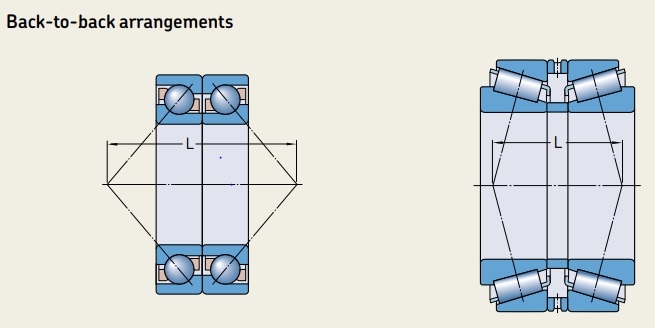
The important thing is to understand why this arrangement gives more rigidity and stability. Looking closely, what actually happens is that outer races are radially and axially restricted completely. So now, the internal clearance of the bearing will be closed when the inner races of the two bearings touch. That is called preloading. When preloading, the inner races of the bearings are being pushed toward one another.
The inner races obviously have a rolling element with a cage above them, and pushing inner races will in turn push these rolling elements in the direction of the force. Now the rolling elements are restricted by the outer races. Hence, the outer race will exert the reaction to the applied load, which will be toward the shaft centerline. Now, as per the contact angle, the reactions from both the bearings will be diverging, with distance L between the two reactions.
Because of this constant reaction force from an outside stationary body (ground) acting on the shaft and with L being more than the width of the bearings, the shaft will be tightly held in the position covering length L at the bearing location. This tightness is realized in terms of higher rigidity and the stability of the shaft. That is why back-to-back arrangements have better resistance to moments in the shaft.
Face-to-face arrangement: Also known as an X arrangement, this is known to tolerate misalignments and cannot support moment loads as effectively as back-to-back arrangements. If misalignment cannot be avoided between the bearing positions, face-to-face bearing arrangements are recommended (see Image 3).
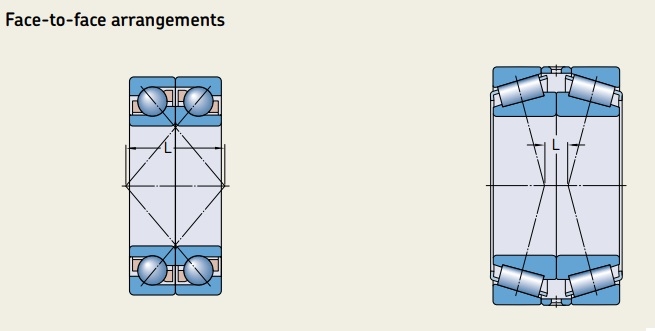
Here in this arrangement, one can see the reaction load lines are converging inside reducing the distance L, as compared with back-to-back arrangements. However, the noteworthy point here is that the inner races are touching each other at the face and the gap is initially present at the outer races. Hence, the preload is achieved by closing the gap between the outer races. In the same way as described for back-to-back arrangements, one can imagine that while pushing the outer races closer, it will move the rolling elements with the cage along.
Since the movement of the inner races is completely confined, there will be a reaction force arising inside out, i.e., the reaction will be given by the inner races against the applied force. This is due to the load lines will come closer to reducing the length L. The reaction force coming from the shaft (inner races) reduces the stiffness of the arrangement and then it can tolerate some misalignments.
After understanding these arrangements, it makes clear the advantages that are normally outlined in the manufacturer’s catalogues.
The primary benefits resulting from preload include, but are not limited to:
- enhanced stiffness
- reduced noise levels
- improved shaft guidance
- compensation for wear and settling
- extended bearing service life