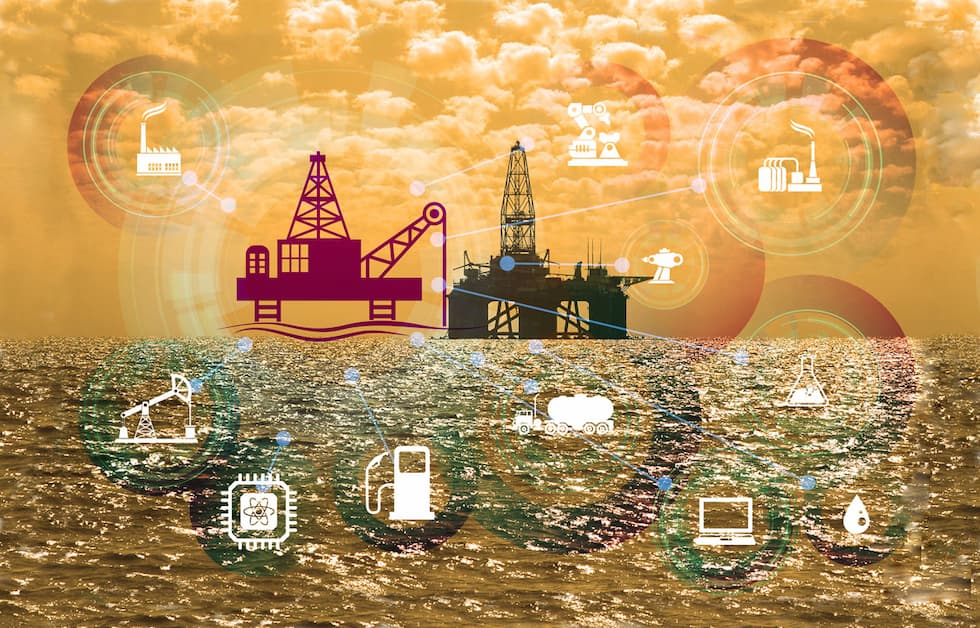
The use of digital twin technology within the oil and gas industry has yet to be fully embraced. However, it presents many advantages, and its use can improve regular maintenance tasks, not only driving down costs but also improving output.
What Is a Digital Twin?
In short, the technology provides an accurate digital model of a physical process or product. When applied to assets within the oil and gas industry, users can map out the entire life cycle of equipment, running different scenarios to simulate projected maintenance tasks and longevity. However, the quality of the returned results will only be as good as the data that the system is provided with.
The challenges of this within oil and gas is that the industry is subjected to many imbalances and dynamic changes. Examples of this include:
- imbalances between supply and demand
- geopolitical events
- the adoption of green energy sources
- other market forces—most notably the COVID-19 pandemic
The latter has brought about a chaotic environment that has highlighted the need for risk management and mitigation in order to become truly sustainable. Only by responding to real-time events can an operation best survive during such turmoil.
How Can Digital Twin Tech Help?
With current data, a digital twin can accurately determine maintenance needs, even in a volatile climate. It is important to note that in the industry today, around 63% of all assets are more than halfway through their projected life cycle. However, in a situation such as the current pandemic, the demand for oil reduced dramatically. This led to vast overproduction, something that a digital twin projection must take into account. Without real-time data such as this, a digital twin cannot return the much-needed accurate results.
The challenge for companies is to get a hold of high-quality, verified and referenced data with which to input the digital twin technology. At present, an industry-wide, broad-scope approach means clunky integration that is slow to navigate. Indeed, by the time an operation has collated the quality data needed for an accurate digital twin return, further dynamic change has already occurred. This means the returned projected outcome is already behind the curve—even obsolete—should another dramatic industry shift occur.
Gaining Accurate Real-Time Data
Gaining the full advantage of digital twin technology requires continuous updating of the data and models provided. The volume of data in the industry is enormous and all needs to be verified and organized before being entered into a digital twin. It also needs to be accurate. Manual data, such as paper forms and manual entry, has an error percentage that is too high to accurately portray current demand. The need for automated data collection is paramount. Such channels being used to collect and collate this include:
- drones
- video capture
- satellites
- fixed wing aircraft
- supervisory control and data acquisition (SCADA) systems
- internet of things (IoT) sensors
This is in addition to oilfield data, including well logs and reservoir performance. Integrating all such data with operational technology leads to quantifiable and actionable results. Overriding technology that can verify and produce such data is yet to become widespread.
The capabilities of a data collation tool can be specifically applied for digital twin technology use within the oil and gas industry. This type of model is adaptable, allowing for change and modification of both existing and future systems and processes. High-quality, collated data brings about digital mapping according to the core purpose of the company and project, as well as giving the capabilities necessary to respond to expected and unexpected events.
The input of such quality, relevant and current data allows digital twin simulation not only for the here and now, but also to run virtually limitless scenarios for asset simulation whatever the future situation.
Such predictive maintenance has massive implications for the running of oil and gas operations. In fact, embracing digital twin technology is set to become a key component for successful industry performance.