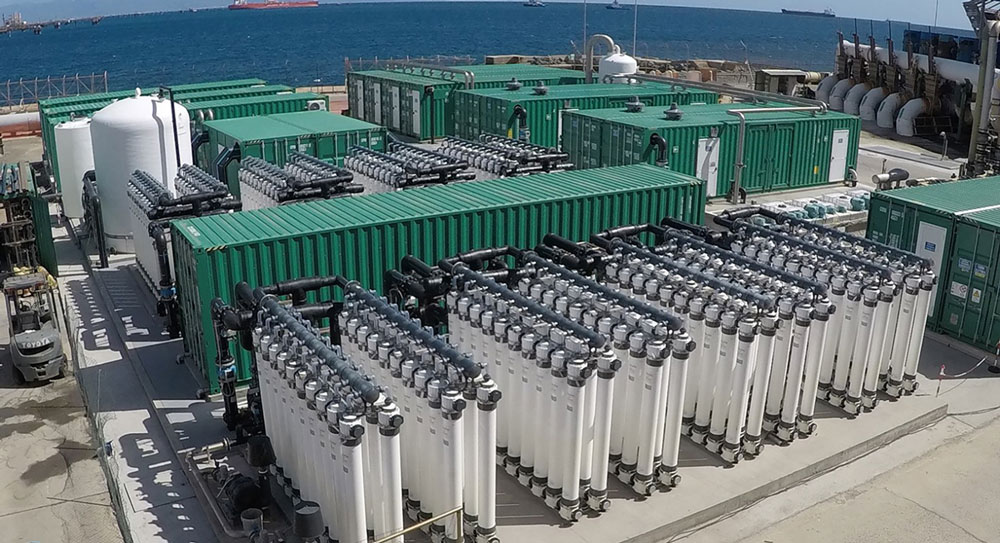
As the global population grows, the demand for water grows too, putting pressure on resources for drinking water, human sanitation and food security. At the same time, the world is facing climate changes that make the availability of water less predictable. Extreme weather events deplete water resources in both water-stressed regions and regions that have not yet been affected by drought or flooding.
To meet the water demand, the world is uniting around United Nations Sustainable Development Goal 6 to secure water and sanitation for all by 2030. The quest for sustainable water supplies is active, and desalination by reverse osmosis (RO) has quickly become a preferred method due to its high efficiency and the extensive availability of seawater compared to other water resources. However, desalination comes at the price of energy. Today, the water sector alone is responsible for about 4% of global electricity consumption, so preserving energy in the desalination process is important. The choice of equipment and components defines the energy efficiency of the RO installation, from initial design to later upgrades and retrofits.
Increased efficiency can be achieved through small investments with a short payback time. After adding it all up, there are millions of dollars and tons of carbon dioxide (CO2) to be saved every year in the desalination industry.
The Pump Matters
RO is a highly energy-intensive process, as the system operates under high pressure to drive the seawater across membranes and remove the minerals. In fact, the pumps consume about 50% to 60% of the total energy used by a typical RO plant, and the choice of pump technology will determine the potential for energy savings.
For many years, centrifugal pumps were considered the best choice for RO. But increasingly, system builders turn to water-lubricated axial piston pumps (AP) coupled in trains to provide the most efficient and flexible solution to meet the changing water demand.
A manufacturer compared the energy efficiency of centrifugal and axial piston pumps across different pump configurations and flow rates. The study revealed energy savings of up to 16% with a high-pressure pump for RO compared to the centrifugal setup across a variety of parameters.
Energy savings like these are documented in test studies and daily operations of plants across the world, and when it comes to the total cost of ownership (TCO), high-pressure pumps represent a competitive choice with operational flexibility, high uptime and reliability. By fast-tracking the adoption of innovative and proven solutions for sustainable desalination, the industry can accelerate low-carbon development and stay on course for climate-neutral water production.
Reducing Energy Consumption
An infrastructure and renewable energy solutions provider opted for high-pressure RO pumps when tendering a new ultrapure seawater RO plant for a power company on the Italian island of Sardinia. The company had three main requirements for the new desalination plant: provide 12,000 cubic meters (m3) ultrapure water per day, cut the electricity consumption and carbon footprint, and complete the job quickly without any infrastructural modifications.
In six months, the new plant was up and running with four containerized RO units. One year into operation, the energy consumption of the desalination processes has been brought down by 88% compared to the old system.
Hybrid Pump Solutions for Large RO Plants
While parallel-coupled axial piston pumps are competitive when it comes to TCO in small and medium-sized RO plants, large, urban water systems can benefit from hybrid solutions that combine high-pressure centrifugal and axial piston pumps to meet the demand for high-efficiency and sustainable desalination solutions. The use of this kind of hybrid solution is an attractive option for retrofits, optimization or upgrades of existing, large-capacity RO systems and promises substantial efficiency improvements.
The RO system requires constant water flow from the centrifugal pump, especially in systems where pressure fluctuations occur due to changes in salinity or water temperature. These pressure fluctuations cause the output flow of the centrifugal pump to shift and control valves or large variable frequency drives (VFDs) are installed to compensate for the shift.
The hybrid solution combining the centrifugal pump with the axial piston pump requires a small VFD to control the flow and no control valve is needed. This makes it a competitive solution in terms of capital expenditure (capex) as well as operating expense (opex) for new systems and retrofits.
Isobaric Energy Recovery for RO Plants of All Sizes
While renewables like solar and wind power are finding their way into desalination plants, there is still a long way to go before renewable supplies are sufficient. Hence, achieving optimum energy efficiency still plays a crucial role in the quest for sustainable RO solutions.
The energy used for pressurizing the seawater to drive it through the RO membranes is rendered useless at the end of the process, and energy recovery devices are used to capture the energy and return it to the feed.
Isobaric energy recovery that transfers the hydraulic energy from the brine stream directly back into the feed stream is known to be an efficient technology, providing efficiencies up to 97% at all flow rates.