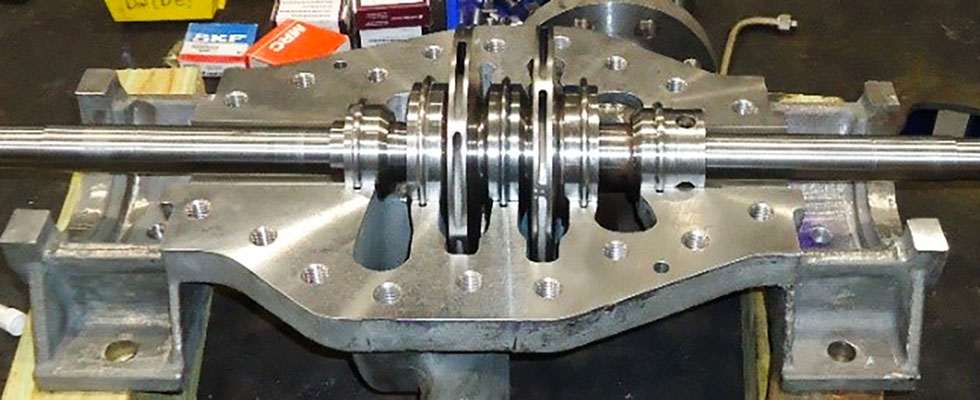
A rotating equipment servicing company in Port Arthur, Texas, recently worked with a refining company that had a pump that was originally manufactured during the 1950s. All casting was predominantly made of cast iron, a typical construction material during that period. The plant is fitted with two pumps nested inside the unit. Replacement parts for this model pump were obsolete, and a solution was needed quickly.
Purchasing a new pump presented two major challenges.
- Delivery time for a new pump is long—even for traditional reverse engineering processes.
- A new current model pump would not fit the existing plant footprint and would require extensive modification.
The final solution was to design a drop-in replacement pump. A drop-in replacement is a pump that will meet all the touch points (feet, flanges and drive coupling), thereby protecting the existing capital investment while fortifying the pump with the latest design standards. Using reverse engineering, incorporating mechanical and metallurgical upgrades while leveraging rapid cast technology, provided the ability for the pump to be delivered in nine weeks.
Full Restoration With Upgrades
Through the years, the pump had experienced extreme corrosion and wear. The overall materials were analyzed. The user had upgraded the impellers to duplex stainless steel during prior repairs. After reviewing American Petroleum Institute (API)-610 material specifications, all new material upgrades were recommended to optimize reliability. The following parts were recommended to be upgraded:
- pump case
- shaft
- wear rings (stationary and rotating)
Engineering Modification & Upgrades
Case
The wear (corrosion and erosion) observed on the casing reduced the thickness below the minimum wall to maintain pressure containment. The case was reverse engineered using the portable coordinate measuring machine to collect all critical data. The resulting 3D model was evaluated through geometric inspection and non-destructive testing (NDT) for hydraulic fit and mechanical integrity. This information was rationalized through design standards against the proper maximum allowable working pressure (MAWP). Ultimately, the casting was beyond repair, and it was recommended to not only replace the casing but to consider upgrading the materials of construction. The recommended new casing was manufactured in duplex stainless steel. To produce the new part with the proper fit, form and function, the 3D model is then adjusted to the original design requirements established during the reverse engineering process. This process is repeated for all parts that are required to complete the pump. It is important to reference current design standards throughout the process to make sure all potential reliability upgrades are considered and integrated into the drop-in replacement. For example, the seal chamber for this casing was upgraded to be compliant with API 682.
The individual pump parts are then separated into single-cast components, like the casing cover and bottom. The 3D models are adjusted for the required foundry casting allowance, and machining stock is added to the part model. This 3D model will be used to manufacture the part.
The next step for the 3D model is the casting simulation design. The solidification software can analyze the geometry to be cast along with the selected alloy and validate that the part will be of the highest quality. The objective is to have a solid casting with any shrinkage isolated inside the riser of the casting. The simulation can be iterated many times with various foundry rigging until the optimum design is developed. The output of the simulation not only yields a quality part, but also verifies the pour temperature, pour time, total melt weight for the mold and the duration until solidification. The yellow tubes on top of the 3D model for the bottom half shown on the simulation are the casting risers. The dark yellow in the middle of the riser shown on the right is the shrinkage isolated in the riser (note that no dark yellow appears in the casting itself).
The 3D model is now ready for the additive manufacturing (AM) process. The AM process eliminates the need for pattern tooling. With the randomized control trials (RCT), users can directly print the sand cast negative necessary to create a mold package used to cast the part. It also improves the casting quality by eliminating parting line, pattern draft and minimizing casting shifts. Employing digital control through the design and AM process allows a foundry to approach investment cast tolerances with the sand cast process.
Shaft
The shaft was upgraded to a stepped design. The material of construction was upgraded to duplex stainless steel. The seal area of the shaft was designed to accommodate the new API 682 compliant mechanical seal.
Wear rings and sleeves
The stationary and rotating wear parts were upgraded beyond the duplex standard to a super alloy known as Nitronic. This new material increases erosion resistance and extends the wear parts’ life span, thereby maintaining the running clearance for a longer runtime. The higher efficiencies over a more extended period will further reduce the life cycle cost of the pump.
Assembly
The pump case was machined and line-bored on the computer numerical control (CNC) bridge mill. Again, leveraging digital controls improves accuracy and reduces the process cycle time for machining.
Once the engineering review was completed and all design upgrades were incorporated, the parts were manufactured. A full as-built dimensional report was compiled along with all testing and material certification to produce a pump data book. The end user elected not to performance-test the pump in the test field, electing an in-situ performance test.
The pumps operating in the plants today were designed and manufactured several years, or even decades, ago by many OEMs that do not exist today or have designs that have become obsolete as drawings and patterns have been lost or destroyed. Proper reverse engineering (not copy-paste), state-of-the-art digital manufacturing processes and sound pump design standard can produce a drop-in replacement quickly and cost-effectively.