Clean water is one of the most essential requirements for human health, environmental sustainability and economic development. Due to population growth, urbanization and climate change, this vital resource has become more scarce than ever in many communities around the world. In order to meet the increasing demand, there is a growing need for societies to shift toward a more circular economy, but it comes at a cost. Instead of automatically discharging wastewater, many experts believe it needs to be captured, treated and distributed back to the consumer. Water reuse and wastewater treatment are intrinsically energy intensive, due to the need to move large volumes of water using pumps and electric motors, and then treating the water to meet stringent regulatory requirements. In conventional wastewater treatment plants (WWTPs) aeration is one of the biggest energy consumers for treating wastewater. Other significant energy consumers include filtration and disinfection processes depending on application. To cope with increasing energy consumption and to reduce the carbon footprint in water industries, novel technologies need to be implemented. Innovative technologies in water reuse facilities often come with drawbacks like increased complexity and reliance on instrumentation. These challenges in energy management are not unique to the water industry. They are also of critical concern in other industries including the chemical, food and beverage, metals and mining, pharmaceutical, and oil and gas.
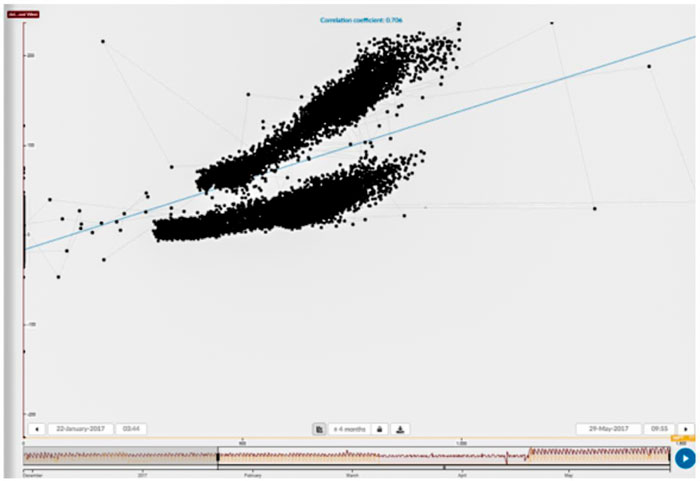
Energy Management 4.0
Global interest in Industry 4.0 has accelerated digital transformation in the process manufacturing industry, including those that are water-related. Many companies have engaged in technology pilots to explore options for reducing costs, to increase overall equipment effectiveness (OEE) and to help conform to enforced regulations. Anaerobic membrane bioreactors (AnMBR) are used in WWTPs to separate and treat sludge from wastewater, generating biogas as a byproduct. This technology can drastically reduce the energy consumption in large plants by generating renewable energy on-site. Microbial electrical systems can be used to generate electricity while treating wastewater with microbial fuel cells (MFC), for instance, but this is still in its early stages of development. Aeration is a key consumer in wastewater facilities, and a lot of research has been conducted in an effort to optimize these processes. To give some examples, membrane aerated biofilm reactors are an emerging technology in which oxygen is transferred much more efficiently. Optimizing the configuration and hydrodynamics in large bioreactors can provide better mixing. Better mixing consequently leads to less energy consumption for aeration and can even result in less production of strong greenhouse gases like nitrous oxides and methane.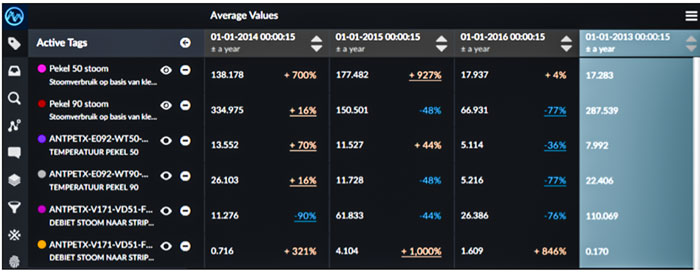
Practical Use Cases
Before starting any energy management project, it is crucial to define the problem and identify the high energy consumers. Using descriptive analytics, one can benchmark optimal operating conditions. Such benchmarks can be used to assess cost-saving opportunities and set priorities for optimization projects. Optimal operating conditions can be used to configure monitors, using discovery analytics. Leaks can be detected if levels in tanks decrease abnormally fast. Alerts can be received when sensors need to be replaced or calibrated. When flow control valves start to wear out or get plugged, this information can be captured within the data. Fouled membranes cause increased hydraulic head losses. This change of behavior is expressed in time-series data and can be identified by the appearance of different operating windows in scatter plots. These anomalies can be detected and used as a premise to prompt people in the field to take action, as was seen at PWN, a water company in the Netherlands.A Water Company Case Study
PWN used time-series data to calculate hydraulic head to analyze and monitor the performance of their water network. It became clear that the hydraulic head losses were increased after construction works (see Image 1). This descriptive analysis enabled the engineers to distinguish between the two operating zones. A similar approach can be used to optimize pumps by comparing the actual performance curve to the manufacturer’s performance curves, providing insights to the energy efficiency of the pumps. The installed system can be monitored live and used to better predict maintenance needs. Covestro, a chemical company, initiated three major energy savings projects for their polyether plant in Antwerp as part of the energy savings goals and ISO 50001 directives. Self-service analytics solutions were implemented for online detection, logging and explaining unexpected energy consumption and for comparing the results with the reference year 2013. The latter is illustrated in Image 2, where the averages of steam consumptions and production rates for four consecutive years are compared.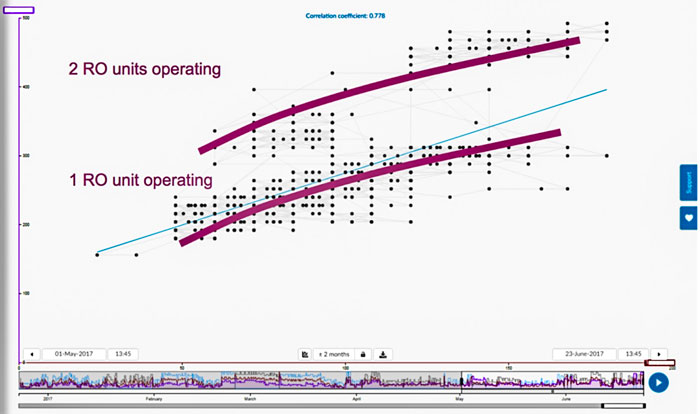