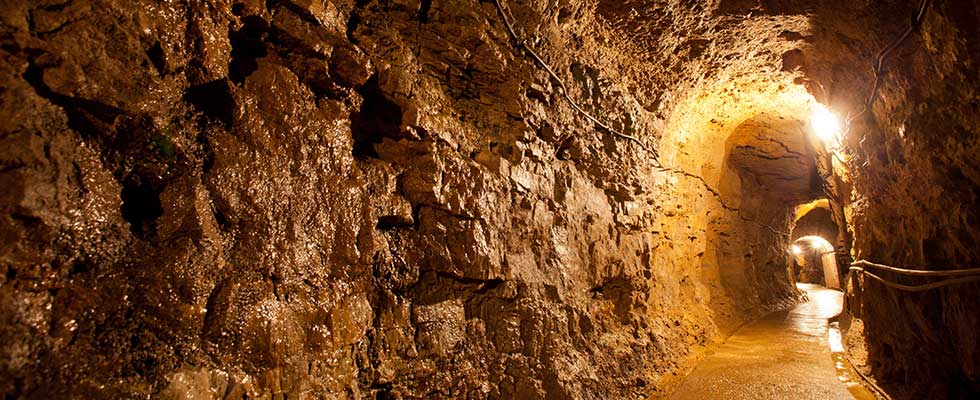
Industrial mining is a gritty business, and the pumps used to dewater sites and move slurries bear the brunt of the wear. Slurry pumps with high-chrome iron wear parts are purpose-built to extend the life of integral components even while working with process fluids that would quickly ruin equipment made from other materials.
In the mining and mineral production industry, moving slurries is the name of the game. Slurry, the thick, viscous fluid containing solids in suspension, is often difficult to move with traditional chemical or water pumps. So high-head slurry pumps are recruited to perform the heavy lifting.
Slurries are regularly used in industrial applications because they provide an easier way to move large volumes of pulverized solids. Any site involving deep digs—mining, oil and gas drilling, power generation and more—needs an efficient method to move extracted earth. Introducing water allows solids to be pumped away from the site using a slurry pump. Compared to mechanically moving materials using transport vehicles, pumps are faster and cheaper.
Submersible slurry pumps are widely found throughout the mining industry. A high flow rate, slow speeds and high slurry concentrations threaten pump components with severe wear and degradation. Contributing to the wear of parts are the high viscosity and abrasiveness of the slurry itself. This means submersible slurry pumps can have a short operational life, often lasting as little as a month or less.if the wrong pump is used.
Constant pump disassembly, repair and installation is expensive not only because of component costs, but because of the high costs of downtime and lost potential business.
Wear and Tear
To better understand the demands an industrial dig places on slurry pumps, picture a mine. It could be deep down in a cave. Maybe it is rainy season, so there is a lot of extra water and sandthat needs to be removed. They are excavating and moving tons of material. There is this mix of stones, water and dirt and mud, and as they are pumping everything through, these solid, abrasive materials are introduced into the pump.
There are harsh and degrading conditions found in industrial mining applications, where un-hardened metal components wear away like a soft wood to sandpaper. Whenever the impeller is spinning in sandy or gravel-laden water, the pumps wear out quickly.
Slurry pumps are widely found in places where things such as mineral and coal runoff are mined—which means an even higher concentration of abrasive particles are found in the slurry. It is not just the materials in the slurry but the entire pumping process that leads to wear. The slurry-pumping process can be compared to an upside down blender.
The volute is like the pitcher, and the impeller is like the blades. When it spins, there is a force, which creates pressure and forces the slurry out. There is the force of the impeller and this gritty water with particles rubbing up against each other, which creates a large amount of heat and pressure.
It is a perfect storm of constant abrasion, high pressure and heat that causes pump components to quickly degrade.
With typical materials, the parts wear out like they are being sanded. It literally wastes away the components. First there are holes, then it basically erodes itself to nothing. When things start to degrade, users start noticing hydraulic losses and leaks. It can be like sucking water through a straw with holes in it.
Most commonly, the parts to experience the most abrasion from slurries are the impeller, wear plate, shaft sleeves, mechanical seal faces, lip seals and the volute.
Also, running the pumps closest to BEP is critical since higher flow rates create more potential for wear on the pump. Ideally, the pump should be run at it’s best efficiency point while also keeping the flow at a rate high enough that material cannot settle at the bottom of the pipeline.
In the real world, even when a mine employs these best practices, pumps continue to wear down. It is the gritty reality of industrial mining.
Chrome Casting
In the realm of mining wastewater pumps, one solution to extend pump life is high-chrome iron components. The high-chrome casting process creates durable surfaces that are less prone to wear from temperature, pressure and abrasion.
Chrome casting can go beyond just surface durability. High-chrome iron cast parts can offer the perfect blend of durability and rigidity. Chrome casting can be advantageous because it achieves a level of strength that is maintained over time.
High-chromium alloys get their hardness from the presence of chromium carbides. Hard and corrosion resistant, chromium carbides are a refractory compound, and they retain their strength at immense temperatures and pressures.
Depending on the alloy’s specific composition, the presence of chromium carbides can increase the hardness of a pump part up to 1,800HV (Vickers Hardness) using the Vickers hardness test.
The process involves a specific heat treatment that produces hardness. The high-chrome alloy’s texture also offers extra wear resistance.
When considering upgrading pump components to those of the high-chrome cast variety, it is important to work with a supplier who can tailor solutions to user needs. The mining industry brings with it inherently expensive operations that are already prone to demanding oversight and regulations. The last thing an operator needs is additional shutdowns and stoppages due to premature wear and tear of low-quality components.