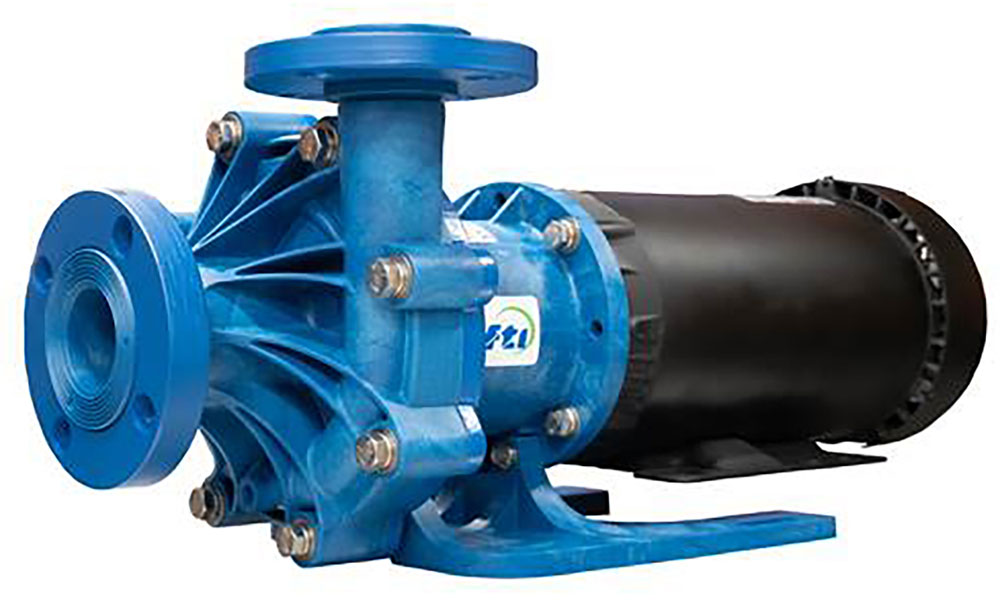
When considering flow rates of less than 300 gallons per minute (gpm), the centrifugal pump generally has design efficiencies ranging from around 50% to 70%. When combined with an electric motor where efficiencies of 80% to 90% and greater are common, and when applied to a system within reasonable proximity to the pump’s design point, it is an efficient machine for moving liquids from one place to another.
The air-operated double diaphragm (AODD) pump, on the other hand, is by comparison less efficient. The U.S. Department of Energy (DOE) estimates that the overall efficiency of a typical compressed air system can be as low as 10% to 15% and that to operate a 1-horsepower (hp) air motor at 100 pounds per square inch gauge (psig), approximately 7 to 8 electrical horsepower must be supplied to the compressor.1
While these two pump designs have widely varying efficiencies, both are ubiquitous among pump users and pump applications within this flow rate range. This is due to the versatility of the AODD pump. Consider these following points of pump application.
Self-priming
Ordinary centrifugal pumps are not self-priming; however, many self-priming centrifugal pumps are available in the marketplace today. These combine the attributes of a liquid ring vacuum pump and centrifugal pump into one and, as such, are special designs and must be filled with liquid prior to starting. AODD pumps are self-priming out of the box—it does not require liquid prior to starting. The AODD design is such that a vacuum is formed of usually 10 to 20 feet of water even when dry, allowing atmospheric pressure to push liquid into the pump suction.
Operating range
AODD pumps have a variable operating range over their curves. By varying the air pressure to the pump with a regulator or valve, the head curve can be selected for a given application, which can be altered for changing conditions or processes. The centrifugal pump requires a means for changing the motor speed in order to vary the head. Head can also be changed in discrete steps with impeller diameter.
Operating at shutoff
Operating a centrifugal pump at shutoff (shut valve, dead head and zero flow are synonymous) is damaging to the pump and can be dangerous due to the heat buildup within the fluid inside the pump. The pump is consuming power even though no flow is occurring, and that power is transferred to the fluid as heat from mixing and friction. Avoiding that condition involves the use of pressure relief valves, bypass piping or other monitors or sensors.
AODD pumps can run at shutoff at any pressure for an indefinite period of time without damage and without using energy. This attribute makes the AODD pump well suited for applications such as filter presses.
Running dry
Running a centrifugal pump without liquid can be damaging to most pump designs, including those with packed boxes and mechanical seals. Any close clearance bushings or wear rings are also subject to damage unless made from materials that are designed to run dry. Under most circumstances, running an AODD pump dry is not a problem. There are no close clearances to seize and all “wetted” seals are static. It is even possible to pump entrained powders with AODD pumps. The exception: It is not advisable to run dry with polytetrafluoroethylene (PTFE) diaphragms for extended periods of time.
Variety of fluids
In general, AODD pumps can be applied to a wider variety of fluids than centrifugal pumps. For inviscid, clean fluids, centrifugal pumps rule the day, but AODD pumps work well with viscous fluids, solids-laden fluids and those that are shear sensitive. There are exceptions, including many slurry and recessed impeller centrifugal pumps for pumping solids and abrasives.
Both types of pumps require corrections for viscous fluids but those for centrifugal pumps are limited to 2,000 to 3,000 centipoise (cP) and Newtonian fluids. The corrections to a centrifugal pump are severe at the higher viscosities, and they often are not applied to fluids above 400 to 500 cP. AODD pumps have higher viscosity limits and can pump non-Newtonian fluids as well. Fluids such as paints, food products, clay slurries and soaps/detergents are typical AODD applications.
Portability
While both centrifugal and AODD pumps can be arranged to be portable, it is generally easier to do with an AODD pump—especially in outdoor environments. For example, self-priming centrifugal pumps are often teamed with a gas or diesel engine and arranged on a framework to be portable. Since trailer or truck-mounted air compressors are widely available to power many types of pneumatic equipment used outdoors, it is more common to see AODD pumps in that environment.
AODD pumps are the natural type of pump to take advantage of the portability of that motive power source and require no special designs to do so. AODD pumps can also run submerged in fluid without special motor enclosures, which can be useful for mining, construction and some marine applications.
Never has it been more important for the application engineer and pump user to choose the most efficient pump for the job. When applying centrifugal pumps, that means plotting the system curve and keeping the operating point close to the best efficiency and using variable frequency drives rather than valves on friction systems. Doing so optimizes the high design efficiency that is the hallmark of centrifugal pumps.
AODD pumps will never compete with the vast hydraulic coverage of centrifugal pumps nor be as efficient. But, despite their inefficiency, they have become popular because of their versatility.
References
Paraphrased from U.S. Department of Energy Office of Industrial Technologies’ Energy Tips—“Determine the Cost of Compressed Air for Your Plant.”