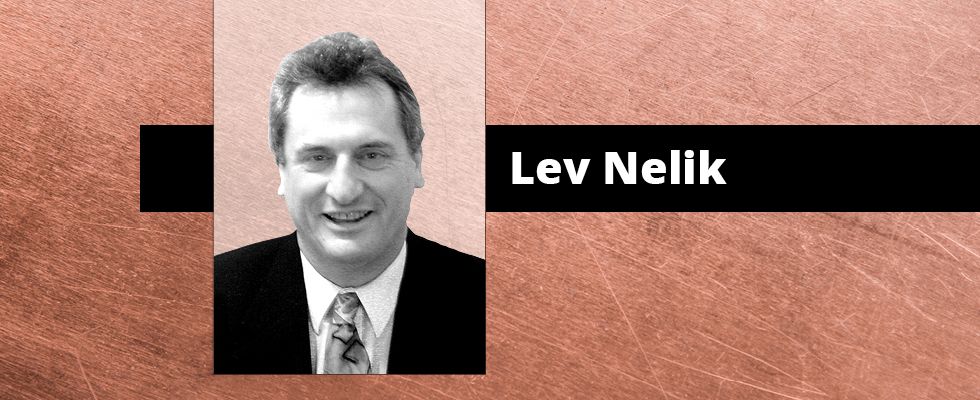
The intent of the recently published current vertical pumps repair specification (VPRS) is to apply it primarily to large vertical turbine pumps with power levels over 500 horsepower (hp) and/or bowl sizes over 12 inches. As discussed in the body of the document, there are essentially three levels of repair that may apply to a vertical turbine pump. Ideally, not only do all worn parts need to be replaced, but also the final stackup of tolerances must be such that the entire rotating assembly is properly centered within the stationary components of the pump, as well as properly aligned to the driver. Excessive eccentricity (lack of proper concentricity) between mating parts could be even more problematic than incorrect clearance.
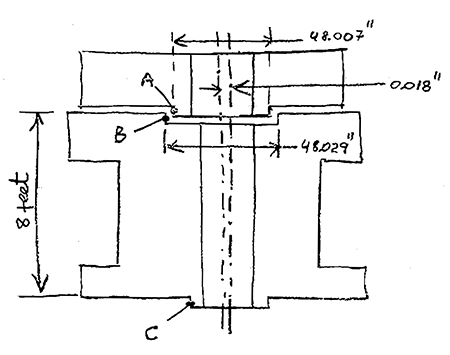
For example, if a clearance between the impeller wear ring and casing wear ring is 0.020 inches instead of the maximum allowed 0.016 inches, more leakage will result in a decrease in flow and efficiency but may not result in immediate or quick failure. However, a 0.005 inch allowed concentricity made instead to be 0.020 inches between the shaft and a guide bushing could result in actual contact between these parts, resulting in catastrophic consequences.
For smaller pumps with a lower power level, the unfortunate present practice by most repair facilities is simply to replace worn parts, paint the pump and deliver it back to the site. The effort and expense to measure and restore eccentricities is rarely done, mainly due to most repair facilities handling small pumps lacking the proper machinery to restore eccentricities, which is also perceived as an unnecessary expense.
As a result, a small pump may wear out too soon, vibrate and be removed after just three to five years, rather than potentially operating well for 15 to 20 years.
For larger pumps, however, a more thorough examination, documentation and restoration of internal concentricities must be done. The added investment in cost is often—although unfortunately not always—seen as justified.
Conscientious end users take time to prepare detailed specifications of the repair process, with greater attention to technical details. A team reviewing the project would involve maintenance, operators, engineering and procurement professionals.
For example, a large 48-inch vertical pump may cost $100,000 to rebuild properly, of which restoration of the eccentricities portion of the cost might be approximately $10,000, i.e., 10%. For a smaller (6-inch) pump, the total cost without restoration of eccentricities could be approximately $10,000, and restoration of eccentricities could be around $5,000, which is 50% of the cost. When competitive bids are considered, the seemingly high proportion of an added 50% cost would usually be considered an unneeded option by purchasing, with the engineering group rarely being involved or having much say in this process. For larger pumps, on the other hand, the engineering group is more likely to be involved, and the reliability aspects include the total cost of quality, which includes the cost of the probability of failure. Because of this, such considerations take an elevated priority.
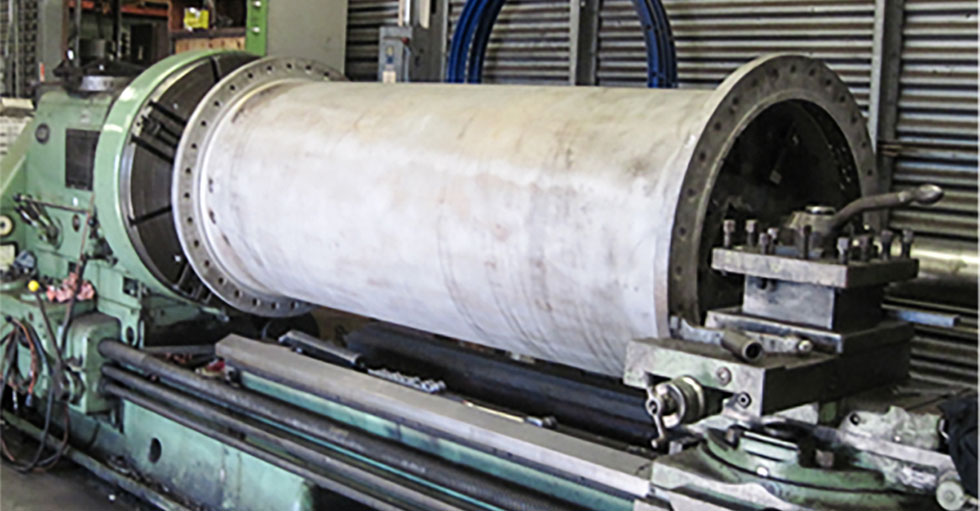
Understanding the impact of eccentricities restoration versus clearances is critical. Manually measuring a 48-inch bowl rabbet fit diameter is not a trivial task. Most small repair shops do not have large and expensive calipers to measure such diameters, and even when they do, the exact determination of the eccentricities is impossible when using handheld tools. Instead, this measurement requires the setting of parts (column, support head, bell) on a large lathe or a vertical milling machine.
Determining eccentricity between rabbet (register) fits at opposite ends of the 48-inch pipe column is impossible without such a large lathe, and the time and expenses associated with that typically appear excessive to the end user. In many cases, it is the setup time to install such a large column pipe on the machine that may cost 90% of the effort, with the machining time itself taking only the remaining 10%. In other words, once the column pipe, a bell or a discharge head is finally installed on the large lathe to measure dimensions (clearances and eccentricities), it is worthwhile to go ahead and take the restoration weld-up and skim cuts at the same time.
For medium-sized pumps, the approach depends on the end user’s awareness of the need as described above. Some end users may see a full restoration of eccentricities as a critical part of the repair process, while others may not. One of the main objectives of the VPRS document is to help educate the end users on the importance of proper repair, as well as to present the cost of quality and the consequences of not following it. Understanding the difference between a clearance between parts versus eccentricity between the same parts is an important starting point to begin to properly understand what a quality repair means and why it should be performed.
In Image 1, there is 0.022 inches of clearance between surfaces A and B, which would be acceptable, if, for example, the allowable max clearance is not to exceed 0.025 inches. However, there is a 0.018 inch eccentricity between surfaces B and C, which means that once the shaft is inserted through these parts it would hit the side. Considering the 8-foot length of parts in this example, it would be impossible for a repair shop to measure concentricity without setting the lower part on the machine (such as a lathe or a mill) and measuring concentricity between surfaces B and C by using the lathe. This would need to be done in a single setting, without rechucking, or by machining an additional control surface (a “cheater cut”) somewhere along its 8-foot length to establish a concentricity reference plane if the part needs to be rechucked and flipped.
This standard specifies requirements and guidelines for the evaluation of existing vertically suspended pump installations as well as the execution of pump repair and upgrades. For this standard, the pump installation includes the pump, driver, electrical system, intake structures and piping.
As noted, this standard focuses primarily on engineered quality repairs, per Level 3. Levels 1 and 2 are described within the standard mainly for general comparison and information for those interested.
This standard does not apply to new pump installations, vertically overhung pump services or submersible motor-type pumps, including deep well or hermetically sealed pumps.
On a final note, if you will find the subject of value and interest and would like to get involved in future releases of revision of this standard (currently Rev. 1B), let us know, and the advisory committee will be glad to involve you. We always benefit from pump professionals and enthusiasts joining in this important work. This will be not limited to vertical pumps, as we plan to expand it to other types, such as double suction, end suction and more.
References
A. Hydraulic Institute (various editions, hard copy or CD)
B. PIP Practices
C. API-610 (various editions)
1 = “Repair Standard for Vertical Pumps”, Pumps & Systems, February 2012, pp. 16-17
2 = “Vertical Turbine Pump Reliability”, P&S, March 2010, pp. 16-19
3 = “The Downside of Perfection in Vertical Turbine Pumps Repair”, P&S, May 2009, pp. 8-9
4 = “Finding the Root Cause of Failure”, P&S, April 2009, pp. 10-11
5 = “Repair, Overhaul and Upgrade of Vertical Turbine Pumps”, P&S, January 2008, pp. 14-16
6 = “Repair and Upgrade of Multistage Centrifugal Pumps”, P&S, December 16-17, 2007
7 = Pumps Reliability and Efficiency/Energy Monitoring System (PREMS-2A):
pumpingmachinery.com/consulting/PREMS-2A/prems-2a.htm
8 = “Pumps and Pumping Systems – Made Easy and with Fun”, 3 Volumes, Nelik, L., The World of Ideas publisher, via Amazon
9 = VERTICAL PUMPS REPAIR SPECIFICATION (VPRS), REV. 1B, Editor L. Nelik, World of Ideas Publication, Amazon