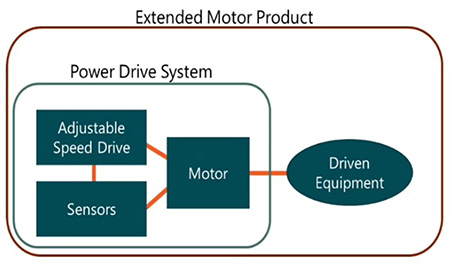
New research points to opportunities to reduce costs in both variable flow and constant flow applications by using an existing technology: variable frequency drives (VFD). By using VFDs, also known as adjustable speed drives, the energy waste inherent in petroleum, chemical, HVAC and other liquid pumping systems could be cut. Additionally, the payback period for installing new equipment was estimated to be four to 10 months on the energy savings alone.
The Cadeo Group is an energy-focused research firm with experience providing analytical and programmatic support for the Department of Energy, the Northwest Energy Efficiency Alliance (NEEA), various industries, state agencies and local utilities. The specific researchers, Sarah Widder and Nate Baker, applied their chemical and civil engineering backgrounds and experience with energy efficiency and motor-driven equipment to examine data collected by the National Electrical Manufacturers Association (NEMA) and NEEA.
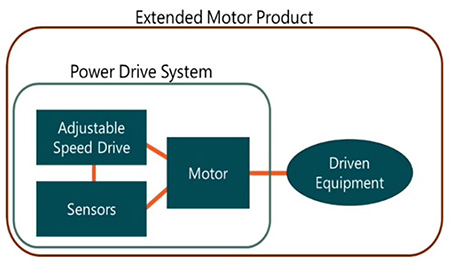
Plant managers may face pressures to cut costs. However, with the current state of the economy, many industries, especially within the petroleum and chemical producing sectors, have an increased urgency to locate potential cost savings. The Cadeo white paper, available on the NEMA website, acknowledges that most modern motor efficiencies already exceed 95%, so further development of motors will be unlikely to produce significant energy savings. Instead, their findings target the inherent waste of stacked margins.
Reducing Overdesign Margins
Everyone designs for a margin of error. However, after adding up the reasonable and appropriate margin of error for each component in a system and the margins of error built into the system, the stacked margins can lead to inefficiencies.
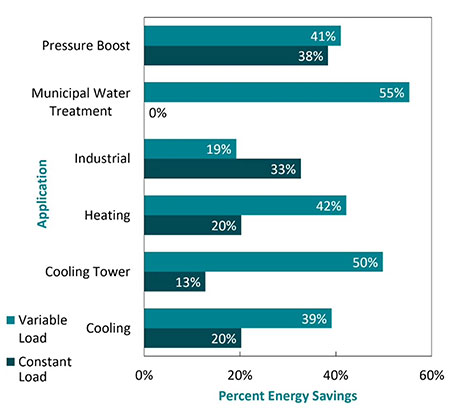
For example, consider the pumping portion of a chemical processing system that targets a flow of 100 gallons per minute (gpm). The system designer understands that there will be variance in the system, so to avoid a negative variance of 90 gpm, they do not design for 100 gpm, but aim for 105 to 110 gpm. Then, when selecting the pump motor requirements, if the design specs require a 400 horsepower (hp) motor for 100 gpm, they add 10% and recognize they need a motor with 440 hp. However, the closest option offered by manufacturers is 450 hp, so they must buy more power than they need. A similar margin variance can be found at each point in the system’s design resulting in far more capacity than required.
Cadeo Group Findings
In their research, the Cadeo Group wanted to understand the energy and nonenergy benefits of installing power drive systems with VFDs in various applications, including constant speed applications.
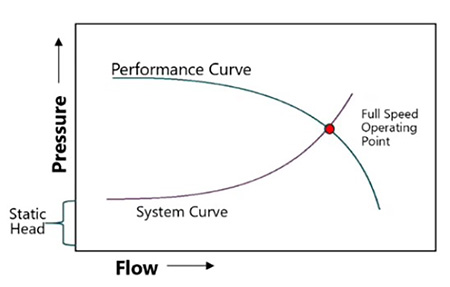
The study focused exclusively on variable and constant speed pumps that had been measured by NEMA and NEEA. While the findings are expected to be representative of other variable torque applications, the Cadeo Group wanted to conduct additional research to understand the variances stemming from operational practice between pumps, fans, compressors, conveyors, escalators, etc.
The pump study verified the expected energy savings of variable speed systems and estimated energy savings between 19% and 55%. In ascending order, the study examined the following six applications: industrial, cooling, pressure boost, heating, cooling tower and municipal water treatment. The study calculated the average power saved to be 43% and the average power difference normalized to be 0.24 kilowatts(kW)/hp. Using a national average of $0.12/kilowatt hour (kWh) for electrical power, variable load applications result in average energy savings of 895 kWh/hp/year and an expected payback of four months from the energy savings.
More notably, the study also found power savings by using variable speed control for constant load applications. Constant load applications were defined as any application where 95% of the operating hours were run at a specific flow rate and energy savings between 0% and 38% were calculated for replacing constant load systems with variable load systems. Overall, the study calculated an average savings of 23% and 0.194 kW/hp. At $0.12/kWh for electrical power, the use of variable load systems for constant flow applications resulted in average energy savings of $349 kWh/hp/year and an expected payback of 10 months from the energy savings.
The Savings Source
To explain how such a cost savings is possible, recognize the inherent differences between the variable flow system design and the constant flow system design. When a variable speed pump control is used within a system, the energy use follows the system’s energy usage curve. Reducing the flow naturally reduces the energy usage.
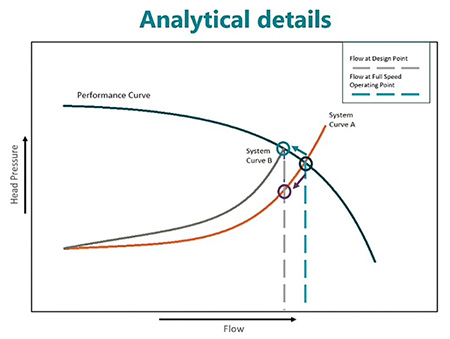
For a constant flow system design, the system runs at a single rate that moves along the performance curve for the pump. For the purposes of the analysis, the most commonly used flow rate was considered to be the best efficiency point (BEP) for the constant load system and the full-speed operating point.
The cost savings come from recognizing how the stacked margins contribute to the performance and system curves. The extra margin for the pump changes the location of the best operation point on the performance curve. Throttling the pump will consume the same amount of energy even though the increased pressure and flow is not needed.
Adding a VFD system to a constant flow system’s motor will allow many plant managers to eliminate the unneeded pressure, unneeded flow, and recognize potential savings. However, it must be noted that some older motors may need special considerations when applying a VFD. Naturally, these details will affect a specific plant’s breakeven point for a conversion.
Of course, the electrical costs only represent one form of savings possible in adopting the variable speed control system. Managers will find decreased maintenance costs from the soft starts for variable speed pumps and improved ability to maintain performance for their systems. When one considers how a common form of throttling is to bleed off some of the system output to feed it back into the system, it is easy to see how the system will recognize reduced costs and increased production. Other process improvements include improved control, improved system flexibility, and increased data feedback through internet of things (IoT) connections.
With the current economic uncertainty introduced by the COVID-19 pandemic, plant managers have more pressure than ever to cut costs. Applying a VFD to an electrical motor system allows a plant manager to reduce the waste introduced to a system by stacked margins of error and will provide extra flexibility to adapt to changing needs. Although the payback period is shortest for a variable load application, constant load applications will also exhibit energy savings and a shorter term payback.