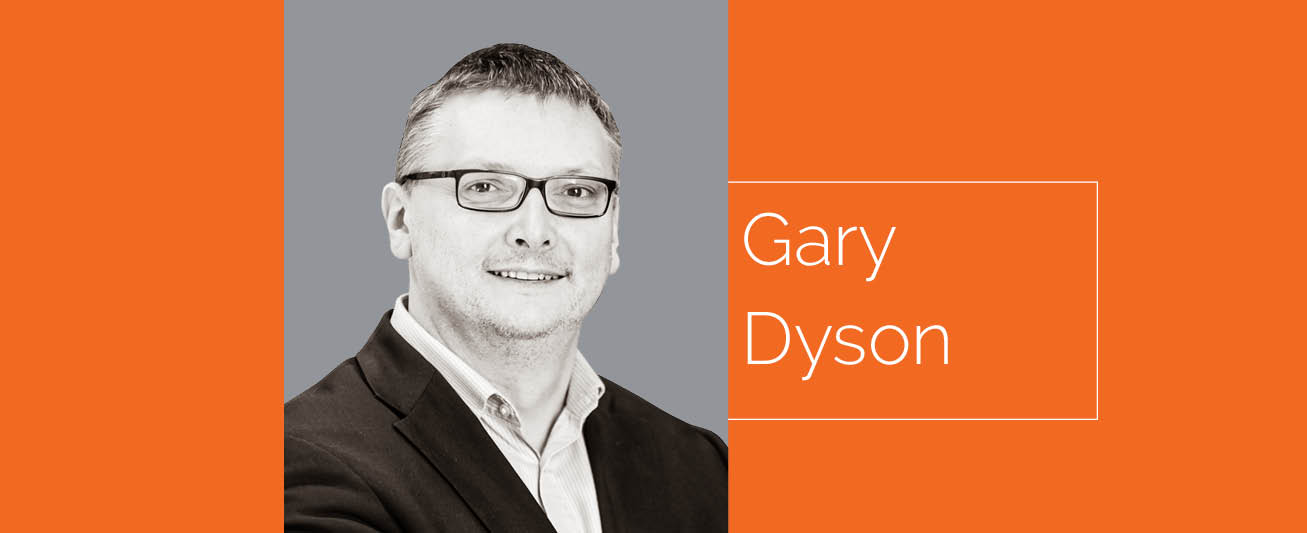
Vibration measuring and monitoring has become one of the most important factors when determining the health of a machine. The levels set by American Petroleum Institute (API) 610 have been widely adopted, and a great deal of effort has been made to ensure that even the smallest machines are equipped with vibration measuring equipment.
There is now a lot of equipment available to retrofit sensors to pumps. Using the data, though, can be difficult as each system appears to offer a vast array of data options without much guidance on how the data can or should be used.
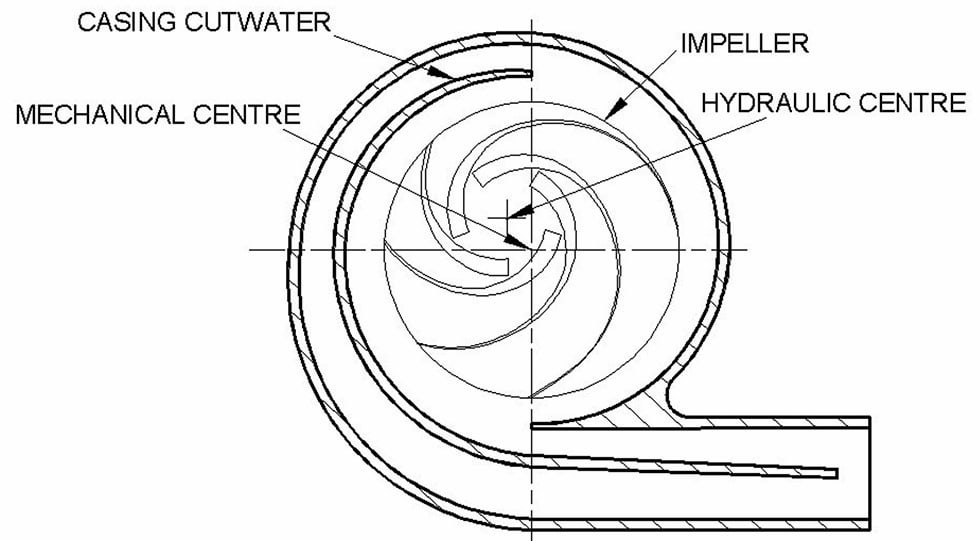
Layer on top of this data the enormous amount of analysis capability—such as operating deflection shape (ODS) and modal—and the new systems such as motion amplification and the volume of data can be overwhelming.
Every pump vibrates. If it doesn’t, it is not in operation. Monitoring the vibration of the machine has never improved the reliability of the machine. Building a picture of the health of the machine and taking action based on this, and understanding the overall picture, is the key to reliability improvements.
Pump Vibration Data
Pumps have specific frequencies that can generally be associated with a machine in operation. These are good places to start with monitoring.
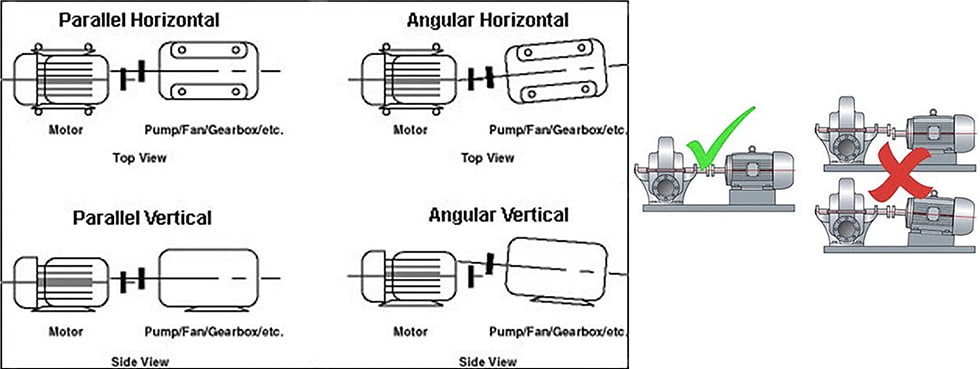
1x rotational speed
This is generally associated with the mechanical balance of the pump. There is also an element of hydraulic unbalance caused by the machine rotating passageways being filled with liquid. Small changes in the shape between each impeller channel cause the weight of rotating fluid to be different between each channel. No matter how well balanced the impeller is in air, there will be some element of unbalance as 1x when the impeller is in operation. 1x is inevitable.
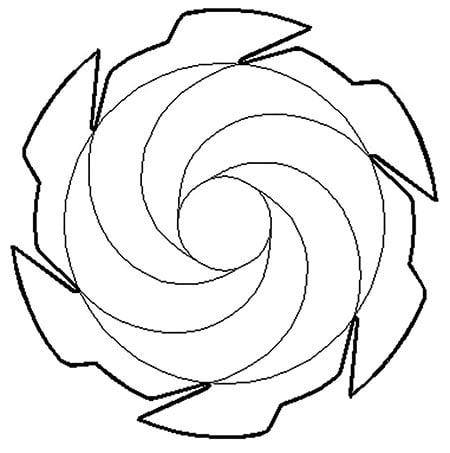
2x alignment
This is generally associated with the quality of the alignment of the pump to the driver. Using sophisticated alignment tools helps to reduce the 2x alignment frequency but it will never be eliminated. 2x is inevitable.
Number of Impeller Vanes x Rotational Speed—Vane Pass & Its Multiples
Pumped liquid progresses through the impeller and gains energy, and this energized liquid passes from the impeller to the volute or diffuser. There is an inherent variation of velocity across one impeller pitch (Image 4) and passing this on to the collector causes the vane pass vibration and its associated multiple. Using an analogy of a rotating saw tooth as a mental image helps to fix this concept in the mind.
Understanding these fundamentals and how these are changing is a good start in understanding what is happening to the machine. Using vibration monitoring that can produce a spectrum and phase data gives a much better view for diagnosing and catching emerging issues.
Taken alone, vibration gives users a small proportion of the picture, and there are many more questions to ask.
For example:
- How was the machine started?
- Was it ready?
- What are the bearing temperatures? How are they changing?
- Where is the machine operating on its curve?
- How is the operating regime changing with time?
- What is the suction pressure?
- What is the discharge pressure?
- What do you see?
- What do you hear?
- How is the piping?
- How is the foundation?
- Is everything in place—missing, bolting, etc.?
- How was the machine stopped?
Having a feel for the overall condition of the equipment is as essential as the remote vibration data. Once you have built a strong mental picture of the machine, then the vibration data becomes valuable. Without that mental picture, the data is just information without context.
Vibration measurement and monitoring are valuable tools in the fight against poor reliability. Alone, though, it is not enough. Fundamental understanding, relentless and thorough investigation in order to identify initiating events, in addition to machine modification to mitigate and eliminate the fundamental causes of the reliability problems, are what actually make a difference.
If you accept poor reliability, that’s what you will get.