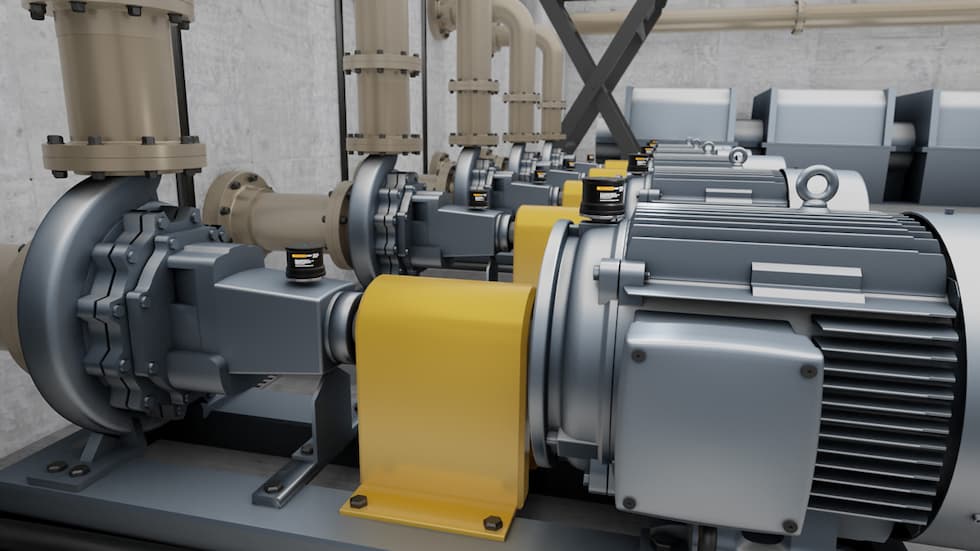
It is normal for machinery to vibrate, but excessive vibration prematurely causes wear in components and can shorten asset life. Changes in a machine’s vibration patterns are an indicator of potential problems. Monitoring vibration to screen for any changes helps teams identify imbalance, looseness, misalignment or bearing wear before failure occurs. Vibration sensors can monitor changes to the amplitude, frequency and pattern of vibration in motors and other machinery.
The data collected by vibration sensors can then be analyzed to identify faults and determine how severe they are. Knowing which machines need urgent attention and which do not helps maintenance teams prioritize their work most effectively.
Predictive maintenance (PdM) is an approach to asset management that relies on operational data to determine when a physical asset needs service. Using a predictive maintenance approach can reduce maintenance costs by preventing equipment failures before they occur.
One way that maintenance costs are reduced is that emergency repairs are minimized or eliminated; another is that unnecessary calendar-based maintenance actions are minimized or eliminated. When basing maintenance actions on actual asset data, the right repairs can be done at the right times. Vibration sensors can be an important component of a predictive maintenance program. Like many other technologies, vibration sensors have become more affordable over time. This makes them an accessible and scalable way to monitor machinery. Still, there are some common misconceptions about when and how to use vibration sensors.
How to Choose a Sensor
They are not a one-size-fits-all solution; no vibration sensor works for every single asset, application or budget. Motors come in many configurations and are used to drive a wide range of equipment types. Other variables to consider include the setting and accessibility of the motor.
Typically, most motors run about the same most of the time. This consistency helps make vibration monitoring and analysis straightforward and effective. In some applications or processes, there are many more variables which means a more sensitive vibration sensor and more advanced vibration analysis may be required. When it comes to rapid condition changes, structure testing, resonance testing and reciprocating motion, vibration analysis can be more complex. The right vibration sensor is the one that will provide the volume and depth of data needed for effective vibration analysis.
Most vibration sensors available today use accelerometers. This includes micro electro-mechanical system (MEMS) sensors, which have high ratings for their lower frequency response. They are cost effective and offer a long battery life, making them a good choice for vibration screening at scale. Suitable for a frequency range of 0 to 1,000 hertz (Hz), MEMS sensors are ideal for detecting problems that stem from faults including imbalance, misalignment and looseness.
For higher frequency ranges (over 1,000 Hz), a piezoelectric sensor is a better choice. This frequency range is where issues with bearings, gear mesh and motor bars can be identified. Compressors and gearboxes are examples of assets that may need this type of monitoring.
Some industrial settings require higher Ingress Protection (IP) ratings. For example, some manufacturing environments expose equipment to dust, liquids or other harmful things. Piezoelectric crystals are impervious to moisture, dust and smoke, making them a good choice for vibration sensors in such settings.
For motors in hazardous or hard-to-reach areas, consider the battery life of vibration sensors. Sensors that do not require frequent battery replacement—some sensors do require battery replacement as frequently as every year or two—are beneficial because they require fewer trips to difficult areas for maintenance technicians. In some instances, the amount of time it takes to get in and out of personal protection equipment (PPE) or to shut down a machine to reach the right spot means that teams do not get measurement data from those machines on a regular basis.
In some cases, motors are high enough that accessing them can be dangerous. Other motors are located behind panels, in tight spaces or in areas with hot steam or potentially harmful materials. Wireless vibration sensors can be used for remote vibration monitoring of motors in such settings, sending vibration data at regular intervals. Teams can stay updated on equipment condition without needing to take frequent trips to areas that present heightened risks.
Some equipment can be monitored well enough with vibration sensors that provide simple, high-level screening. Other assets need sensors that can provide some diagnostics. How critical a piece of equipment is to operations can determine what kind of sensor is the best fit.
How to Start a Vibration Monitoring Program
Despite the misconceptions some people may have, adding sensors does not mean eliminating routes or eliminating jobs. Maintenance teams already stretched thin may think that they do not have the capacity to add a sensor system. They may also be wary of the upfront cost.
Rather than replacing people, vibration sensors help users do their work more effectively. Vibration sensors also do not have to be used on every asset for a vibration monitoring program to be effective. In fact, starting with too much too soon can ensure that vibration monitoring efforts are not effective at all.
Instead, it is recommended to start with a small, focused pilot program. Once a team has some findings and results, it
can decide how to best expand the program. There is no need
to cover everything at once and no need to spend a lot out of the gate.
Using Vibration Data Effectively
If a maintenance team gets bogged down with too much data, that data can become a nuisance instead of a tool. Plan for what to do with vibration data once it is collected. Different sensors collect different types of data at different intervals. The best sensor for any application is the one that will provide the most useful data—and not just the most data.
The right sensors, software and analysis combined ensure an effective vibration monitoring program. Vibration analysis does not have to be done in-house—not all teams have the budget to have a vibration analyst on staff. Expert consultants can provide vibration analysis on an as-needed basis.
Vibration data should provide the answers to a few questions:
- What is the fault?
- How severe is the fault?
- What action should be taken and when?
The right sensor will provide the information needed to make the appropriate maintenance decisions. Over time, trending vibration data also makes it possible to gain insight into overall asset health, identify potential faults sooner and optimize maintenance time and efforts.
While a handheld vibration tool might identify a potential fault a couple of days in advance, monitoring with vibration sensors provides more coverage and more data and can commonly indicate potential problems months in advance—or more. Early warning of faults helps teams avoid “fire-fighting mode” and reduces costly unplanned downtime.
Taking any off-the-shelf sensor and mounting it on a machine is unlikely to be effective or lead to useful results. For a vibration monitoring program to be effective, maintenance teams need to consider the hardware they use, the software they use and what their internal and external support will look like. Considering these factors when choosing and implementing sensors can help ensure a successful vibration monitoring program.