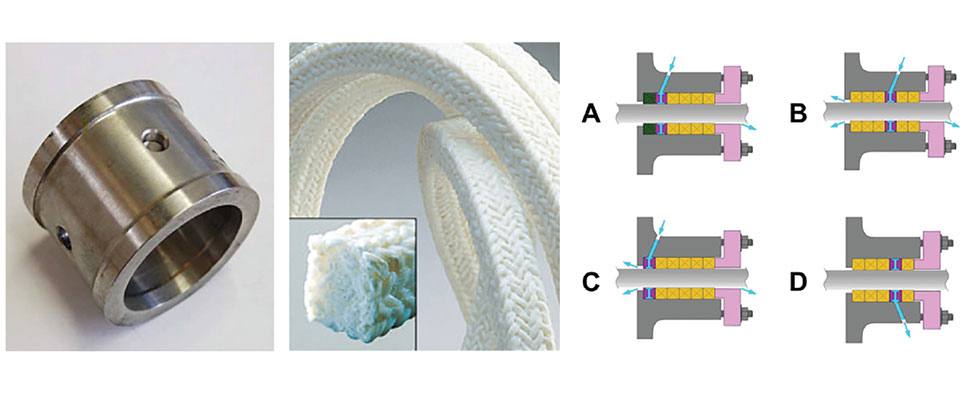
IMAGES 1-3: Active flush with lantern ring; braided sealing rings; packing ring orientations 2L3, 3L2, L6 and 3L1 (Images courtesy of the Fluid Sealing Assocation)
The spring and summer of 2022 was one of the driest in the Northeastern United States. According to the National Weather Society, the rainfall in 2022 was one of the lowest in 20 years. Many rivers, lakes and reservoirs dropped to levels that had not been seen before. Weather reports described how local towns and cities across the state of Massachusetts were experiencing drought conditions with severe consequences to these communities. The National Drought Mitigation Center (NDMC), a part of the University of Nebraska-Lincoln, the National Oceanic and Atmospheric Administration (NOAA), and the U.S. Department of Agriculture (USDA) describes five classifications for drought conditions. The first level of drought is classified as abnormally dry (D0). These are areas going into or coming out of drought. The other four classification levels are moderate (D1), severe (D2), extreme (D3) and exceptional (D4). Across most of Massachusetts, the drought conditions ranged between D2 and D3. The national news reports told of other areas across the nation experiencing similar problems. Lake Mead in Nevada and the Great Salt Lake in Utah were at their lowest levels. It is staggering when you compare the total volume of cubic gallons of water once held by a lake or reservoir to the current levels without being concerned.
There are industries that rely on large volumes of water for production processes—such as pulp and paper, mining, hydro power and more. Industries that have these processes that are using packed pumps use an active flush with a lantern ring (Image 1) to extend the performance of the braided sealing rings (Image 2).
There are several reasons for using a flush. One would be to remove or reduce the amount of abrasive material from entering the stuffing box. Another purpose could be to help lubricate and cool surfaces between the packing ring’s interior diameter (ID) and the shaft sleeve’s outer diameter (OD) particularly for higher shaft speeds. Sealing higher speeds with braided packing rings that use dryer fiber materials can generate higher temperatures due to the frictional heat, which in turn will affect the longevity of the packing rings life. With the advancement of modern fibers and lubricants, braided packings have progressed to not requiring flush water to cool or lubricate.
Many times, plant and maintenance personnel do not take the necessary time to thoroughly evaluate the proper protocols of setting up flush lines to the stuffing box. Mechanical packing rings are perceived as being less sophisticated sealing devices that require greater flush requirements.
1. First, determine the correct packing and lantern ring arrangement. Knowing the packing ring orientation to be a 2L3 (two rings below the lantern ring with three rings above), 3L2, L6 or 3L1 (Image 3) can make the difference between the packing rings lasting for many weeks or only hours. Ensuring maintenance workers have the arrangement information before packing the pump is crucial or time will be wasted remeasuring the lantern ring location.
2. Second, make certain the correct cross-sectional size of packing is being used. This is extremely important when dealing with any packing arrangement that has rings both above and below the lantern ring. Using the wrong packing cross-section will affect the location of the lantern ring with relation to the flush port and affect the packing performance. To calculate the proper cross-sectional (c/s) size of packing and number of packing rings in a stuffing box, you will need to know the box bore diameter (ring OD), shaft-sleeve diameter (ring ID) and stuffing box depth.
Equation 1: (OD – ID)/2 = C/S; Box Depth/C/S= # of Rings
3. Third, determine the requirements for the lantern flush. An industry practice is running the line off the discharge side of the pump back to the stuffing box. The thought behind that solution is that it will generate plenty of flow into the stuffing box to maintain an effective seal for the packing rings. However, sending all this additional pressure back to the stuffing box causes unnecessary load and wear on the packing rings. The Fluid Sealing Association has created a formula for calculating stuffing box pressure of a centrifugal pump. Knowing a few values like the pump suction pressure (PS) and the total dynamic head (TDH) will allow you to calculate the approximate stuffing box pressure (SBP). Use Equation 2 to determine the stuffing box pressure of an end suction pump:
Equation 2: SBP = PS + [25% (TDH)]
Once an approximate value for the stuffing box pressure has been determined, add an additional margin of safety. The rule of thumb for setting the flush pressure is 1 bar or 14.5 pounds per square inch (psi) over the stuffing box pressure. This additional increase to the flush pressure is good insurance to help compensate for any changes in the system or head pressure so the flush continues to maintain a positive flow.
There are options for flow control devices to help maintain proper flush pressure to the stuffing box. Flow meters are designed to maintain and regulate flush water into the stuffing box. Using these types of devices can help minimize the amount of water being added into the process medium. This saves energy if the production medium needs to be reheated or the water removed. When considering which type of flow meter is right for your application, it is important to understand the variety to choose from, such as differential pressure, velocity, positive displacement, mass and open-channel flow meters. When selecting a flow meter, consider these factors to make the best choice for the application.
Not every flow meter works perfectly in every application. The reality is that there are many types of flow meters each offering various advantages and capabilities. There are a few considerations to help guide you in a better direction when selecting. What is the type of fluid, liquid or gas? How dense or viscous is it? Does it contain contaminants or bubbles that could affect the reading? Is the fluid flow considered laminar or more turbulent? These are all important questions that need to be answered before selecting a flow meter.
Some industries are less concerned about water consumption because it comes at a low cost, while other industries have higher costs associated with the usage of operating a flush. Water is one of our basic needs, an extremely valued resource we all take for granted. We should all do our part to conserve and protect this resource.
To learn more about mechanical packings, visit the Fluid Sealing Association website at fluidsealing.com.
We invite your suggestions for article topics as well as questions on sealing issues so we can better respond to the needs of the industry. Please direct your suggestions and questions to sealingsensequestions@fluidsealing.com.