Every raisin of the 50,000 tons of raisins processed annually at the National Raisin Co. plant in California undergoes a 35-cyle cleaning process and a thorough quality inspection before shipment. During this rigorous process, between 60,000 and 80,000 gallons of wastewater are generated each day, mostly from washing dust, sugar and other contaminants away from the raisins. As sales and production have increased, so have the company’s wastewater costs. While the family-owned company based in Fowler, California, investigated ways to reduce the plant’s operational costs, it also considered how to minimize the environmental impact of its processes on the close-knit community of 6,000. The wastewater produced by the plant contains sugar and other byproducts from the raisins that create a high biological oxygen demand (BOD). Water with BOD used for land irrigation requires special permits and ongoing regulations to ensure that groundwater quality is not compromised. Water with BOD can also produce offensive odors when disposed of via land application. This sugar-laden wash water must be treated to remove contaminants, but transporting it to a municipal treatment plant would be expensive—approximately $50,000 per month. To remove the sugar from the wash water, the company opted for a reverse osmosis process—the most economical and environmentally friendly solution. This process produces wastewater with lower levels of dissolved solids than the well water that feeds the plant, so the facility can safely reuse the wash water in the raisin cleaning process or to irrigate nearby vineyards. When National Raisin Co. began reusing its water, the company’s sewer bills dropped by approximately $300,000 per year, earning a return on investment in about three years. During this time, the company also partnered with a local distillery that wanted to purchase the treated wash water to make grape alcohol.
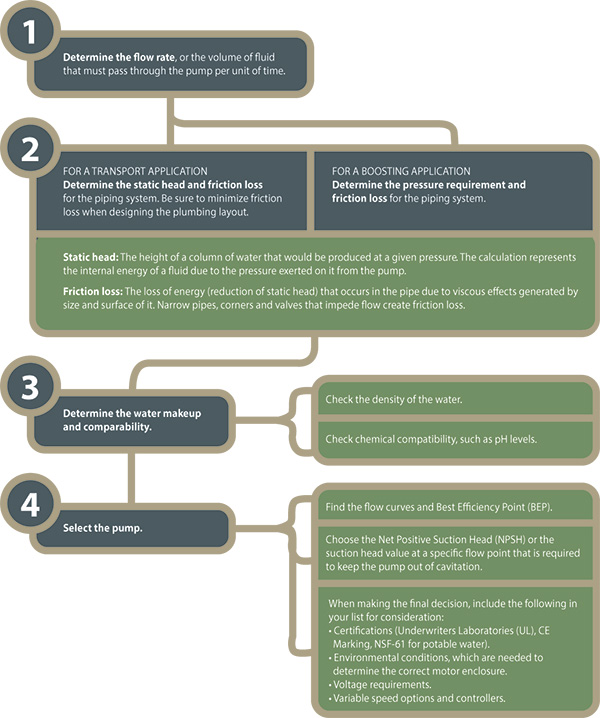
The Solution
When a conventional treatment process is not adequate for meeting the required treatment standards, advanced treatment technologies can be used to remove contaminants that conventional treatment processes leave behind. These technologies are designed to meet specific needs, including the following:- Removal of solids and bacteria by microfiltration or ultrafiltration membranes
- Biological nutrient removal with sequencing batch reactors or membrane bioreactors
- Removal of dissolved organics or salts with reverse osmosis
- Removal of trace contaminants and pathogens through oxidation and disinfection
- Removal of dissolved organics and contaminants through adsorption or ozone-enhanced biological active filtration
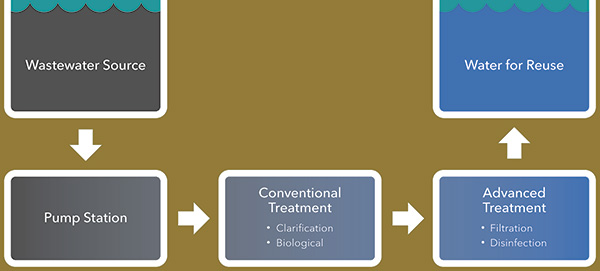
Pumping Systems
Treating water is only the first step to ensuring that a plant recycles and reuses wastewater efficiently and effectively. Organizations must also consider the transportation and storage of water reuse. Treatment and pumping systems are primary energy consumers within a water or wastewater loop. Sizing the system and selecting the right equipment to meet specific reuse requirements are critical to maximize energy savings over the life of the equipment. Pumps serve two purposes in a reuse system: transportation and pressure boosting. Water must be moved from one location to another for treatment, storage or use. Some treatment technologies require pressure boosting, including reverse osmosis, in which specific pressures are required to move water through a membrane. Many reuse applications, such as irrigation and equipment washing, also require boosting capabilities.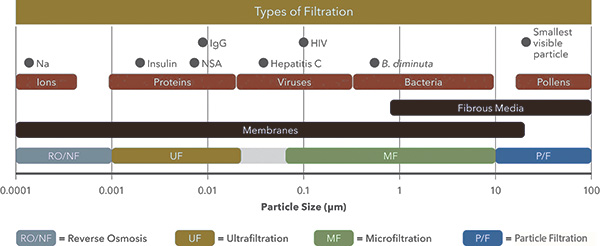