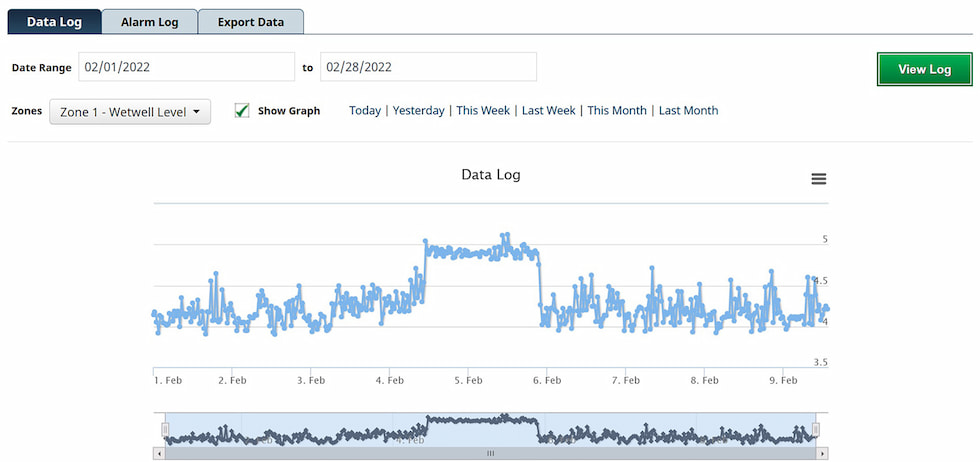
Operators of water and wastewater management facilities use remote monitoring systems connected to a variety of sensors and accessories to keep tabs on important environmental conditions such as temperature, humidity, water leak detection, power failures and unscheduled entry.
These systems are also used for preventative pump maintenance when they are programmed to watch specific conditions that could point to a problem with the pumping system. For example, users can use a remote monitoring device to observe pulse counts to detect total flow output from a pump, as well as follow runtimes to avoid overworking a pump or generator. In addition, they can monitor equipment vibration as an early indicator of an impending malfunction.
Fundamentals of Remote Monitoring
A monitoring system can be installed at both staffed facilities and unattended sites. It consists of a base unit that constantly collects data from sensors or existing equipment. The number of external sensors applied depends on how many inputs are on the base unit. Users program the device to designate the necessary high or low parameters on the monitored sensors. The base unit contacts designated personnel when a sensor reading moves out of the preset limits. Managers can receive these notifications via phone, email or text.
Users can also access real-time and historical data log information to look for trends that could suggest a problem and generate records to use in preparing regulatory reports. This information is helpful in determining if certain equipment and components are not performing at a satisfactory level.
Monitoring Flow Rate Levels
Facility operators can wire a remote monitoring system to a flow totalization meter, which measures the amount of liquid or gas traveling through pipes and emits a pulse with each turn, or several turns, of its wheel.
The monitoring system is then programmed to read, count and interpret the pulses to alert personnel of changes in the flow of the current. Once the monitoring device is installed and programmed, it will display the total amount of liquid or gas passing through the pipe in real time. Users can set high- and low-flow limits and set the unit to send alarm notifications when readings fall out of this range.
Monitoring Pump & Generator Runtime
Observing runtimes on pumps and generators is useful for managing active hours of operation and scheduling maintenance, which can extend the life cycle of the equipment. Many pumps and generators have relays or switches that change positions when the pump is on. In these situations, operators can wire a monitoring device to them to detect when the pump or generator is switched on and maintain an ongoing log of the time. Users can program the monitoring device to send an alert when the runtime has reached a certain number of hours.
Peace of Mind Operating Older Pumps
Monitoring pulse counts and runtimes is an easy way to keep an eye on operational data from remote locations that have older pumps and generators. Of course, many modern flow meters offer a 4-20 milliamp (mA) or Modbus output that provides automatic, user-friendly operation. In fact, certain generators or pumps have built-in smart Internet of Things (IoT) functionality. However, for operators of legacy pumps and generators, using a remote monitoring system with existing flow meters is a cost-effective way to know whether everything is functioning properly.
Monitoring Vibration
When vibration characteristics of pump components change, it might be a signal that they are damaged and on the brink of failure. For instance, vibration increases when an impeller breaks or pump bearings or seals begin to wear out. Personnel often cannot see or hear this subtle change but a vibration sensor installed in the pump can detect it easily. The sensor focuses on a pump’s acoustics to identify imbalances, providing early warning of changes occurring within the pump.
Vibration sensors measure the vibration velocity of the pump ranging from 0 to 25 millimeters/second (mm/sec [root mean square]) over the frequency range 10 to 1,000 hertz (Hz). For example, an output of 4 mA is consistent with no vibration at 0 mm/sec, whereas an output of 20 mA indicates intense vibration at 25 mm/sec.
Low-frequency vibrations can indicate system faults like pump bearing fluid lubrication whirl. Mid- to high-frequency vibrations can reveal malfunction of the drive motor or impeller. Very high-frequency vibrations can suggest high-pressure leaks, entrained gas and pump cavitation, as well as emerging faults on castings, piping, rotors and bearings.
Vibration sensors are permanently attached to the equipment by a magnetic mount or screwed in via the sensor’s threaded mount. Next, they are hard-wired to the remote monitoring device. Then, the user programs the system to send alerts and log the information coming from the sensor.
Each vibration sensor communicates its frequency readings in real time to the remote monitoring device. When the system detects a reading outside of the preset range, it sends a notification to designated operators. This gives personnel time to take action to prevent equipment failure, secondary damage and costly downtime.
Selecting a monitoring system that also functions as a data logger is helpful for capturing vibration readings at set time intervals. Users can view real-time and historical data to look for trends that indicate a potential equipment failure.
With water and wastewater facilities processing millions of gallons of water every day, it is critical to have a system in place that helps to ensure equipment is running as efficiently as possible. Remote monitoring systems can achieve an extra layer of maintenance protection at the plant.