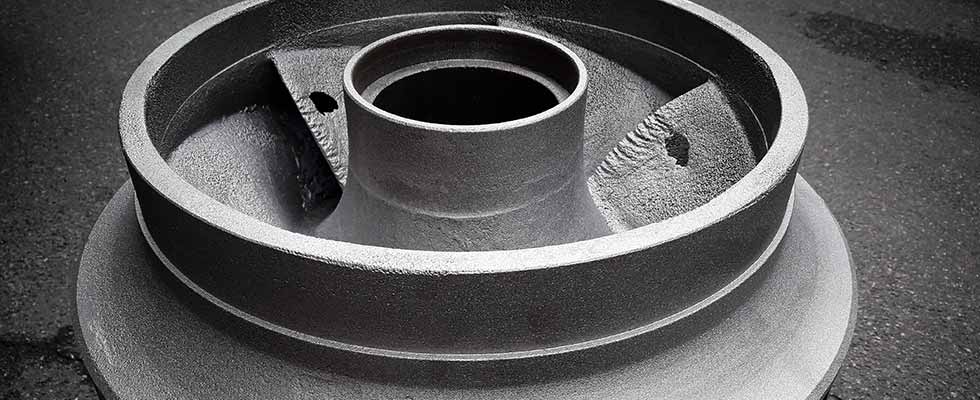
Cavitation is a condition that can affect any fluid flow system. Despite it being an ever-present threat, it is not well understood. In the simplest possible terms, cavitation involves the formation of water vapor bubbles that damage metal components when they collapse back to the liquid phase. Here are some common questions and answers that relate to cavitation.
Does a pump sound differently when it cavitates?
Yes. Cavitation has been described as sounding like gravel or coffee beans in the system.
How does cavitation damage system components?
One aspect of cavitation that is not widely understood is why these apparently harmless bubbles are so destructive when they implode. The answer is in the release of latent heat energy of condensation when the water vapor returns to its liquid phase. The collapse of the bubble and the energy released creates a small pressure jet that can strike a nearby solid surface, potentially damaging it. Because of the large number of bubbles formed in a cavitating system, these bubbles of water vapor can cause extensive damage to system components over time. Because cavitation takes place on the entry to a pump, the first system component that the bubbles encounter is the pump impeller.
Where else can cavitation happen?
Virtually anywhere that water is moving fast. The most well-known locations, aside from pumps, are ships’ propellers, control valve seats and small-bore orifice plates in water pipework.
What causes cavitation in pumps?
Cavitation in pumps is caused by excessively low pressure at the pump inlet. A blockage or restriction such as a clogged filter or part-closed valve mounted on the inlet to the pump can cause it. It can also happen when the pump is having to source its water supply from a sump installed below the pump—called a “suction lift.” Finally, hot water, close to boiling point, is a likely contributor.
Why does hot water allow pumps to cavitate more easily?
When water temperatures are low, the vapor pressure of water is also low. For example, at 32 F, the vapor pressure is a fraction of 1 pound per square inch (psi). As water temperatures rise, the vapor pressure climbs. At 212 F, the vapor pressure is the same as standard atmospheric pressure. At this temperature, when the vapor pressure is the same as the atmospheric pressure, the water will begin to vaporize—turn to gas, in layman’s terms. The commonly known term for this is boiling.
What is wrong with a suction lift?
A suction lift adds more vertical height from the water level in the sump up to the pump. This subtracts from the static pressure available to the water, making it easier for the water to turn to vapor and generate damaging bubbles.
What is happening in the pump when it is cavitating?
Bernoulli’s theorem states that static water pressure in a pipe multiplied by its velocity is a constant. It follows then that if velocity is temporarily increased, water pressure must drop.
As the water passes through the impeller it accelerates, moving from a larger diameter pipe into a smaller diameter as it approaches the impeller, leading to a reduction in the static pressure. If the vapor pressure of the water is higher than the static pressure at this point, water gas bubbles will form.
As the water makes contact with the vanes of the impeller, pressure is increased and the bubbles implode quickly as the static pressure now exceeds the vapor pressure. All is now liquid again, at a price. Depending on the impeller material, damage can be extensive. Cast iron impellers are the worst affected. Stainless steel impellers are less affected, due to the toughness of the material.
How can I predict if a pump is going to cavitate?
First, by looking at the net positive suction head required (NPSHr) curve of the pump. This is a calculation of how much absolute pressure is needed at the inlet to keep the system from cavitating.
Second, calculate the NPSH available (NPSHa). This value represents the absolute pressure available at the pump inlet. If the NPSHa is 3 feet more than the NPSHr, the pump will not cavitate. Be aware, NPSHr is measured under ideal conditions for repeatability and accurate benchmarking. Pumps connected to a short radius elbow on the inlet are hardly ideal. When this type of poor inlet pipe is in place, up to 50% may need to be added to the declared value of NPSHr to be on the safe side.
How do I calculate NPSHa?
NPSHa is the sum of three values:
- The vertical static suction head. If the pump is on a suction lift, it will be a negative number.
- The friction loss on the inlet pipework. This is also a negative number.
- The temperature advantage, which is calculated using an equation where temperature advantage equals atmospheric pressure minus vapor pressure. Cold water in the system lends a temperature advantage that can help avoid cavitation. Hotter system water reduces this advantage.
In summary, Equation 1 shows:
NPSHa = +/- static head/lift – friction loss + temperature advantage
So, if there is enough static head available when pumping hot water, will the pump be OK?
If static pressure in the system is high enough, yes. When the pressure falls as the water interacts with the impeller, if the pressure level is still higher than the water vapor pressure, no gas bubbles will form.
And if there is not enough static head available, are we in trouble?
If the static pressure in the system is too low, when the pressure falls as the water interacts with the impeller, the pressure level will fall below the level at which water vaporizes. In this situation, bubbles will form and cavitation will occur.
The pressure level at which water will vaporize is an important aspect of cavitation because it changes based on the temperature of the water.
How is NPSHr measured?
Pump manufacturers measure NPSHr most often by using a closed-circuit test rig with a sealed water tank with an air blanket at the top and a vacuum pump connected to the top, ready to suck out the air. They operate the pump across a range of flow rates and, at each flow rate, start the vacuum pump and observe the inlet pressure falling on a compound gauge. They also closely look at the discharge pressure gauge. When the pump-generated pressure falls by 3%, the pump is cavitating according to the pump industry’s common standard and the inlet pressure—the NPSHr—is recorded.
As touched on earlier, to ensure repeatable results, the inlet pipe has to be 15 straight pipe diameters in length. However, this a rare sight in most pump installations. Hence, the safety margin. As a side note, the drop in pressure is the start of the process called “pumping on the break” where a cavitating pump will cease to generate any head. Pressure falls all the way to zero. The 3% is at the beginning of it cavitating.
What is ‘false’ cavitation?
This is a situation in which a pump sounds as if it is cavitating, but is not. Instead, the pump is having to deal with entrained air bubbles, which present no damage to the pump impeller.
Entrained air is a nuisance, but it is not actually cavitation. It happens most often on cooling tower applications when there is a vortex in the tower pond near the exit pipe, where the water leaves. The vortex can allow air to be sucked into the condenser cooling tower pump.
Is there hope for preventing the damage caused by cavitation?
Yes. In recent years, technology for tracking pump performance has evolved to the point that cavitation can be identified early, or even predicted so that issues can be addressed before substantial damage is caused.