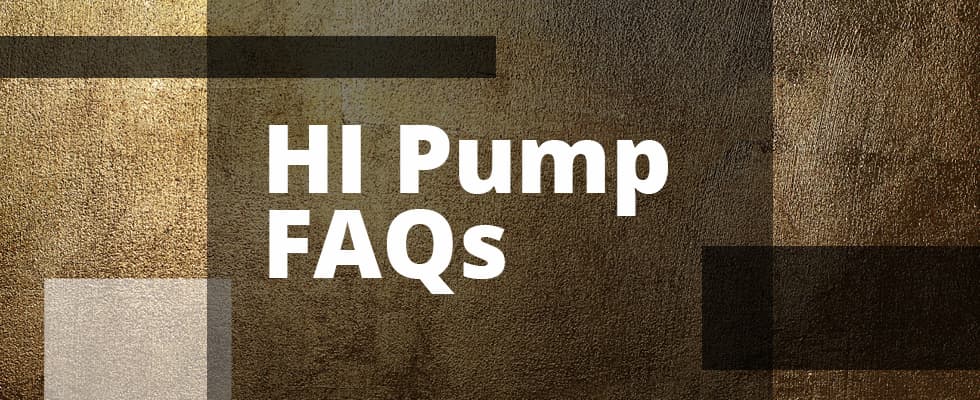
What factors affect pump efficiency?
Perhaps the most important factor is to select a pump that is properly sized for the normal system operating conditions, because off-design flow rate will result in lower operating efficiency. Assuming proper hydraulic selection, the first consideration is the type or design of the pump.
Focusing on rotodynamic pumps, there are many types with different configurations and features to meet specific service conditions—e.g., paper stock, sewage, slurries, etc.—all of which have compromises in design needed to address special applications. This will result in compromise efficiencies compared to clean liquid pumps (Image 1).
In addition to the design compromises made for specific applications, there are other items that will affect the attainable pump efficiency. For example, in vertical turbine diffuser-type pumps (due to hydraulic losses at the inlet and discharge of the pump), the number of stages will affect the attainable efficiency of the bowl assembly.
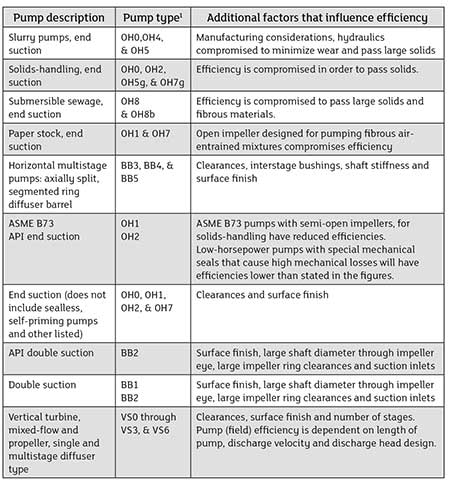
A single-stage attainable efficiency could be as much as six points below the bowl efficiency when four or more stages are used because the entrance and exit losses do not repeat with each stage. When reviewing a pump curve for this type of pump, it will likely include an efficiency derating for low stage counts.
An additional consideration for these types of pumps is that the overall efficiency will be less than the bowl assembly efficiency due to hydraulic losses in the column piping, discharge elbow losses and bearing losses. Because of the variability in this style pump, this correction needs to be analyzed for each application.
Pump type and design is only the beginning. Another consideration is the pump’s specific speed. Specific speed is an index for the pump design that relates to how the flow enters and exits the impeller. There is an optimal specific speed to reach maximum attainable efficiency that may vary depending on the pump design.
However, it may not be possible to select a pump at the “optimal specific speed” because the application will generally dictate the specific speed for the pump.
Pumps with a low specific speed discharge flow in a radial direction. Radial flow pumps (low specific speed) produce relatively higher head and lower flow rates. On the opposite end, pumps with higher specific speed, have flow enter and exit the impeller (propeller) in the same axial direction. Axial flow pumps (high specific speed) produce relatively higher flow rate and lower head.
Pumpage is also an important consideration. The viscosity of the pumped fluid will have a detrimental effect on efficiency for rotodynamic pumps.
For rotodynamic pumps, the performance as tested on water is corrected to the viscous performance using ANSI/HI 9.6.7 Rotodynamic Pumps–Guideline for Effects Liquid Viscosity on Performance. While this is not an exhaustive list, these considerations are important when estimating the efficiency of the pump.