
Motors are the most common source of power used by pumping systems. Knowing the condition of the motor and drive is important in any facility to maintain uptime and save money. Many testing instruments only provide measurements or alerts rather than answers to the condition of the motors. Motor circuit analysis (MCA) and electrical signature analysis (ESA) technologies help the health of motors and drives by answering questions that ease the burden of interpretation and expertise required when analyzing and interpreting other testing methods.
What Are MCA & ESA Technologies?
MCA is a deenergized low voltage test method to assess the health of the motor and associated cabling. This method can be initiated from the motor control center (MCC) or directly at the motor. The advantage to testing from the MCC is that the entire electrical portion of the motor system, including the connections and cables between the test point and the motor, will be evaluated. MCA is a motor testing method that identifies faults previously difficult or impossible to detect using the older techniques.
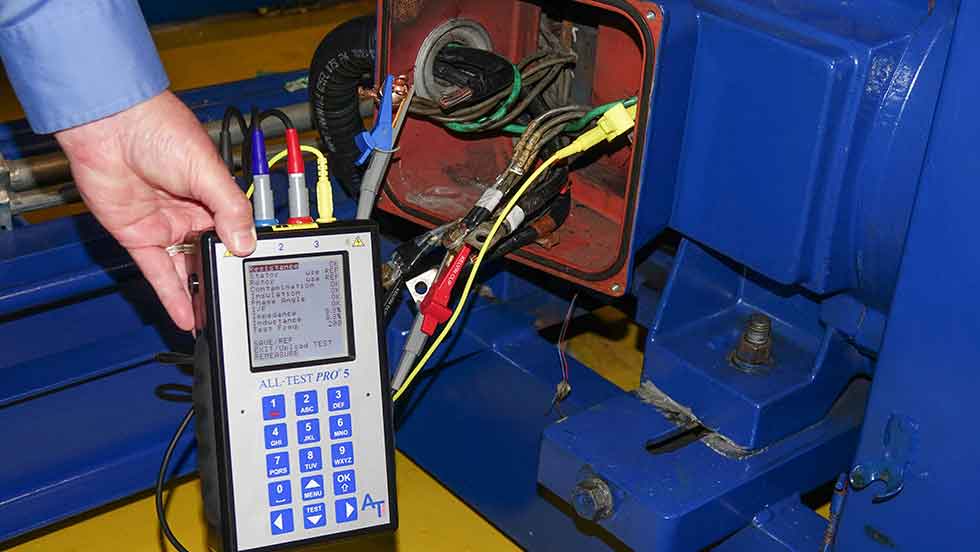
The condition of the ground wall insulation system fails to identify the condition of the winding insulation system or any of the various rotor faults. MCA can assess the health of the motor while the motor is deenergized. MCA can be used to determine the condition of the ground wall insulation and winding insulation, as well as identify squirrel cage rotor faults in induction motors and cabling to the control.
ESA uses both voltage and current to evaluate the entire motor system while the motor is energized. Incoming power quality detects faults in the grid, control or distribution center, operation and environment. ESA can quickly identify faults by capturing the time waveform of the motor’s voltage and current. The technology performs a fast Fourier transform (FFT) on these waveforms to identify mechanical faults that apply periodic loads on the motor—such as unbalance, misalignment, looseness, bearing defects, gear faults, vane or blade forces, process faults (i.e., cavitation), or hydraulic forces in fluid or air systems.
ESA can also find faults in the motor, such as static and dynamic eccentricity, or any fault in the squirrel cage rotor. ESA assesses the health of the motor system while operating. The recommended monitoring schedule varies between monthly up to annually, depending on how critical the motor is and the environment where the motors are operating.
MCA and ESA technologies complement other testing technologies. Vibration, infrared and ultrasound all alert potential problems. Use of MCA technology can help identify the source of the problems in the following equipment:
- alternating current (AC)/direct current (DC) motors regardless of size, poweror voltage
- AC/DC traction motors
- generators/alternators
- machine tool motors
- servo motors
- control transformers
- transmission and distribution transformers
- machine tool motors
- gearboxes
- pumps and fans
- belted systems
Benefits of MCA
MCA technology is used for incoming and outgoing inspection of new, repaired motors (motor tags), condition monitoring, preventative maintenance, predictive maintenance (trending asset life) in a safe and quick manner. MCA can quickly detect cable degradation, pitted/eroded contacts, loose connections, developing winding faults, ground faults, winding contamination and rotor faults. Another benefit of MCA is test value static (TVS) that tracks the motor asset from the cradle to the grave. TVS monitors changes in the motor baseline that alert potential motor failure and associated developing problems.
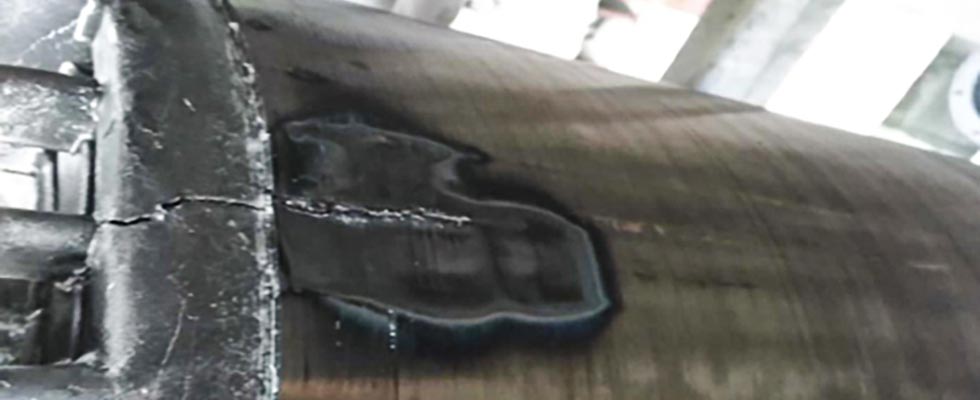
Benefits of ESA
ESA technology quickly detects mechanical issues such as stator and rotor issues (eccentric, casting voids, cracked or broken bars), balance (bent or cracked shafts and bearings) and alignment (belts, fan and pump). ESA includes power quality and can be used for energy data logging, harmonic analysis, voltage and current charting, viewing waveforms, waveform capture of sags and swells, transient capture and event capture while the motor is operating. Additional benefits include motor efficiency, commissioning, troubleshooting and predictive trending and analysis.
Costs increase when motors have a catastrophic failure, which results in more replacement parts, production losses and wasted time troubleshooting. Although the cost is low to maintain a motor in a run to fail scenario, the cost increases when the motor fails as compared to a moderate approach to maintenance and routine testing. ESA and MCA technologies can help identify bad motors and good motors. Both technologies are nondestructive test methods that do not stress the motor with additional voltage that could deteriorate insulation, possibly causing an end of life situation on an operating asset.