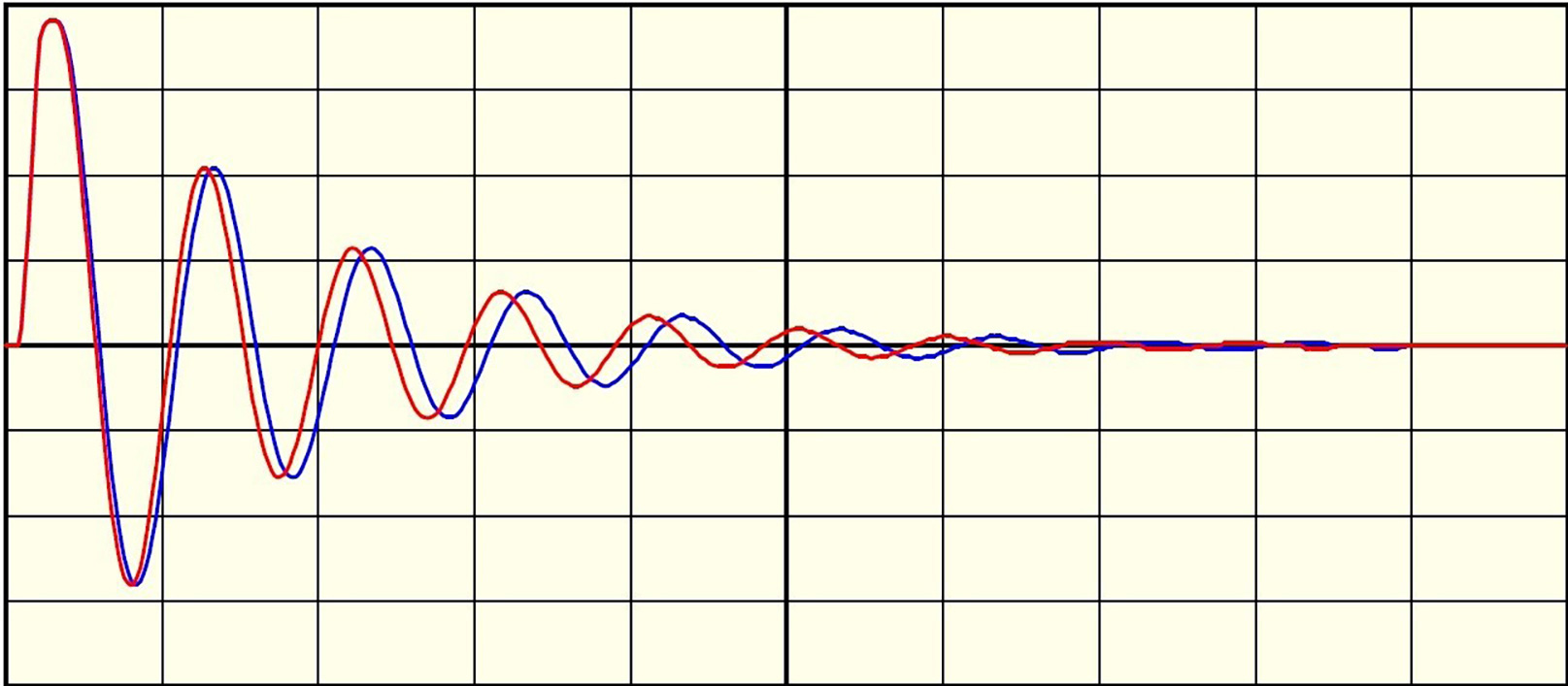
The surge comparison test is an essential test for motor maintenance and reliability professionals in the pumps and controls industry. Most maintenance programs are already using digital multimeters and megohmmeters. They conduct low and medium voltage tests such as the megohm test (sometimes called a megger test), winding resistance and others. This article goes into depth explaining what a surge test is and how it can find faults these other tests cannot.
Why Is the Surge Test Important?
The surge test is the only test that finds turn-to-turn insulation weaknesses in motor windings. These weaknesses cannot be found with insulation resistance/megohm, low-voltage measurements or high-voltage high-potential (hipot) tests. The surge test stresses the motor-winding’s turn-to-turn insulation at a voltage above operating voltage so that both weaknesses and hard shorts can be found.
Surge test results are valuable data for predictive maintenance professionals. Pass/fail determinations are easy to make in most cases so data-driven decisions can be clearly defined for the type of motors in use. If weaknesses are found above operating voltage, in most cases the motor can continue to run while remedial actions are scheduled.
Typical Motor Failure Progression
A motor can progress to failure in many ways. A typical progression starts as turn-to-turn insulation weakness in the windings. Most winding failures, including shorts to ground, start with weak turn-to-turn insulation.
Partial discharges (PD) are the first evidence of weakness that can be detected in the windings. The presence of PD may not indicate a problem in medium- and high-voltage motors but is a problem in low voltage motors. See a previous article on PD testing from the March 2022 issue of Pumps & Systems.
If insulation continues to weaken, a surge test is the best test for detecting weakness early. A failure above peak operating voltage is a precursor to complete motor failure. The motor can continue to run for a while leaving time to plan a course of action.
Once the weakness causes turn-to-turn arcs, heat creates a hot spot. The hot spot causes more turns to short out and subsequently more heat is created. Eventually the winding shorts to ground.
How Does the Surge Test Work?
A high rise-time pulse is repeatedly sent through the winding by circuitry in the test instrument. The result is a decaying oscillating wave for each pulse, displayed on a screen by an oscilloscope circuit. The number of oscillations of the wave depends on the Q factor of the motor (impedance components)—how much the surge wave is dampened by the motor winding circuit. The rotor and the construction of the motor determine the level of dampening. The frequency of the waveform is inversely proportional to the number of turns. Therefore, a winding with fewer turns will produce a higher frequency wave and vice versa, with everything else being equal.
The surge tester increases the voltage of each pulse and compares the resulting surge waves by calculating a percent wave difference. If the motor loses a turn because of an arc or short, the frequency of the waveform increases. On the test screen, this appears as if the wave suddenly shifts to the left. When this happens, the difference between waves increases. The difference is calculated by the tester as a percentage.
Surge waves are compared in two ways: phase-to-phase and pulse-to-pulse. A phase-to-phase comparison in a three-phase motor compares phase 1 to 2, then 2 to 3 and then 3 to 1. In a pulse-to-pulse comparison, each phase is tested against itself. As the surge voltage is gradually increased, the surge tester compares each new waveform to the previous one.
How Are Results Calculated?
The general approach is to calculate the difference between many points along a wave pair (y-axis points on the two waves with the same x-axis position), add up all the y-axis differences and divide by an average. If the difference is above the operator’s pass/fail threshold, the surge test is considered failed. Keep in mind that the tester does not fail the motor, it only fails the test. The operator determines what action to take as a result since it may be possible that the motor can continue to run.
The Surge Test Is Not Destructive
The surge test is not destructive because the energy in each surge pulse is low and the duration of the over-voltage is short. A good analogy is a static electric discharge arcing from your finger to a doorknob. You may be able to feel it but there is no burn mark or damage.
Motors are designed to handle voltages far above normal surge test voltages. For example, it is not uncommon to see 460-volt (V) motors arc around 10,000 V. Even old motors have been seen to arc around 8,000 V. Compare that to normal surge test voltage for 460 V motors of around 2,000 V. Furthermore, motors and coils in laboratory settings have been surge tested many times with no discernable change in the insulation properties.
For old and brittle insulation, carbon tracking in cracks in the insulation will lower the insulation’s ability to withstand certain voltages. Maintenance professionals should consider reducing the surge test voltage for such motors. The bottom line is, if there is an arc, the motor insulation is bad and the motor either already has problems or will develop problems soon.
Surge tests are critical because they are the only tests that find turn-to-turn insulation weaknesses. These weaknesses are precursors to serious failures and shutdown of a motor. Surge tests provide data that is also used to find hard shorts and several other mistakes in windings and coils.
The surge test generates a surge pulse in a motor’s windings, which results in a decaying oscillating waveform. The test instrument calculates the difference in waveforms either phase-to-phase or pulse-to-pulse. If the difference is above the operator’s pass/fail threshold, the motor has weak winding insulation.
The surge test is important for predictive maintenance professionals because it can find cases of weak insulation before the motor progresses to complete failure.
This allows maintenance programs to schedule maintenance rather than risk unplanned downtime.
What Motor Problems Can a Surge Test Find?
%20(1).jpg)
- phase-to-phase weaknesses and shorts (1)
- turn-to-turn weaknesses and shorts (2)
- coil-to-coil weaknesses and shorts (3)
Not pictured in Image 2:
- wrong turn count
- wrong coil connections internally
- weaknesses to ground (in some cases only and not as well as a hipot test)