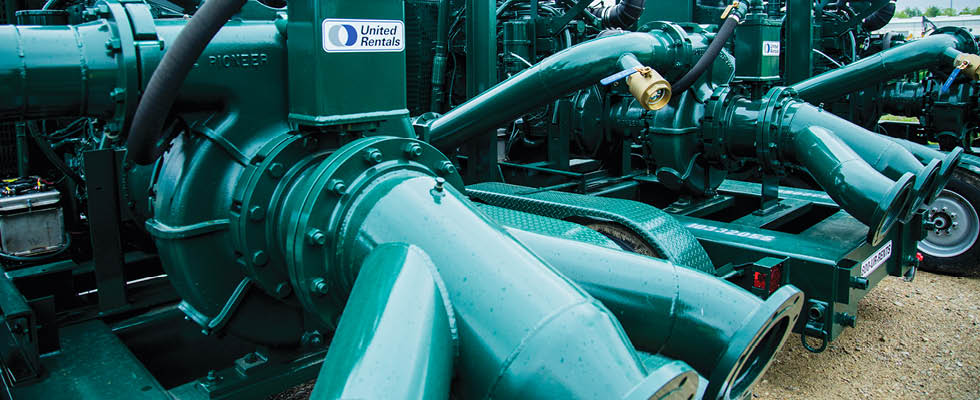
Choosing the right pump is essential to successfully transferring fluids on a worksite. Standard centrifugal pumps, also called trash pumps, handle many tasks, but installing one when more pressure is needed can result in breakdowns, project delays and cost overruns. A high-head pump is often the optimal solution when pushing a liquid uphill or over a significant distance. Understanding when to use a high-head pump can keep fluids and projects moving smoothly.
Factoring Resistance Into Pump Selection
A high-head pump is designed to deliver the extra pressure required to keep a fluid moving when it meets high resistance in the pumping system. High resistance typically results from one of two factors: elevation gains or friction losses that occur when pumping over long distances.
When the ingress point of the pump is significantly lower than the egress point, additional pressure is needed to overcome gravitational forces. A high-head pump may be required when pumping fluid over hills or into a tank, for example.
When fluids are moved over long distances, more pressure is needed to account for the additional loss in energy caused by friction, known as friction loss. Friction loss occurs when the fluid rubs against the walls of the pipe or hose. The longer the distance, the more friction loss.
To overcome resistance from elevation gains or friction loss, high-head pumps are generally designed with larger impellers than trash pumps and impeller blades that are shaped to maximize pressure. They may also have more horsepower than a comparably sized trash pump. These factors combine to provide more pressure for applications with a high total dynamic head (TDH).
A Question of Pressure vs. Volume
When determining the type of pump a project requires, it is important to remember the relationship between pressure and volume. It may seem like the extra pressure provided by a high-head pump would move fluid through the system at a higher flow rate (gallons per minute), but that is not the case. In fact, when the pressure exerted on the fluid is increased, the flow rate decreases.
The flow of water through a garden hose illustrates this principle. A hose that is completely open at the end delivers the maximum volume of water, but that water travels only a short distance. If the end of a hose is partially covered with a thumb or nozzle, the volume of water exiting the hose will decrease, but the pressure behind the obstruction will make the water travel further.
High-Head Pump Applications
High-head pumps are used in a variety of industries and settings, including:
- Construction sites: High-head pumps may be needed when dewatering an excavation or deep hole.
- Oil and gas: This industry commonly utilizes high-head pumps to move fluids involved in the drilling and extraction process of these energy resources—particularly in areas with high elevation changes.
- Industrial plants: Chemical plants may use high-head pumps to move liquids between process stages. The pumps are also used in fire suppression systems since they are capable of pushing water or other fire retardant fluids through the maze of piping found in these plants.
- Data centers: Contractors that build data centers employ high-head pumps to flush pipes once construction is completed, or to test the integrity of cooling tower piping.
Limitations of High-Head Pumps
Every type of pump comes with tradeoffs. Unlike trash pumps, most high-head pumps are not designed to allow solids to pass and are therefore better for moving relatively clean fluids.
In addition, high-head pumps must be used only in pumping systems designed to handle the extra pressure. It can be tempting to use a high-head pump that has performed well at one task for another application where extra pressure
is not needed, but that is a mistake. Installing a high-head pump rated for 150 pounds per square inch (psi) in a system that utilizes hoses, clamps and other fixtures rated for 20 to 50 psi can damage the pump and may even result in a pipe or hose explosion that harms workers and causes damage to the site.
Making A Pump Selection
Calculating the TDH is essential to choosing a pump and determining if a high-head pump is needed, but many additional factors should be taken into consideration as well. These include:
- the type of liquid being moved, including the percentage of solids
- the required flow rate and suction lift
- the distance to the discharge point
- the project elevation (higher elevations have thinner atmospheres, which require more powerful pumps)
- the temperature of the liquid
Even project managers with a good understanding of pump basics can lack the expertise or bandwidth to choose among the many pump models available.
One way to get the best, most cost-efficient pump system for the application is to consult an equipment rental provider that offers a large and readily available inventory of pump types and sizes and a team of knowledgeable and experienced pump experts, including in-house engineers who can perform pump calculations. The more questions the vendor asks about the site conditions and the fluid being moved, the better the chances the pump they recommend will get the job done efficiently and effectively. Working with a vendor that has service technicians on call 24/7 can
also further minimize or eliminate pump-related downtime.
Accounting for high levels of resistance and choosing a pump accordingly when transferring fluids can save time, money and reputations.