End users in need of replacement parts should understand the capabilities and offerings of different suppliers to obtain optimal system components.
06/07/2016
The aftermarket business continues to be in a state of flux. For many years, pump users and original equipment manufacturers (OEMs) have referred to non-OEM parts as pirate or replicator parts. Recently, several companies have evolved into a new category of solution providers. Parts supplied by these companies go beyond simple parts replacement. A solution provider focuses on the total cost of ownership to provide quality parts using state-of-the-art manufacturing. These companies engineer upgrades that improve runtime and use dedicated or job-shop manufacturing processes to provide quick deliveries.
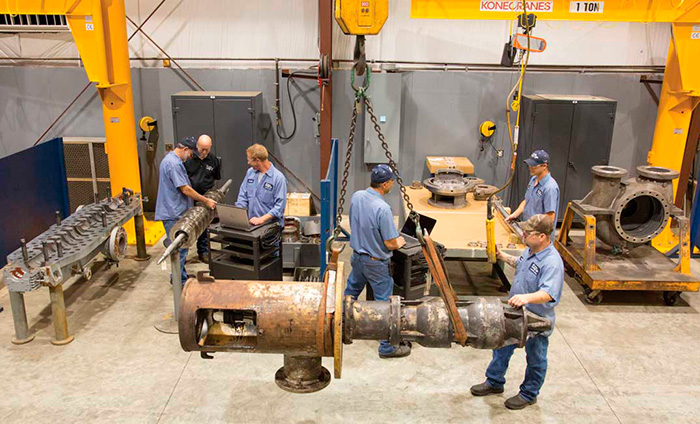
Pirates & Replicators
While many users would prefer to purchase from the OEM, they often look for alternate sources for their parts because some OEMs may lack the flexibility to meet delivery requirements or because the OEM has closed. For this reason, pirate and replicator companies have existed for decades. The process of finding and selecting an alternate source has become more complicated with the advent of new portable coordinate measurement machines (PCMM). Just because a parts supplier uses these devices does not mean it will be able to provide an optimal part; a quality parts supplier does more than purchase equipment. PCMM machines are highly accurate devices that take thousands of measurement points or scan complete surfaces to measure a part's physical characteristics. The supplier must have the technical ability to analyze the data collected. Even if the part being copied is a new part, it is likely to have some manufacturing deviations that can hinder the performance of the part being supplied. The OEM can clearly evaluate and even categorize these deviations for disposition and use, but a pirate cannot. Subsequent deviations can occur that prevent the pump from meeting the original operating conditions, and this problem could worsen if the pirate is working with a worn sample. The part will simply be a brand-new, worn-out part. Replicators take the process one step further: They reverse engineer the part. This means they evaluate the data collected using the PCMM based on their understanding of pump design. They rationalize the data and have the technical expertise to identify manufacturing deviations, in-service part wear and manufacturing flaws. From there, they reverse engineer a product that meets the original fit, form and function. Assuming the replicator has the in-house expertise to rationalize the data as described, the parts supplied will work and often be adequate to restore the original operating performance.Solution Providers
Albert Einstein has been quoted as saying, "The definition of insanity is doing the same thing over and over and expecting different results." Based on the discussion above, a pirate may produce an unfavorable result, which can jeopardize the pump's operation. A replicator can produce the desired results but typically does not optimize performance of the part. In other words, if a user had poor design performance and reliability before the part is replaced and the supplier or replicator simply provides the same part again and again, the user cannot expect the pump's performance and reliability to become acceptable. Solution providers do not simply repair or replace parts; they offer value-added engineering from hydraulic and mechanical design, metallurgical expertise and manufacturing know-how. They partner with the end user to look at the total pump system and offer solutions with tangible reliability improvements and measureable cost savings. Solution providers have become even more critical in today's global energy-conscious environment. Plant operations and maintenance personnel are pressed to minimize their plants' carbon footprints while increasing profitability. This is difficult to do when many pumps in service today are operating off their design point because they were not properly sized during the design phase or because the operating conditions have changed since startup.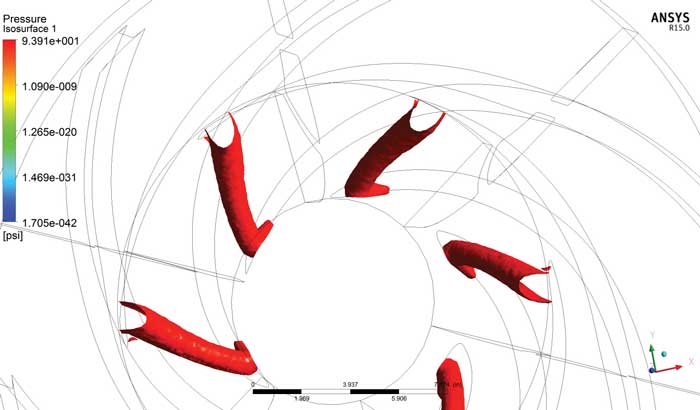
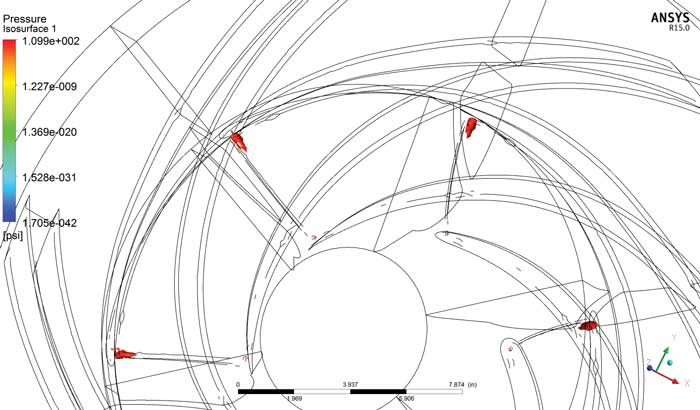
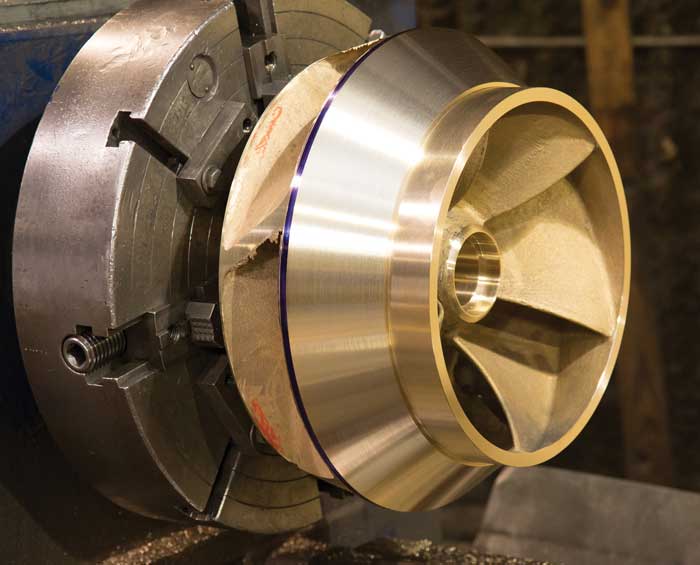