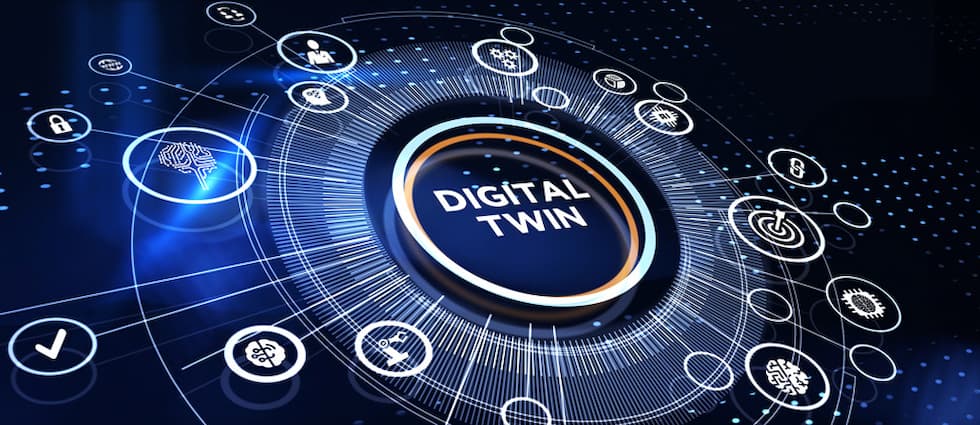
As technology advances, it seems the latest buzzword is industry 4.0. This is closely followed by digital twin. For those that are yet to get to grips with the meaning of both (and that is many), first demystify the former.
Industry 4.0 refers to the fourth industrial revolution. What this means is the transformation of traditional manufacturing and industrial processes into those that are automated. This is being buoyed through the dramatic increase in smart technology, also referred to as the internet of things (IoT).
Understanding the Digital Twin
In a nutshell, a digital twin is a virtual modeling program that simulates a physical object or process throughout its entire life cycle. All scenarios can be programmed to determine the effects. It also allows the user remote monitoring and control.
A digital twin can be created to mirror most applications, be it a system, single asset or a complex combination of linked equipment. By running various scenarios and ‘what if’ occurrences, companies can discover innovative ways to increase performance. Conversely, this also provides a solid way to test a high-risk process without the danger of a catastrophic result.
A digital twin can be as simple or sophisticated as a user chooses. It can represent a single element or multiple and complex cases. To create such a model requires sensors, a communication network and an advanced digital platform.
Three Major Applications for A Digital Twin & the Benefits They Bring
The Industry 4.0 landscape is something never-yet experienced by the human race. To complement this, the concept of the digital twin was first seen in the aerospace industry. Today, there is not a field untouched by the advancement of technology. It is this that makes the use of a digital twin such a powerful tool.
The following are three of the most advantageous reasons for using digital twin technology.
1. Prototypes and product design:
The creation of virtual models and prototypes provides a unique insight into workload capacities, constraints, breaking points, characteristics and failures. This is equally applicable to a physical asset as to a system. The benefits of running robust simulations on virtual prototypes before moving into production are many—both from an economic and safety point of view.
2. Maintenance and safety:
The ability to predict wear, tear and failure of assets allows for true proactive maintenance. Examples include assets within the oil and gas or petrochemical industry where, historically, maintenance has often been reactive following manual inspection.
3. Process planning:
Inefficiencies and losses during any industrial process are costly. Determining what these are and where they occur allows organizations to optimize output, increase yield and reduce wastage. In fields where downtime has a negative impact on production (petrochemical, oil and gas, nuclear, etc.), accurately forecasting and planning the down periods can make all the difference in the provision of these costly operations.
Considerations
As with any new technology, there are various aspects to consider before jumping in. First and foremost is confirming that adequate technology is in place to feed the necessary data. This needs to be collated, analyzed, verified, structured and high-enough quality to provide the digital twin with the necessary information to accurately perform its task. Connectivity is key, and consideration should be given to the quality of an existing communication infrastructure before beginning such a project.
A digital twin is not a stand-alone concept. It is a dynamic commodity—ever-improving thanks to continuous analysis of real-time data. For most organizations, this will see an initial digital twin application evolving through time, perhaps starting as a single entity before being combined into an ever-more complex process over time.