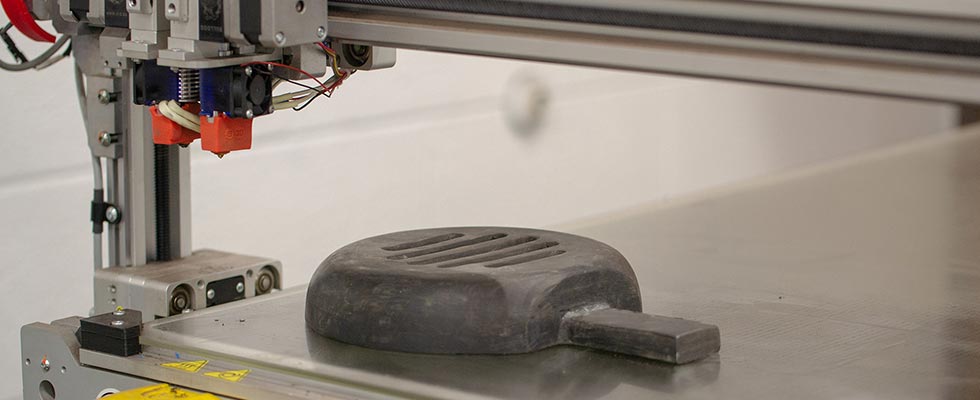
Some think technology is eliminating skilled positions, when in fact it is mostly used to bridge the gap and create new positions. Technology has advanced, and it is not just the tech industries that are using it.
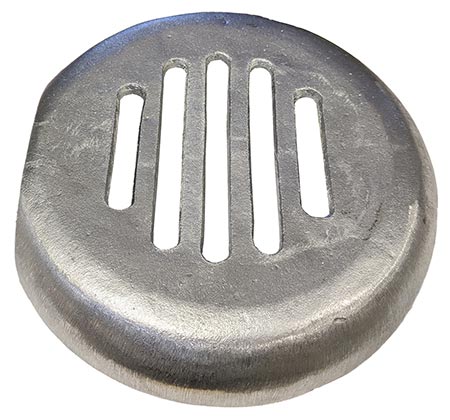
Industrial applications have become more involved in technology in recent years as technology has become more cost-effective and more vital to industries of all kinds. The introduction and progression of 3D printing has caught the eyes of many industrial company leaders, begging the question of how 3D printing can be implemented into manufacturing techniques to improve efficiencies.
While this technology is not practical for all industrial environments, 3D printing and prototyping can be particularly useful in the recreation of obsolete parts or the creation of small-batch castings through foundry mold applications—specifically the patternmaking process.
To understand where 3D printing would be applicable, users must first have some knowledge of the foundry mold process. These foundry processes and metal castings are dying art forms, but if a user is fortunate enough to have one in his or her building or on their supplier list, the possibilities are endless.
One of the most critical elements of the process is having an accurate and functional pattern to create or recreate a part. There are a variety of foundry processes, but for the purposes of this example, this article will focus on small-batch, hand-molded sand castings.
The mold-making process begins with a drawing that is used to create a pattern out of a material strong enough to leave a clean imprint in the sand. The pattern is then removed and once the metal is poured, it fills the void left by the pattern, then the part hardens and cools.
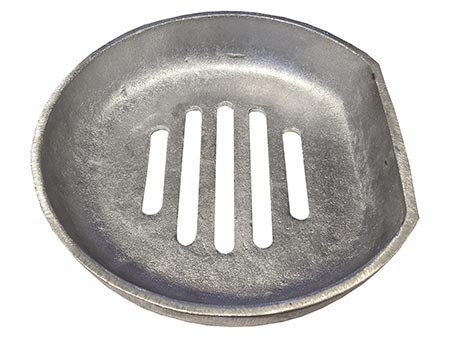
Once the sand is broken away from the part, the newly created or formerly obsolete part is then finished and machined as specified by the customer or manufacturer.
When making a pattern using a 3D printer, the goal is similar to that of traditional patternmaking: create a pattern that has a smooth surface, yet rigid enough to leave a clean imprint while withstanding the pressure needed to create a quality mold. Traditional patternmaking relies on years of experience and finesse performed by hand using trade skills of metal forming and welding that can be time-consuming, while 3D printing requires software knowledge and an aptitude for technology.
One aftermarket parts company has fabricated custom fan covers using 14-gauge, cold-rolled steel—an individual, by-hand process that is not ideal for large batch orders. When this company was recently faced with producing hundreds of fan covers, the opportunity to use 3D-printing technology in combination with a skilled foundry team presented itself.
The first hurdle in the process was to test if the custom fan covers would be a practical choice for 3D printing. In early attempts, a few challenges arose as the printed material warped and bent as it cooled, causing the pattern to be out of tolerance. The team was able to correct this by creating supports to combat warping during printing. After printing, the team was able to smooth the surface of the pattern, preparing it for the molding and casting stages of the foundry process.
The process of using the foundry in combination with 3D prototyping proved to be timelier than traditional custom fan cover fabrication processes, cutting the manufacturing process from months to weeks.
While working out the kinks of a 3D pattern takes time and small adjustments, it can prove valuable if the finished pattern can be used to create multiples of the finished part.
3D printing continues to grow in popularity around the world for its uses in commercial applications. Under the right circumstances, 3D printing pairs perfectly with the benefits of a small-batch custom foundry, especially when used to create newly designed parts as well as obsolete, high-quantity parts.
As materials and technology advance for 3D printers, the likelihood of implementing 3D printing as a standard, cost-effective way of patternmaking in foundry settings may develop over time.
As of now, 3D printing can serve customers and manufacturers by providing the ability to recreate formerly difficult to find, obsolete or labor-intensive parts, as well as for potential prototyping of parts for fit, form and function.