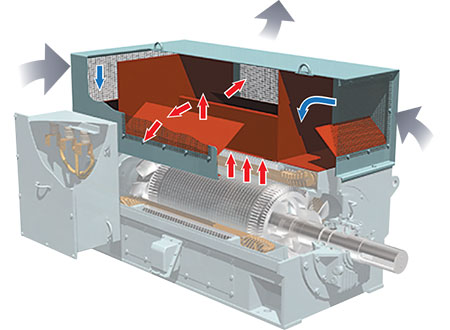
Electric motors are considered one of the main components of large pump systems due to their percentage of the total system cost and their role in the entire pump system’s reliability. When pump OEMs specify motors for a request for quotation (RFQ), specifications such as the rated power, rated voltage/frequency and each application’s speed range are generally clearly indicated. However, additional critical issues arise when choosing the appropriate motor enclosure.
First, the enclosure protects the motor windings, a critical component, from harmful contaminants in the outside environment like water, dust and high temperature while efficiently cooling and reducing motor noise. It also protects personnel from heat and high noise generated by the motor. The enclosure is one of the main factors in determining motor frame size, which may impact the motor cost and the pump system design.
Most users select motor enclosure types without considering the surrounding environments or ambient conditions and with little understanding of each enclosure type’s advantages or disadvantages. Proper selection of motor enclosures will benefit users with lower cost, higher reliability and improved efficiency. In contrast, improper choices can cause frequent downtimes, increased motor repairs and additional and often nonbudgeted maintenance costs.
When it comes to motor enclosures, there are many options. National Electrical Manufacturers Association (NEMA) standard MG1-2016 defines several different types of common motor enclosures but most of them are cast frames for small motors with limited rated power. This article will review four major enclosure options (ODP, WPII, TEWAC and TEAAC) for large- and medium-size electric motors (3,000 horsepower [hp] or larger) and a guide for selecting proper motor enclosure types while considering cooling methods, pros/cons, motor size, cost, reliability and site environments.
Here are the essential things to consider when choosing enclosure types for large- and medium-size motors.
Enclosure Types
1 - ODP (Open Drip Proof, IC01, IP12)
Cooling method: The surrounding outside air is drawn into the motor top-mounted enclosure to cool the whole motor body, including rotor and stator windings. Motor cooling is achieved by rotating interior fan blades radially installed on the shaft end(s), creating a slight pressure difference between the rotating blades’ two sides, pulling cooler outside air into the motor housing.
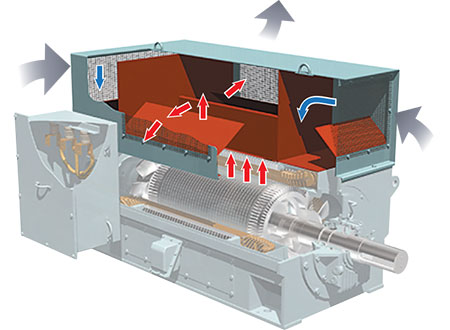
The air intake side of the fan blades is exposed to the outside air through the enclosure’s embedded channels. The discharge side of the fan blades forces fresh air into the motor. Main parts of the motor’s internal structure like rotor, stator and windings are exposed to cooling air. The moving air absorbs the generated heat and is directed to the discharge channel.
Image 1 shows the path of the cooling air. The air intake path (blue arrows) is drawn from the outside, and after absorbing the heat from internal parts (red arrows), it is directed to the outside channels and leaves the motor. The volume of the air that enters the motor depends on motor speed and fan blade design.
Alternatively, an independent external blower motor could be mounted on the main motor enclosure to fulfill the cooling air circulation requirement. This type is protected against dripping water that may have up to a 15-degree angle from the vertical line and will not enter the motor.
Advantages: ODP enclosures are considered the least expensive, simplest structures among top-hat-type enclosures. Stators and rotor windings are cooled by outside air, keeping the frame size relatively small.
Disadvantages: The open enclosure design results in a high noise level compared to other enclosure types. It is also difficult to apply noise abatement techniques because the noise from the internal shaft-mounted fans reaches the outside. This type is not applicable for Division 1 hazardous areas.
Possible problems and solutions: If an air filter is not installed, insects and rodents can easily enter the motor enclosure through air openings and block the airflow. Air filters could become clogged by dust or particles. Thus, air filters and differential pressure instruments are recommended. Due to exposure to the surrounding air, the internal parts are at risk of rusting and corrosion. Proper primary painting is recommended, especially for the stator and rotor and internal frame.
Recommendations: Recommend ODP for clean and well-ventilated indoor areas only. Not suitable for outdoor or corrosive/dust areas.
2 - WPII (Weather Protected Type II, IC01, IP23/24)
Cooling method: The cooling method is similar to ODP. However, WP II offers better protection against external dust, water and objects. Baffles on the top-hat enclosure’s air-inlet side force fresh air to change direction while moving from inside to outside. The airflow pathway encounters three 90-degree turns, reducing the opportunity for water droplets and dust to enter the motor.
Advantages: The WPII enclosure is designed for outdoor use. However, it is also suitable in a well-ventilated indoor location. The footprint is relatively small, and the structure is simple, like ODP. The cost is slightly higher than an ODP enclosure but still less expensive than other totally enclosed types.
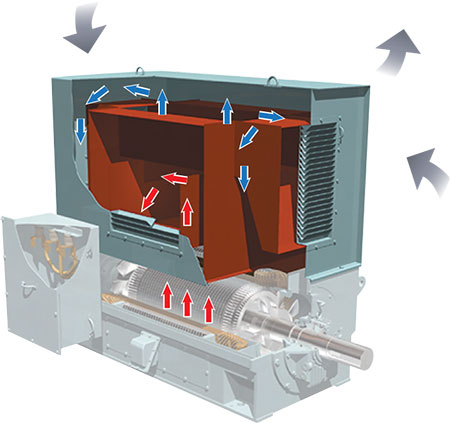
Disadvantages: Like an ODP enclosure, the high noise can be an issue. If used in a dusty area, the filter can clog easily, causing the motor to trip. This type is not applicable for Division 1 areas.
Possible problems and solutions: Air filters could become clogged by dust or particles. Thus, air filters and differential pressure instruments are recommended. Due to exposure to the surrounding air, the internal parts are at risk of rusting and corrosion. Proper primary painting is recommended, especially for the stator and rotor and internal frame.
Recommendations: A WPII enclosure is suitable for use in relatively clean and less-dusty outdoor areas. Also, it could be a reasonable substitute when cooling water is not available at the site. Please note that a stainless steel washable air filter (90% of particles ≥ 10 microns) is recommended for this enclosure, and regular maintenance, cleaning or filter replacement is necessary.
3 - TEWAC (Totally Enclosed Water to Air Cooled, IC81W, IP54/56)
Cooling method: A TEWAC enclosure uses the high heat absorption property of liquids for motor cooling. In this type of enclosure, the internal circulating hot air passes through dedicated air pathways designed and embedded in the heat exchanger. The heat exchanger is mounted on the motor body and has channels and tubes where liquid can pass through without leaking into the motor body. On the other side, the cooling fluid such as freshwater or a glycol mixture flows through heat exchanger tubes to remove heat from hot air that is continuously circulating inside the motor. To effectively design the motor and its TEWAC cooling system, the end users need to provide essential data regarding the proposed cooling liquid’s quality to be deployed in the cooling system and heat exchanger. This enables manufacturers to offer the best economic and engineered solution. Information regarding maximum inlet liquid/water temperature and liquid/water type are required.
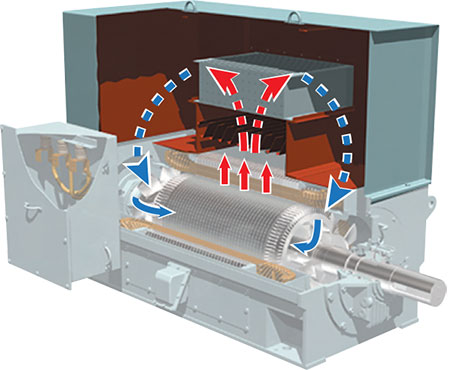
Advantages: This type of enclosure has the best cooling efficiency and lowest noise compared with other types of enclosures. Noise reduction is easy to apply, and large-capacity motors up to 30 megawatts (MW) for induction motors and up to 100 MW synchronous motors are available. A TEWAC configuration is considered the most reliable option and suitable for use in dusty/dirty areas, indoor/outdoor and Division 1/Division 2 hazardous areas if properly designed.
Disadvantages: Capex/opex cost is the highest among top-hat-type enclosures. Cooling water is always required for a TEWAC enclosure. A closed-loop cooling system is an option when fresh cooling water is not available; however, the additional cost adds up and cooling efficiency can drop. Users should have a water cooling system that maintains the quality and inlet temperature of the
cooling water.
Possible problems and solutions: Water leakage is a potential problem, so a water leakage detector is recommended. A double tube heat exchanger or redundant cooler is an available option to increase reliability.
Recommendations: A TEWAC design is the best option for large motors when the maximum ambient temperature is high and cooling water is available. It is best for use in a corrosive and dusty area and is suitable for Division 1/Division 2 hazardous areas when properly designed.
4 - TEAAC (Totally Enclosed Air to Air Cooled, IC611, IP54/56)
Cooling method: A TEAAC enclosure is equipped with an external fan that blows surrounding ambient air into the motor frame’s heat exchanger tubes. The motor heat exchanger is designed to efficiently transfer internal motor heat to the surrounding air.
Internal motor sealed forced air is circulated by internal fan(s) blades mounted on shaft end(s). If the rotor is rotating, shaft-mounted blades are also turning. This causes internal motor-sealed hot air to continuously circulate and pass through heat exchanger tubes. The volume of sealed air circulated internally directly corresponds to the motor rotor’s speed.
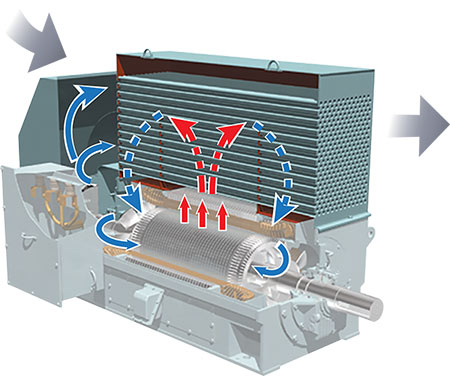
The rotor’s higher speed results in a higher chance of exposure of internal hot air to the heat exchanger. Heat exchanger tubes play a key role in efficiently transferring heat from motor internal hot air to external air.
This enclosure type is expensive and is not suitable for an extremely large-capacity motor since the windings are not well cooled, particularly if the motor is operating in a variable and low-speed application for a long period of time. In that case, the chance of overheating exists, which could damage the motor’s insulation and reduce the motor’s operating life.
Advantages: A TEAAC enclosure does not require cooling water at the site. As the frame is totally enclosed, this option is suitable for dusty /corrosive/humid/salty areas. The noise abatement technique is easy to apply.
Disadvantages: This enclosure’s frame size is usually one or two sizes larger than TEWAC or WPII when the other specs are the same. The initial cost is the highest, and there is some limit in the rated power range. Noise level is higher than a TEWAC.
Possible problems and solutions: When the noise level is too high, a noise absorber is highly recommended, especially for large high-speed motors. Windings are not well-cooled for large motors, so one or two external blowers are needed for better cooling.
Recommendations: A TEAAC enclosure is recommended when the maximum ambient temperature is not high and cooling water is not available at the site. A TEAAC is a good fit for on/offshore applications. It is not recommended for use in an extremely high ambient temperature and cooling water is available.
When choosing the best enclosure type, there are many things to consider in selecting proper motor enclosures. The factors to be investigated are based on users’ needs or site conditions such as environmental circumstances, hazardous environment requirements, water availability, etc.
It can be challenging to determine what type of motor enclosure is the best for the driven equipment. Therefore, understanding the basic concepts, pros, cons and recommendations of each enclosure type will help users select the most efficient and cost-effective enclosure for pump systems.
Getting familiar with motor standards such as NEMA MG-1, International Electrotechnical Commission (IEC) and American Petroleum Institute (API) 541/547 is a good starting point to learn about basic motor requirements, including enclosure types and cooling methods.
Another good practice is to consult with motor experts to receive professional advice and recommendations. By selecting the best enclosure type, the motor is more likely to achieve the designed motor life cycle and simultaneously increase motor performance and reliability.
References
NEMA MG-1 2016
TMEIC MV Induction Motors 21-L Series Catalog_2012