Modern pumping systems typically include alarms that alert operators when a malfunction occurs. However, by practicing predictive maintenance, potential problems can be caught before they become major issues. Integrate a remote monitoring system with the right sensors and data logging functionality to prevent high-level equipment failure, extend pump life and minimize station downtime.
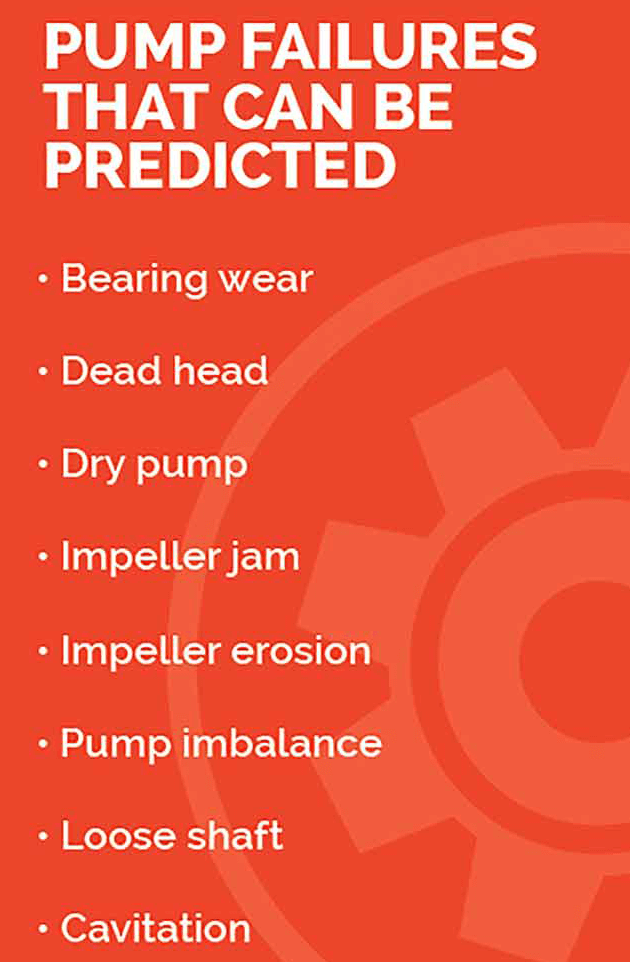
Advantages of Remote Monitoring
Managing a stormwater or sewer pump station can be challenging. Unexpected events such as fast-moving storms, heavy rains, lightning and power outages are unpredictable. During these times, an unexpected pump failure can make it difficult to take fast enough action to avoid a spill. Remote monitoring of pumping stations provides operators with real-time alerts on failures, which maximizes pumps’ best efficiency points (BEP) and reduces overflows and spills. (See the sidebar at the end of this article: Types of Vibration)
Monitoring systems also safeguard from costs associated with fines from overflow and flooded wells, cleanup and downtime. If a pump fails, the callout system immediately sends an alert, so personnel can diagnose the pump failure and take corrective action to get the well back online before a spill occurs. In addition, having a remote monitoring system reduces maintenance and travel costs because it prevents the need to regularly drive to remote sites to check if pumps are functioning properly.
Predicting Equipment Failures
In theory, a well-designed pumping system should continue performing effectively for years. However, the reality is that many different operating conditions can cut a system’s life short.
A pump laboring under the handicap of a clogged intake, suction loss or cavitation stresses parts of the system and can cause it to fail prematurely. Bearing wear, dead head, dry pump and impeller jams can all cause premature motor and pump failure, which can lead to overflows and station shutdown. Using sensors and data logging are keys to performing predictive maintenance, preventing unscheduled shutdowns and optimizing the pumps’ BEP. Here are five ways to get more out of the pumps and water/wastewater equipment by using sensors and remote monitoring technology.
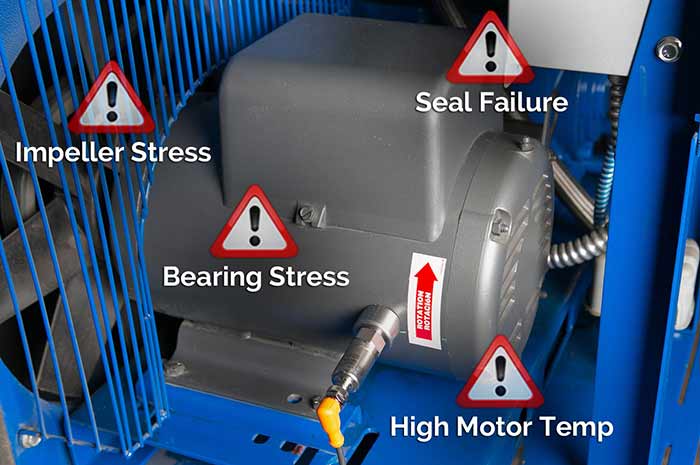
1. Monitor Vibration
Fortunately, critical and auxiliary pumping systems usually give hints they are damaged and about to fail. Every rotating machine has its own vibration characteristics, and when a part starts going bad, those characteristics change.
If the seals or bearings on a pump begin to fail or if an impeller breaks, vibration increases. Although this change would not be noticeable to the human eye or ear, it is easily detected by a vibration sensor installed on the pump. The sensor “listens” to the pump’s acoustics to detect imbalances, providing early warning of issues arising within the pump.
Vibration sensors measure the vibration velocity (severity of vibration) of a machine from 0 to 25 millimeters per second (mm/s) root mean square amplitude (rms) over the frequency range 10 to 1,000 hertz (Hz). An output of 4 milliamps (mA) will correspond to 0 mm/sec (no vibration) and an output of 20 mA corresponds to 25 mm/sec (intense vibration).
Each vibration sensor communicates its frequency readings in real time to the remote monitoring system. The system can be set to “alarm” when an out-of-limit value is detected. This allows for time to take the action required to prevent catastrophic failure, secondary damage and downtime.
Many remote monitoring systems function as data loggers because they record and store all sensor data, which personnel can access and view at any time. When vibration sensors are integrated, they capture vibration readings at set time intervals, which can be viewed in real time and analyzed for trends that indicate a failure is imminent.
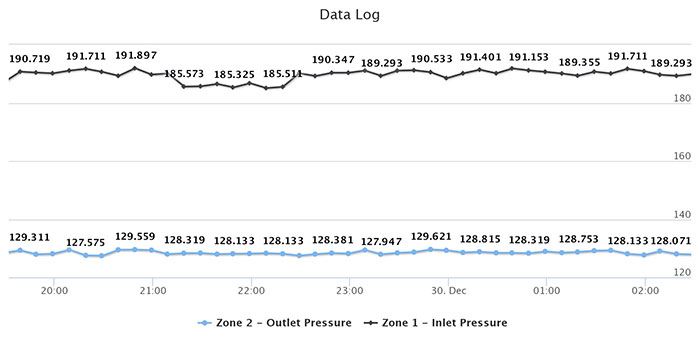
2. Monitor Pressure
If a pump is running, it has pressure. Monitoring this pressure is a key way to understand the characteristics of the pump and increase its life cycle. The more flow, the less pressure on the discharge, whereas low flow will show a higher pressure on the discharge. Pressure sensors help identify key problems that can prevent the pump from running within its BEP.
Ideally, a pump should not operate at flows ±10 percent of its BEP.
When a pump is not running at BEP, motor temperature rises, and bearings, seals and impellers have more stress, reducing service life. This can lead to premature failure of the pumping system. It is also useful to have a pressure sensor on the suction side: the difference in pressure is proportional to the total head. It is ideal to have pressure sensors on both sides of the pump.
Pressure sensors also monitor pump discharge, so they can alert if a pump shuts down for a long period of time or pressure drops from lack of suction. Pressure alarms allow users to take action to prevent the pumps from running dry if suction is lost for any reason.
If the pumps are water-cooled by an externally fed supply line, pressure sensors can monitor these lines for adequate pressure. Water-cooled pumps will go into a thermal overload if the temperature reaches unsafe levels, causing permanent damage to the motor, shaft and impeller. Cost-efficient sensors can prevent expensive repairs and unexpected downtime at the station.
Remote monitoring devices can interface with pressure sensors. For example, 4 to 20 mA inputs work with an array of sensors and provide real-time data acquisition, so well pressure data can be logged and accessible via the web interface at any time. This allows end users to easily run reports and analyze accurate data.
In wastewater applications, submersible pumps are typically placed at the bottom of lift station storage tanks to pump suspended solids, sewage and refuse. Pressure sensors can identify blockages and flooding so that operators can turn on additional pumps during flooding, equalize wear on pumps and turn pumps off when tanks are low.
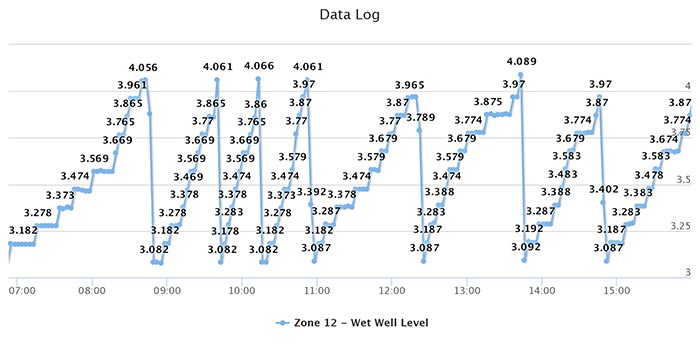
3. Monitor Current Amperage & Voltage
Remote monitoring systems can easily monitor for power failures, which stop pumps and other equipment from running altogether. But you can go a step further by continually monitoring the pump’s motor current and using the results to determine if there is a looming problem. A pump running at overcurrent for a long time, even by small amounts of 5 to 10 percent of their rating, will ultimately overheat, damaging internals and causing premature failure. Bad or failing bearings, clogged lines or material jammed within the pump can also cause an overcurrent problem.
Reduced flow caused by a blockage can also cause an undercurrent situation. In an overvoltage situation, current can increase and cause motor temperatures to run higher when the load decreases, causing a surge in voltage to the pump’s motor. Similarly, if the voltage sags under heavier loads, the motor can suffer from a low-voltage state, which will increase the motor’s current.
In any pump installation, the amount of current (amperage) the motor draws correlates directly to the size of the load. Adding a current transformer (CT) on the pump’s incoming power will monitor the pump’s current draw. A severe increase or decrease as described above indicates a pump problem that requires immediate attention. In pump installations, problems like suction loss and jams can cause serious damage to the motor or pump long before the thermal overloads trip.
These problems can be detected within milliseconds of the occurrence by monitoring the drive motor current with a current transformer.
Wastewater treatment plants also use current transformers to monitor motor conditions at remote lift stations. Operators analyze current data from each motor to predict potential failures. Current monitoring can extend the life of any pump system.
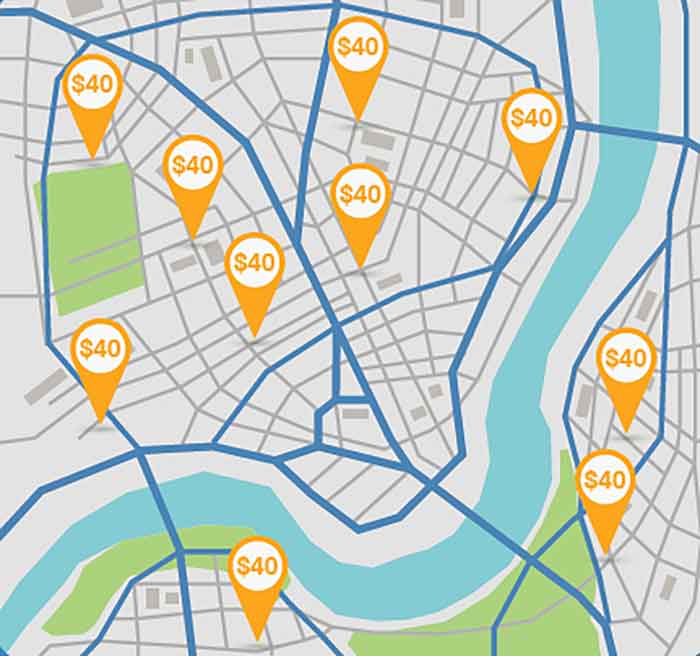
4. Pulse Counts, Run Times & Alarms
Monitoring systems should be equipped with data acquisitioning functionality to automatically provide operating statistics and historical information on the pumps that indicate how well the station is performing. Personnel can collect and record precise data, including flow rates, run times and all the operational principles involved in pump monitoring. This data is available via a web interface and can display in real time as the pump operates.
Flow meters with multipliers can be configured to determine how much flow a station is outputting. These values can be recorded and archived, so operators can create monthly and yearly reports. Important run times to include for data measurements include total hours a pump has worked, how much accumulated time the station has operated per day, and work cycles on pumps. So, when an inspector requires data, run time reports can be easily produced and exported.
Other reports like alarm logs can be crucial tools to determine how much time the site was offline and when it came back online. Depending on the length of the downtime, penalties and fines occur most often when authorities determine that you didn’t take fast corrective action to get the site back online.
5. Switch to Cellular Service
Cellular-based remote monitoring systems can have a higher initial cost, but that cost is easily recovered with lower monthly rates. Cellular service costs far less than dialers using copper phone lines. For each remote site added, the recurring monthly cost on the landline can be cut in half.
In addition, cellular systems are supervised. These systems will generate an offline alarm if the device unexpectedly stops communicating, which can be caused by a weather-related event, power surge, mass outage or human error. With unsupervised landline-based systems, users can call in to verify the lines are operational. But a line can go down at any time after that check, rendering the pump station’s alarm monitoring system useless.
Look for cellular systems that are cloud-based because they provide the greatest flexibility, redundant servers, real-time monitoring and data acquisition.
Cloud-based cellular systems give a full view of all the sites from a user-friendly dashboard, as well as free phone apps to monitor on the go.
Final Thoughts
It is vital to keep pumping systems and stations running as efficiently as possible. A remote monitoring system with integrated sensors can provide all the protection needed to avoid high-level events and also enable users to conduct predictive care and maintenance.
When production depends on early fault detection, sensor selection becomes critical. Sensors help monitor vibration, pressure, current, pulse counts and run time. The right system provides a clear picture of energy use, equipment life cycle and pump performance. It also uncovers fault trends to predict and diagnose pump failure, breakdowns and performance loss.