Chemical, petrochemical and refining applications such as pipeline transfer services, waxy oil charge, polyethylene terephthalic acid (PTA) reactor feed or water injection require American Petroleum Institute (API)-compliant pumps that can deliver typical flow rates of 300 to 1,500 gallons per minute (gpm) (68 cubic meters per hour [m3/h] to 340 m3/h) and heads up to 15,000 feet (4,572 meters). The pumps commonly used for these applications include API multistage, integrally geared pumps and BB3- or BB5-style pumps. They achieve higher pressures by connecting multiple liquid chambers in a series, sometimes at higher speeds. Increased final discharge pressure is accomplished through increased rotational speed, impeller trim size, number of stages (impellers) and diffusion pressure recovery. The plants using these pumps run operations around the clock, so unplanned downtime should be avoided at all costs, as the value of a lost day of production vastly exceeds the cost of the pump. How do plants ensure pumps are optimized to run at peak efficiency, in a manner that extends the mean time between maintenance and reduces maintenance costs?
Proper Selection & Design
It starts with proper selection and process design. Two stage pumps that use the addition of a speed increasing gearbox can replace up to 12 stages, which offers a significant reduction in material costs. It minimizes the complexity of setting clearances and takes up about 25 percent as much space in the plant. Sizing the pump properly at the outset is critical. This is accomplished by advanced analytics and computer-tailored hydraulics, which place the best efficiency point (BEP) at or slightly below the rated point, resulting in optimum efficiency and reduced end-of-curve horsepower (hp).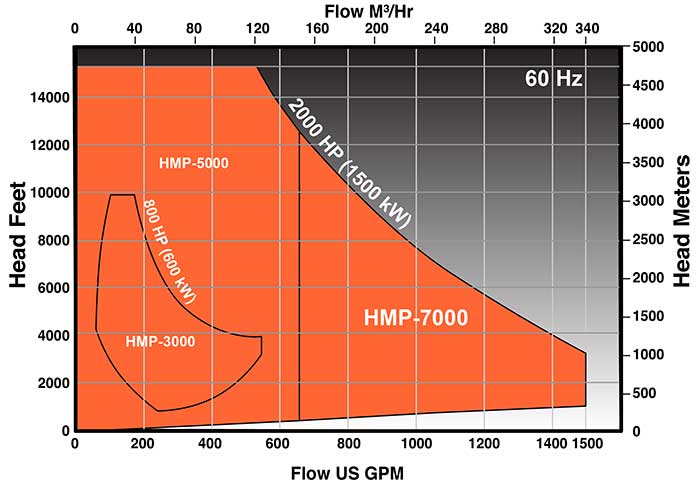
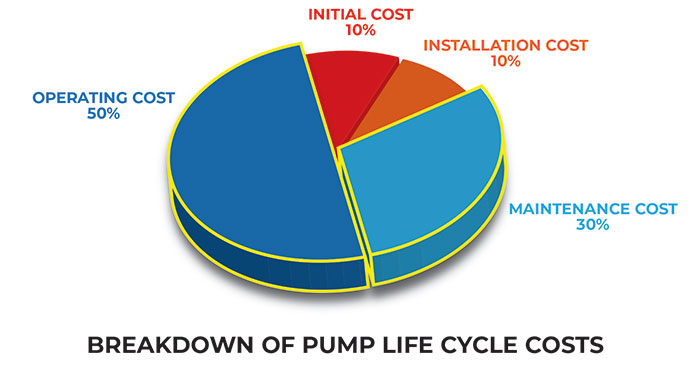
7 Upgrades on Multistage Integrally Geared Pumps
- Process seals—Many new materials have been developed that improve seal performance and life.
- Process seal rotating face—Today’s “soft-mount” design creates a more stable sealing surface. Removing old hard-mount hardware allows the rotating face to better handle fluctuations in temperature and pressure while improving the running flatness of sealing surfaces.
- Seal housing—Modifications are needed to accommodate the newer and more reliable rotating face, and also to improve fluid flow through the seal housing and remove high-point vapor pockets, which improves seal life.
- Gearbox seal—Today’s latest gearbox seal designs offer better sealing capabilities and reduce leakage of gearbox oil, reducing process fluid entry into the gearbox.
- Shaft sleeves—These are machined to extremely tight tolerances. They maintain proper parallelism and flatness for optimal seal life and low vibration. This type of upgrade specifically complements the new seals and rotating faces.
- Inboard bearings (motor side) and outboard bearings (pump side)—The latest generation of inboard bearings offers better rotor stability over a wider operating range and improves bearing stability, while enhanced outboard deflection pad bearings improve rotor stability, damping and reduced vibration and enable improved seal longevity.
- Instrumentation—Updated instrumentation for monitoring vibration and temperature accommodates the new bearing designs.
Upgrades Offer Better ROI
Upgrading these key elements reduces MTBR and provides operational flexibility while leveraging improvements in materials and design technology. Upgrading these elements can double the service life of the bearings and seals at a fraction of the cost of replacing the entire pump. In most cases, this eliminates the need to make any changes to piping and foundations. Because of the modular design, upgrades to key components can refresh an aging pump in a manner that delivers longer service life. Upgrading eliminates the cost of installing a new pump, which in refineries or fertilizer plants involves a customized process defined by nonstandard piping, different foundations, space limitations and steel structures. A re-rate of the pump with an upgrade to the key components can be easily accomplished in a matter of days, during a standard turnaround, at a fraction of the cost.Benefits of an Upgrade
Operating costs—These costs can be minimized by reducing energy costs, vibration, eliminating leakage and ensuring that pumps are operating at their BEP.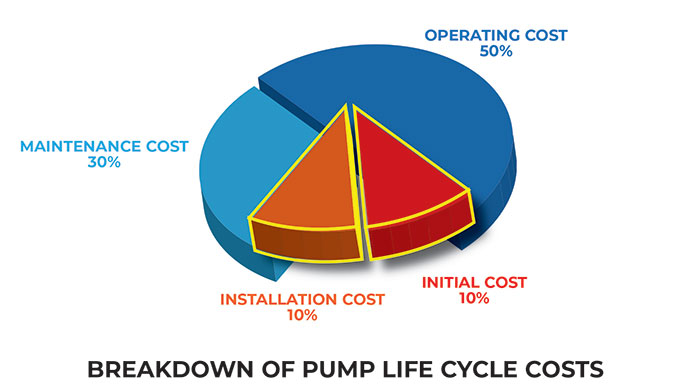