Amechanical seal has failed, and the pump must be taken offline. The consequences could range from a minor inconvenience to a complete unit shutdown. The reliability of that pump and possibly the entire system has decreased. So, what happened? Some clues may be gained by examining the seal components, but finding a true root cause is unlikely without knowing the conditions surrounding the seal leading up to the failure. Consider for a moment that passenger aircraft, trains, merchant ships and (eventually) cars are required by law to have onboard data recorders (ODRs) that produce alarms, perform system checks and provide evidence for incident investigations. Aircraft ODRs must record 91 types of data, trains 25, merchant ships 25 and cars 15 (for vehicles that have ODRs). Of course, comparing a single mechanical seal in a small water pump to an Airbus A321 traveling at 500 mph or a 10,000 ton freight train rolling through Chicago might be a stretch. But certainly the user can think of several pumping applications where a seal failure could threaten the safety of plant personnel, cause significant damage to the pump and other equipment, or result in significant economic costs. If we place all of these concerns under the heading of reliability, then the transportation industry says that knowledge is a major component of reliability: real-time, all-the-time, automatically recorded knowledge. An investment in piping plan instrumentation can increase real-time knowledge and plant dependability. The more the piping plan instrumentation acts like an ODR, the more reliable the system will be.
Consider the following examples:
1. Many large process plants and pipeline networks record data from electronic transmitters that detect mechanical seal piping plan parameters such as pressure, temperature, flow and level. This data is routed to the supervisory control and data acquisition system (SCADA) where operations, maintenance and reliability teams can respond to alarms and plan future maintenance before an expensive seal failure happens. Alarm levels can be changed remotely, whereas analog switches must be changed manually inside the switch housing.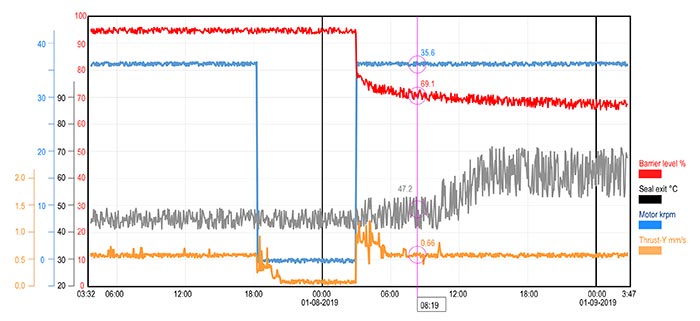
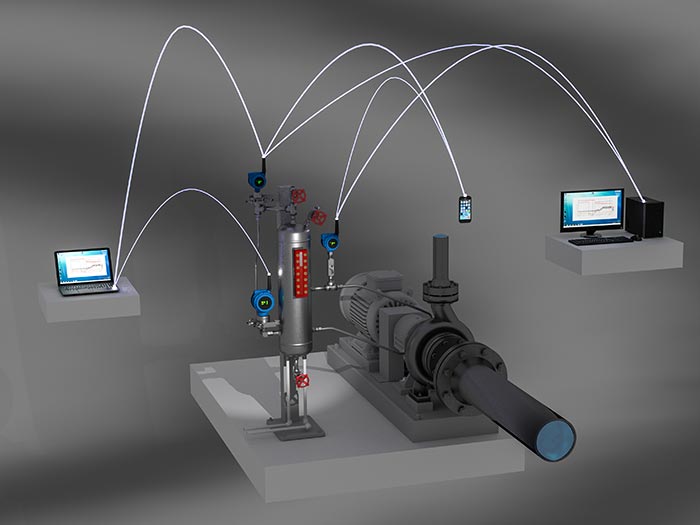
- 14 CFR 121.344 91 types of data for passenger aircraft.
- 49 CFR 229.135 25 types of data for freight trains.
- 49 CFR 563 15 types of data for cars.
- International Maritime Association, Resolution MSC.333(90) Adoption Of Revised Performance Standards for Shipborne Voyage Data Recorders (VDR). 20 parameters.
- “Beyond Switches for Pump Monitoring: What Changed with API Standard 682,” white paper, Emerson Process Management, Copyright Rosemount Inc., July 2015.