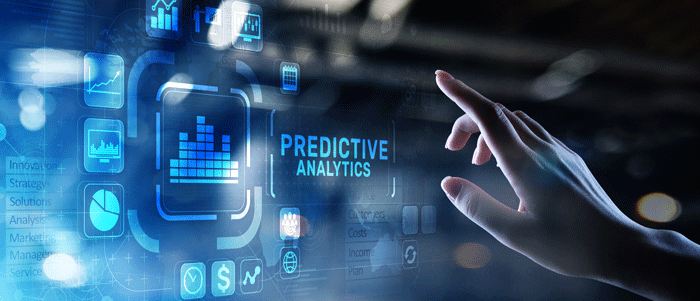
Unplanned downtime is one of the largest pain points for industrial manufacturers today, costing them an estimated $50 billion each year, per DeLoitte. The risk is even greater for process manufacturing, where a critical equipment failure could result in the loss of an entire batch, environmental hazards or safety risks. The adoption of digital technologies, such as the industrial internet of things (IIoT), promises to mitigate these threats by forecasting equipment failures in advance and catching faults before they lead to unscheduled shutdowns. However, in practice, several challenges arise when maintenance personnel and operations leaders work to implement an IIoT solution aimed at eliminating unplanned downtime.
As the various technical fields that support predictive maintenance (PdM) solutions have matured, the offerings and approaches available on the market have grown in scope and variety. Effectively sorting through these different solutions can become an effort in its own right, even before any implementation work has begun. Even for those early adopters who have been working on implementing IIoT solutions for years, there is often a disconnect between the expectation of what a solution will offer and the actual output of the product.
The narrative surrounding data analytics technologies, such as machine learning and artificial intelligence (ML/AI, here used interchangeably), is often the promise of a platform with predictive analytics that are able to predict when and how a piece of equipment is going to fail. In reality, the term “predictive” is misused for technologies that are inherently nonpredictive. Although nonpredictive technologies provide some value on their own, it should be clear as to what is truly predictive and what is not.
Diagnostic Vs. Predictive Analytics
For an algorithm or software platform to be predictive, it should provide information on an event in advance of the actual occurrence of the event. Currently, nearly all solutions advertised as predictive actually operate in a diagnostic fashion by providing explanatory insight into the current operation or condition of an asset or system. Diagnostic solutions take real-time sensor data and provide information on the current condition or performance of the monitored assets. Top-tier solutions can provide real-time notifications of small problems that are known precursors to larger problems, which provides value to the end user. However, nothing in this scenario is predictive, as no information regarding the time or severity of any future events has been provided.
A prevalent diagnostic technology that has seen recent advances and enhancements is online condition monitoring. Condition monitoring on its own only provides access to data. Online or continuous condition monitoring enhances this access by providing critical data in real time over the complete duration of the asset’s operating window. More sophisticated solutions may apply diagnostic analytics on top of condition monitoring to present the data in a form that is more easily interpreted by operators and maintenance managers.
In contrast, predictive analytics paradigms, such as prognostics and predictive maintenance, go beyond the current state of an asset or piece of equipment and provide information on the time to failure explicitly. Predictive algorithms consider the current state of the machinery or process, as well as the loads and stressors, and make a prediction about the evolution of the system. This provides additional insight into when and how the asset will fail. Similar methods can also be used to conduct “what-if” scenarios that predict the hypothetical outcomes resulting from changes in the process, asset condition or operation.
Are True Prognostics Possible?
Strictly speaking, a prognosis has three elements: time, location and severity of an event. However, this may seem difficult to accomplish in practice. Being able to predict when and how failures occur has long been thought of as a holy grail for industrial maintenance. As such, much research has been done on this subject. In recent years, this research has provided more accurate modeling, advancement of machine learning and data science and increases in computing power available to industrial operators. The application of such technologies to predicting machine failures has given rise to distinct areas of applied science, such as prognostics and health monitoring (PHM) and PdM. In fact, in the past five years or so, users have seen the commercialization of PHM and PdM research, with industrial end users beginning to realize the value of this new technology.
What makes prognosis possible is a confluence of several key technologies:
- New sensors specifically designed for use in IIoT settings that have the ability to operate in harsh or sensitive environments.
- Advances in machine learning and deep learning that make such approaches suitable for prognosis problems.
- Advances in physics of failure and simulation approaches that provide accurate predictive models of damage and failure progression.
When these technologies are combined with deep subject matter expertise, algorithms can be developed that take sensor data, track the progression of a specific asset’s condition and provide a predictive model of when and how the asset is going to fail.
Deriving Value from Predictive Solutions
With diagnostic solutions, end users benefit from greater insight into the health of their assets and can realize value when faults are identified early in their progression. Such a value proposition is often referred to as actionable insight and represents the new paradigm offered by typical implementations of IIoT, in contrast to the traditional practice of schedule-based maintenance. The success of diagnostic analytics also depends heavily on the accuracy of fault detection. With a high rate of false positives and false negatives, operators and managers have a difficult time judging which events should be acted on. Even when fault detection accuracy is high, maintenance managers cannot address many early faults immediately, and they still need to schedule service in advance. Without some sense of the time frame for a fault to progress to catastrophic failure of an asset, and without a reasonable estimate of the severity of such a failure, maintenance scheduling remains suboptimal, and unplanned downtime cannot be eliminated.
By coupling accurate fault detection with prognosis, maintenance managers determine repair and maintenance time frames based on accurate estimations of the time to failure for an asset or component. For instance, if a critical fault is detected, but failure is not expected for several months, more time can be allotted to prepare for repair and replacement activities so that disruption to production can be minimized or eliminated. Conversely, if a critical failure is predicted to occur in a matter of days, an immediate response can be prioritized with confidence.
Time horizon for prognosis is another aspect to consider. Emerging technologies are increasing the time before failure when a fault is detected by using metrics and features that are more sensitive to the mechanics of degradation and failure. With the expansion and development of physics of failure and model-based prognostics techniques, algorithms can detect the earliest signals of incipient faults, often increasing fault detection lead times from days to weeks in advance of failure.
Selecting a Predictive Analytics Platform
When selecting an IIoT solution, the first thing that plant operators and maintenance managers should do is define the expected outcomes of such an effort. If, after careful consideration, there are reasons to pursue an approach that provides failure predictions, in addition to failure detection, then the following features for a predictive analytics platform should be taken into consideration when evaluating different solutions.
The most common approach to providing failure predictions is through a remaining useful life (RUL) estimation.
Such an estimation will give an operator the amount of time before a failure is expected to occur on an asset based on the condition determined from sensor readings. Another parameter of interest is the uncertainty in the estimation, providing both a sense of estimation reliability and the time frame within which failure is expected.
To produce the most accurate RUL predictions, the prognosis algorithms should consider changes in asset operation or process conditions. This can often be achieved using model-based or physics-based approaches. The RUL will then adapt to changes in process or operating point. Furthermore, by incorporating the physical processes of degradation and specific characteristics of the equipment, the features most sensitive to faults and degradation mechanisms can be selected, and accurate predictions can be made.
Methods also exist to provide information on the location and cause of failure. These diagnostic methods include fault detection, isolation and estimation. When these elements are combined, an operator or maintenance manager is provided with far more than an indication that something is wrong with an asset. Appropriate maintenance can be planned much further in advance and operations can be optimized to completely prevent unexpected failures.
Prognosis of a Heat Exchanger
The value of prognosis can be illustrated with the gradual degradation of a heat exchanger through fouling. Fouling is the most common failure mode of virtually every kind of heat exchanger. However, in many applications, the physical processes that drive fouling are not always linear or easy to predict. For instance, some heat exchanger applications in the chemical processing industry exhibit self-cleaning behavior from time to time, and thus, the level of fouling can fluctuate repeatedly, resulting in false positives.
By including models of the evolution of the physical processes involved in fouling and the performance characteristics of the heat exchanger, changes in the operating conditions can be accounted for, and the non-linear behavior of the asset over time can be more accurately predicted. In Image 1, the end of life of a spiral heat exchanger is predicted well before substantial degradation has occurred. Examining the health history in the first figure only, a maintenance manager may conclude that cleaning the heat exchanger will not be necessary for many years. However, with the RUL prediction incorporating model-based prognostics, a more accurate estimation of the maintenance needs shows that cleaning should occur much sooner than would be considered with condition monitoring alone.
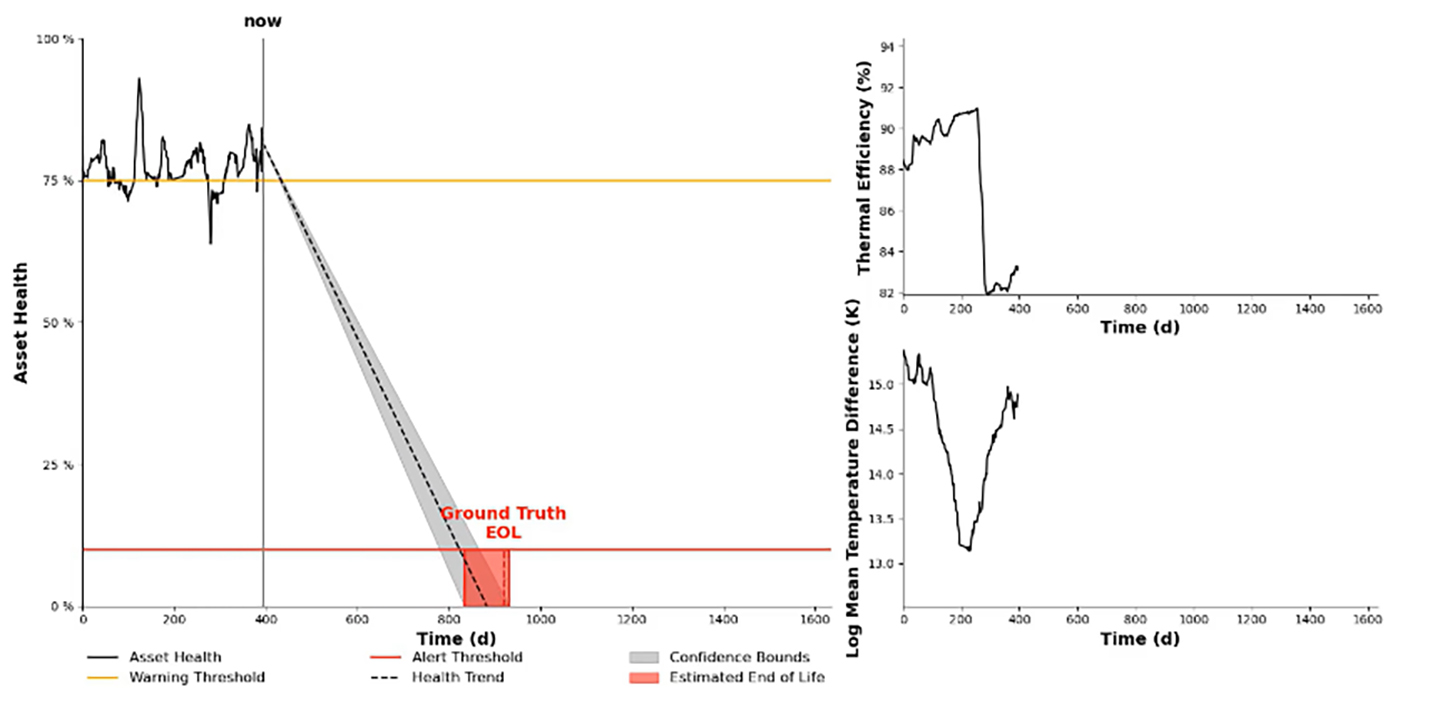
IMAGE 1: The end of life of a spiral heat exchanger is predicted well before substantial degradation has occurred (Images courtesy of Novity)
Although the prediction in the first figure has some amount of uncertainty and error associated with it, a robust prognostics algorithm decreases in both error and uncertainty over time as more history is available to the algorithm. Such a reduction in error and uncertainty can be seen in Image 2 as the health has reduced further. The signals characteristic of the failure grow as the degradation progresses and the prognosis algorithm becomes
more accurate.
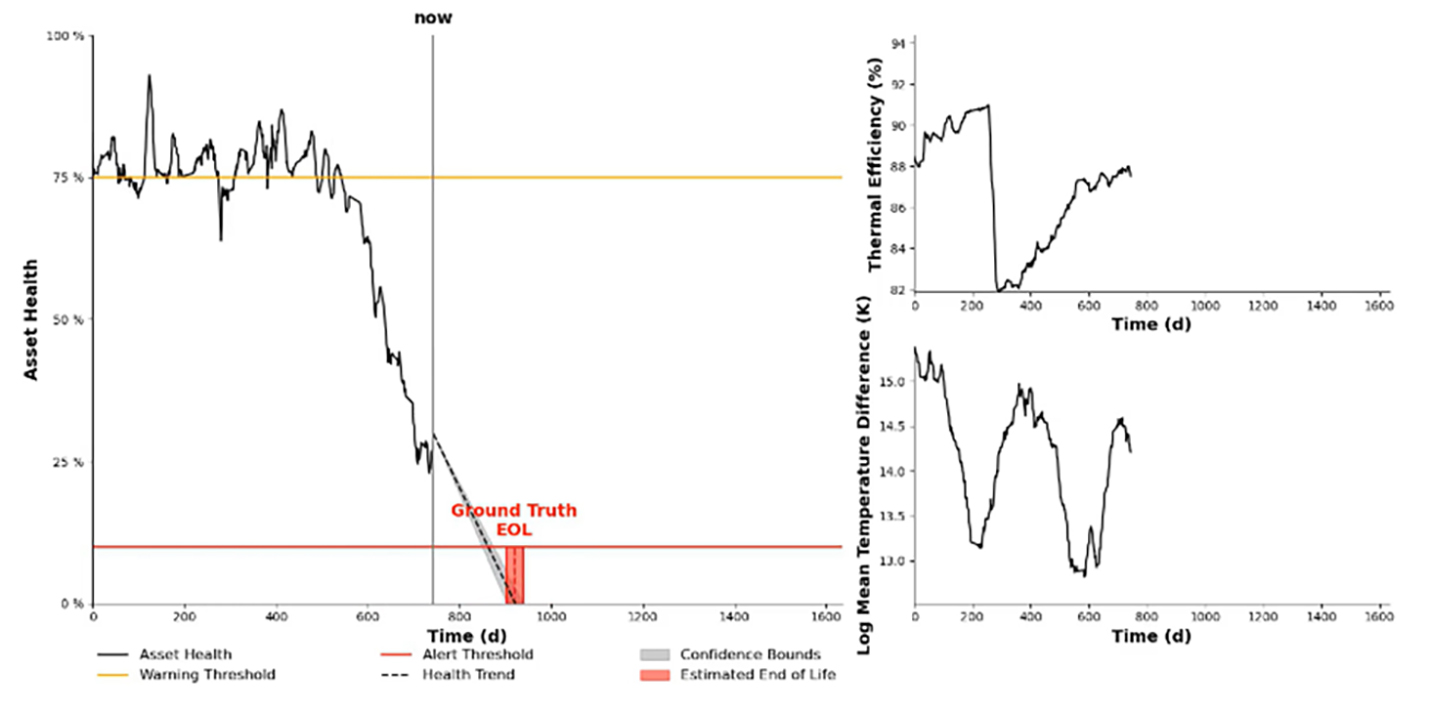
IMAGE 2: Reduction in error and uncertainty
By informed application of predictive and diagnostic technologies, process industry equipment users can drive significant improvements to their bottom line. With new sources of data coming from sensors, and effective analytical tools to process these data-streams, accurate and timely notifications of equipment problems can be provided, and appropriate action can be taken before any additional damage to mission-critical hardware occurs. Furthermore, by leveraging emerging prognostics technologies, maintenance personnel no longer have to guess when equipment is going to fail. Maintenance, repair and overhaul schedules can be optimized according to actual failure timelines, and the possibility of eliminating unplanned downtime can be realized.