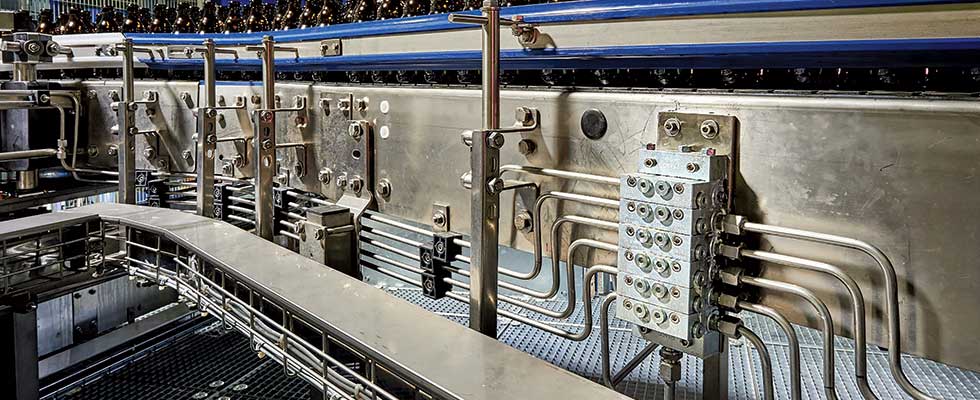
Demand is as high as ever in the food and beverage industry, and every minute matters on the production line. Any downtime affects productivity, and ultimately, profitability.
It is a problem bottling companies know well, and many are turning to automation throughout the production process to keep up capacity, especially as worker shortages plague industries. Automation keeps the line moving—usually producing higher volumes—with fewer people manning operations. It can also allow for faster onboarding of new staff in times of turnover and the ongoing transition from deeply experienced floor workers to digital natives. While the older workers knew from their long tenures what problems to look for and how to quickly solve them, the newer workers can get up-to-speed quickly with a digitized, automated application—and those automated solutions are often able to resolve any issues more seamlessly.
With bottling lines operating at high capacity, it is essential they maintain optimal lubrication to keep things up and running—which is no easy task, especially with fewer eyes on the system and increased pressure to avoid the downtime that often comes with fixing a lubrication issue.
Lubrication fails on the bottling line for many reasons, but setting up automatic lubrication with a system that meets a plant’s needs can maintain the uptime bottlers need to stay on target.
Poor Lubrication Decreases Efficacy—or Stops Production
There are challenges throughout the bottling process that can negatively impact lubrication efficacy.
Product spills can lead to equipment corrosion, reducing lubricants’ ability to keep things operating smoothly. Then, sanitary wash downs to clean equipment of contamination can lead to lubricant leakage or, even worse, remove lubricants from key bearings. Bearing failure creates downtime for repairs and replacements, which leads to lost production and increased operating costs.
Another lubrication problem occurs when lubricants go where they should not go—into the bottles and cans being filled with product. Product spoilage, even when quickly identified, can lead not only to large quantities of lost product, but also to productivity losses and costs associated with cleaning up equipment and getting it up and running again.
Worse still, if a spill is not identified before a product goes to market, a company’s image could be impaired for failing to comply with health, safety and environmental regulations.
For Automated Systems, Automatic Lubrication Is Key
To meet all these challenges, it is essential for all the equipment to have proper lubrication and management. At the same time, the bottling industry is becoming increasingly automated, adopting the use of more high-speed, high-tech machinery, all of which must be efficiently lubricated for top performance.
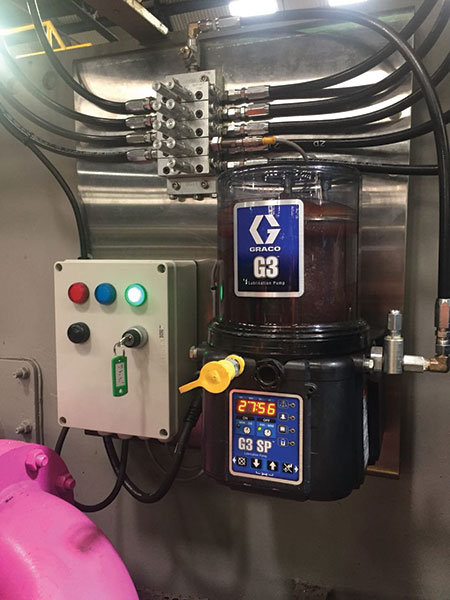
Luckily, lubrication can also be automated, allowing bottlers to properly maintain equipment while still enjoying the benefits of automating production.
Choosing the Right Divider Valves for Distributing Lubricants
In an automatic lubrication system, the divider valves ensure lubricant is dispensed accurately, ensuring optimal performance. There are several options for progressive dividers that meet the lubrication requirements of bearings and other key lubrication points, and many options come in both carbon steel and stainless steel.
It is also important to select a divider with a built-in outlet check valve to ensure accurate lubrication delivery and even consider performance indicators to enable easier and more reliable troubleshooting.
Another consideration is output volume, especially for an assembly with larger machine requirements. Selecting divider valves with larger output options is essential for heavy-duty, high-volume producers with large bearing applications.
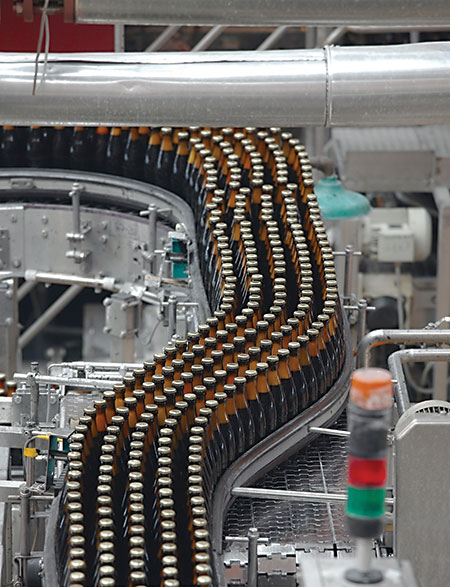
As the push toward automation and increased technology in bottling accelerates, lubrication is a vital part of the process that must keep up with other automated processes. As companies continue to look for ways to increase efficiency and lower operating costs, automatic lubrication is becoming a standard operating practice that has proven to result in a fast return on investment and long-term operating gains.
Case Study
The Duvel Moortgat Brewery in Puurs, Belgium, produces between 150,000 and 180,000 bottles of beer an hour. The brewery found it was frequently experiencing bearing failures on one of its bottling lines, which has 1,035 different grease points—even though the maintenance team was following its service schedule. The brewery decided to install an automatic lubrication system and immediately saw longer bearing life.
Following the initial install, Moortgat Brewery quickly installed automatic lubrication systems across the entire bottling plant, resulting in increased uptime on the production line and significant savings—not only financially, but also in efficiency, productivity and labor. The maintenance staff no longer had to lubricate each lube point manually—a time-consuming process.
The benefits of automatic lubrication extend beyond longer product runtimes. Automatic lubrication systems also help protect against moisture, sugars and wash-down chemicals that can chew up and damage bearings—preventing fluids from penetrating the bearing housing by creating a fully sealed lubrication system. With bearings failing less frequently, maintenance departments can be more efficient, and producers can potentially save thousands of dollars in spare bearing inventory.