It is becoming increasingly necessary to implement the same proactive approach to maintaining motors that is used to maintain the mechanical equipment that those motors drive. Taking a proactive (or precision) approach to maintaining plant assets can reduce maintenance by 50 percent over other maintenance philosophies. It is common practice for motor reliability to build an inventory of spare motors and place them in storage for use at a later date. These “new” motors will remain on the shelf until needed, sometimes several years from the original purchase dates. When these motors are installed, they are given the run test. If they run they are considered good to go, and any issues in the motors are lived with, undetected or ignored. This is usually because the cost of removing and replacing these suspect motors can be high. Replacement may also require a plant shutdown; in these cases, plant operation dictates the action. Considering the importance of these machines in the successful operation of these various plants, it’s surprising how little effort is spent verifying the condition of new and rebuilt motors. Many users assume that since a motor is new, it’s perfectly suited for service, but that is not always the case. Plants that routinely perform new motor acceptance testing report between 25 to 30 percent of new or rebuilt motors have issues. These issues may not prevent the motors from operating, but they often result in shortened lifespan, inefficient or less than optimal operation, frequent or repetitive failures, or increased operating or maintenance costs.
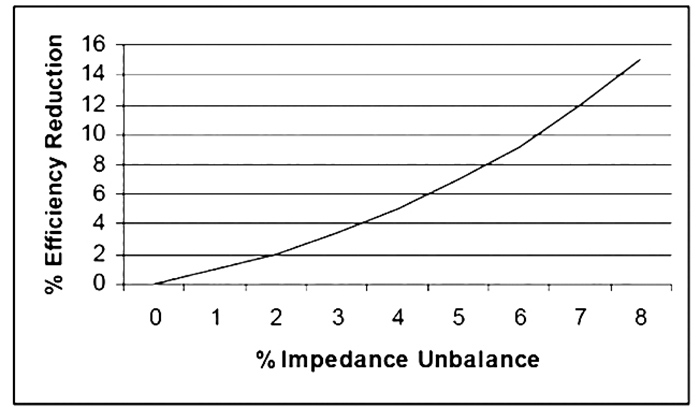
Increased Energy Costs
A motor with an impedance unbalance may operate successfully for many years. However, an impedance unbalance creates excess heating, which reduces the life of the insulation and ultimately shortens the life of the motor, and will also reduce the efficiency of the motor, which will increase operating costs. For example, Figure 1 shows that a 3.5 percent impedance unbalance on a 75-horsepower (hp) motor reduces the motor’s efficiency by 4 percent. If this motor operates at 80 percent load for 7,500 hours per year with a demand cost of $11/kilowatt and an energy cost of $0.07/kilowatt-hour, the excess cost of energy is approximately $1,200 per year.Reduced Life
An impedance unbalance will create a current unbalance and increased currents in one or more phases. This increased current causes increased I2R or heat losses. The same 3.5 percent impedance unbalance that increases the energy costs also causes an increase in operating temperature of approximately 30 percent. Every 10 C temperature increase reduces the life of the insulation by 50 percent. If the motor is operating at 60 C, a 30 percent increase in temperature equates to approximately 200 C increase in temperature. This will result a 75 percent reduction in the life of the insulation.Additional Financial Considerations
Most plants operate with minimal maintenance departments, and skilled labor is at a premium. Once a motor is installed and operating, plants are satisfied to let it run unless it completely fails. Additional testing or replacing a motor before failure, are not usually considered. Remember, it takes the same amount of time to install a suspect motor as a good motor. So installing a motor without careful consideration when we know 25 to 30 percent of new motors have issues is not an efficient use of time.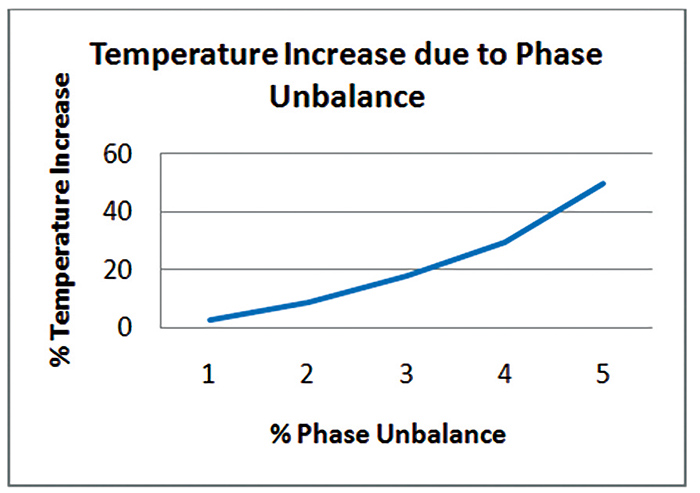