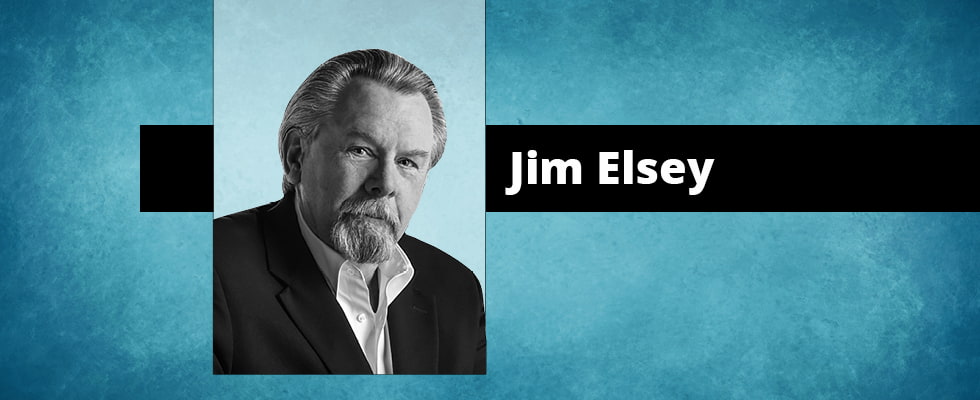
I am frequently asked for pump startup commissioning advice and procedures—and from experience I begrudgingly predict that what most folks are actually looking for is the abridged CliffsNotes version. I typically start asking specific questions about the pump and the application, but the conversation quickly falters and fades to sports or a binge-worthy series on Netflix.
The Basics
I have personally commissioned hundreds of pumps over my career, from small to really big and with drivers of all types ranging from steam turbines to engines and motors. Not all of these startup events went well, but from the failures came experience and from those experiences came wisdom.
There are a few basic steps no matter the pump type or application that I will cover, and then I will also address the often overlooked details (common mistakes) that can deliver both people and equipment into pump purgatory. For the purposes of this column, I am speaking only for centrifugal pumps and, unless otherwise noted, the pumps are not self-priming. Many of these tips and comments are for initial startups (commissioning evolutions), but will also deftly apply to the pump you start up every Monday morning.
When I am scheduled to supervise a pump startup, I immediately remind myself of one of my old and trusty mnemonic devices. This one is borrowed from the medical profession and in Latin is “primum non nocere” or in English, “first, do no harm.”
Over my career, I have often been summoned to the crime scene as the post-disaster forensic pump pathologist. I have witnessed some expensive startup mistakes that could have easily been avoided if only the operator had simply read and observed a few key points in the instruction book.
Let’s start with a few basic steps that are true regardless of the pump type, model and application.
- You have read and understand the instruction manual and the local facility operating procedure manual.
- Every centrifugal pump must be primed, vented and full of liquid before it is started. The pump you are about to start must be properly vented and primed.
- The suction valve must be fully open.
- The discharge valve may be closed, partially open or fully open; it depends on several factors that are covered later in part two.
- The bearings for both the pump and driver must have proper lubrication—oil at the proper level and/or validation check for the presence of grease. For oil mist applications, you must verify that the generator is in operation.
- Pump packing and/or mechanical seal must be adjusted and/or set properly.
- The driver must be accurately aligned to the pump.
- A full system lineup procedure (valve positions) shall be completed.
- Do you have permission to start the pump (lock out/tag out procedures addressed)?
- Start the pump and subsequently fully open the discharge valve.
- Observe the discharge pressure gauge rise to the proper pressure and the flow meter display the correct flow rate.
- Pat yourself on the back.
Sounds pretty simple so far, but please let me offer some advice. In the words of author Stephen Covey (“Seven Habits of Highly Effective People”), you must “start with the end in mind.” Before starting the pump, did you first envision a smooth operating pump that was producing the proper flow and head while operating at the best efficiency point (BEP) with no problems? If you did, then you missed a few steps in the previous startup procedure.
All too often we will find ourselves at the pump, not properly prepared for the initial startup and accompanied by an impatient operations supervisor pushing to “just start it up.” The issue here is that in reality there is a long list of items that should have been accomplished and/or checked before this high drama startup moment arrives. Pumps are expensive, and you can easily waste all of the cost and more in the one second it takes to push the start button.
Another troublesome issue I frequently observe is that the person with the least amount of operating experience is selected as the supervisor for the startup. The person is selected for several reasons, which are unofficial but nevertheless realistic, including: the startup is on third shift or a weekend or a holiday; the building is not heated; the building is not cooled; there is no building and the weather is miserable; the site is remote; and finally, the fatal assumption that a formal education means you surely had a class on pump startup somewhere in the past.
I will limit the discussion to “things” that are required and or recommended prior to startup. The more complicated the pump and the system, the more steps and checks required. I will not cover more sophisticated installations and procedures, because these operators typically have extensive training and experience.
Regarding proper pump selection, there are also countless numbers of decisions and action steps that should have taken place long before this critical moment we call startup (alternate title: “Things You Should Have Done Prior to or During Installation”).
Examples of these basics that should have been done earlier are foundation design, grouting, elimination of pipe strain, ensuring sufficient net positive suction head (NPSH) margin, pipe size and system geometry, materials choices, system hydro test, system instrumentation, submergence calculations and auxiliary systems.
ANSI Pumps
American National Standards Institute (ANSI) pumps are some of the most ubiquitous pump types in the world. Consequently, I will address a few things that are important for this group.
ANSI pumps include adjustable impeller clearance settings. There are basically two styles that are the opposite of each other, but regardless of the style they must be adjusted to the proper clearance prior to startup. The mechanical seal will also need to be adjusted and set. Note: It is imperative to set the seal after the impeller clearance is set or the setting/adjustment will change.
The direction of rotation on ANSI pumps is extremely important because if the pump is rotated in the wrong direction, the impeller will immediately “expand” (unscrews from the shaft) into the casing and cause expensive damage to the casing, impeller, shaft, bearings and mechanical seal. For this reason, these pumps are typically shipped without the coupling installed. It is essential to perform the driver rotation check prior to the coupling installation. Skipping this step is unfortunately a common problem.
Priming the Pump
Often misunderstood, or simply overlooked, the pump must be primed prior to startup. Even a self-priming pump must be primed the first time. The brief definition of primed means that all the air and noncondensable gases are removed from the pump and suction line and that only liquid is present in the system. If the pump is in a flooded system, the process of priming is easy. A flooded system simply means that the source of liquid is at an elevation above the pump impeller centerline—gravity is your friend in the priming process. To remove the air and noncondensable gases, you still must vent them outside of the system. Most systems will include a vent line with a valve or a removable plug to facilitate this. If there is no means of venting, you will need to be creative, and those methods are perhaps the subject of a future column.
Venting Tips
You cannot properly vent a running pump. The heavier liquid will be expelled while the lighter air/gas and will stay in the middle of the pump, often trapped in the eye of the impeller and/or the stuffing box/seal chamber. Think centrifuge principles of operation and realize water is almost 800 times heavier than air. Improper venting explains that squealing noise you will hear on startup that goes away after a minute and immediately before the mechanical seal starts to leak because it ran dry. Most seal chambers/stuffing boxes should be separately vented prior to startup. Pumps with throat bushings (restrictive) bushings in the stuffing box will present specific challenges to vent. Some designs, specific seal flush systems and some accessories will allow this evolution to occur automatically. Don’t assume your system has the special design.
Vertical pumps present their own special requirements for venting. Because the stuffing box is at the high point, you need to take extra precautions in these cases.
A pump that has a centerline discharge nozzle will typically lend itself to automatic venting, but not necessarily the stuffing box or seal chamber. Pumps that are horizontal split case or have a tangential discharge will require that the casing be vented by some other means. No matter the pump type, the air still needs somewhere to go, so be sure it has a place to go. Magic is not an acceptable response.
Pump Is Not Flooded
When the liquid source is below the centerline of the impeller (lift situation) you will need to vent and prime the pump in some other manner. The three main methods are:
- The use of a foot valve (type of check valve) at the suction end of the pipe. You can fill the suction line with liquid and the foot valve will hold it in the line until the pump is started.
- The use of an external means of drawing a vacuum on the suction line. This can be accomplished with a vacuum pump and ejector or an auxiliary pump—typically a positive displacement pump.
- The use of a priming tank or chamber.
Additional Tips
Foot valves are notorious for failing or jamming at the worst time in either the full-open or full-closed position. You may not realize that it is not working when it fails in a partial position.
Any air in the suction line still needs somewhere to go (otherwise it is trapped), and the pump will not be able to compress it. You will require some type of vent line or automatic air relief valve. If there is a downstream check valve, the pump will not be able to create sufficient pressure to lift and open the check valve.
Self-priming pumps or pumps that are primed from another source will need to have lubrication to the mechanical seal during the startup and priming process. Many self-primers handle this issue with a design that uses an oil-filled seal chamber. Of course, the pump is not necessarily shipped with oil in that chamber, and you need to add it prior to startup. Other pumps will require an external source of lubrication and or independent seal flush system.
Self-primer pumps in operating mode will not leak liquid out of the suction line or the seal chamber because those areas are typically under some vacuum, but do realize that air will leak in.
Keep a record the data: bearing temperatures, flow, pressure (head), amps, voltage, frequency, vibrations and ambient conditions.
Part 2 of this column will appear in the next issue of Pumps & Systems. Read it here.
Read more Common Pumping Mistakes articles here.