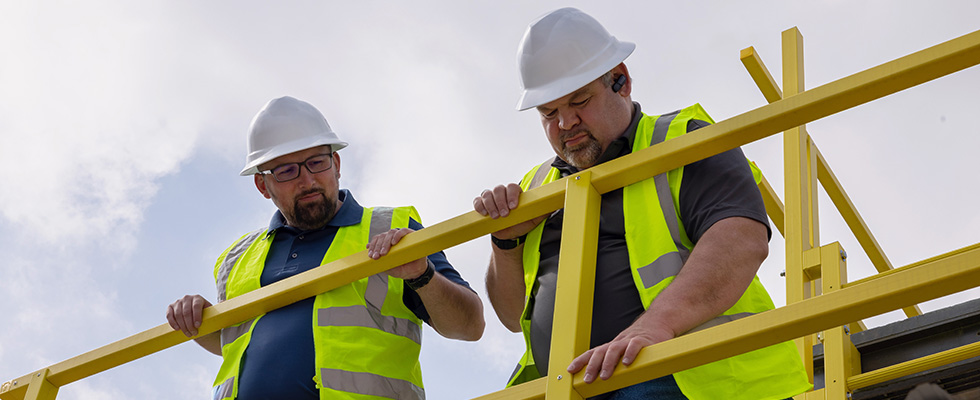
Workplace safety boils down to two specific goals: protecting people and protecting the business. The key to meeting both goals is to install industrial solutions that work and that last. Finding solutions that last is critical because a safety structure that initially meets Occupational Safety and Health Administration (OSHA) regulations could later result in heavy fines if the structural material weakens.
The Cost of OSHA Violations
Industrial facilities must comply with and be aware of OSHA standards covering a wide range of topics and circumstances. One of the standards where violations and uncertainty commonly occur is OSHA Standard 29 CFR 1910, subpart D, which covers walking and working surfaces. Contained within this section are ladders, platforms, stairways, guardrails and other fall protection systems.
In addition to putting people at risk, safety violations are costly for businesses in a couple of ways. First, noncompliance can result in significant fines. Second, businesses may be required to shut down operations until compliance is restored, causing an operational disruption leading to lost productivity and revenue.
To protect employees and visitors, and to protect businesses from operational downtime and expensive fines, users must be proactive to ensure they have a proper safety structure made with material that will last for decades.
Replace Older Safety Structures
One of the most common compliance mistakes businesses make is assuming older safety structures remain OSHA-compliant indefinitely. Previously installed safety structures—especially those made of traditional materials like steel, aluminum and wood—may degrade over time due to rust and corrosion. Even if they were once compliant, they may no longer meet updated OSHA regulations.
In addition, older structures can become costly in terms of maintenance. Replacing rotten or corroded parts, repainting scratched and flaking surfaces and repairing gouged and warped components quickly adds up. Whether they are replacing an existing safety structure or starting a new installation, users should work with a safety expert well versed in the latest safety materials designed for long-term performance with little or no maintenance costs.
Advantages of FRP Structures
One material that is both modern and proven is fiberglass-reinforced polymer (FRP). FRP offers considerable advantages:
- Corrosion resistance: A corrosive or wet environment can cause access platforms, stairs and other safety structures to age and wear prematurely. FRP safety products are resistant to corrosion from chemicals, moisture and extreme environments. This makes them ideal for industrial applications where exposure to harsh conditions is common and can damage other materials like steel or aluminum.
- Electrical safety: Controlling and reducing the risk of electrical hazards is crucial in environments with electrical equipment, especially those that also involve any form of moisture, liquids or other conductive elements. FRP is nonconductive, eliminating the risk of electrical hazards. This also means FRP structures do not require grounding, offering a safer choice for facilities with electrical risks.
- Easy installation: Avoiding downtime to address safety issues may occasionally be necessary, but FRP solutions are designed for quick, easy assembly with ordinary tools. Hiring a welder or paying for a hot permit is not necessary, as would be the case with a metal structure.
- Modular construction: No two facility designs are exactly alike, and as businesses grow and change, so do safety and access needs. FRP structural solutions are available in modular components that can be arranged to meet virtually any safety structure configuration. FRP structures can also be easily adapted and updated when workplace layouts evolve. Along with saving time, this modular construction also reduces costs because users do not have to pay for a custom design.
Lasting OSHA Compliance
Longevity is another area where FRP stands out. Because it will not warp, rot or corrode, it lasts for decades. In addition, the safety yellow coloring is integrated throughout the material, so it will not flake or scratch off. Nonskid surface grit enhances slip resistance to prevent workplace accidents, and differentiating color nosing on stair treads improves visibility to reduce trips and falls. The result is an OSHA-compliant safety solution that will protect people and protect the bottom-line year after year without maintenance and replacement costs.
Because facility layouts and needs change, it is important to partner with an FRP supplier that maintains a full stock of materials so they can be ready to ship within a few business days, helping businesses achieve OSHA compliance quickly and efficiently.
A complete FRP supplier will stock platforms, stair systems, fixed ladders, handrails guardrails and more for constructing crossovers, catwalks, stair towers, access systems and mezzanines for convenient safety configuration.
Start With a Safety Expert
To keep employees safe and avoid the high cost of OSHA violations, it is best for users to get an assessment of their safety structure needs. Users should work with a company that will take the time to send a safety expert to provide an onsite assessment of their facilities. A safety expert has a thorough knowledge of OSHA requirements and can review current structures for possible violations. In addition, a safety expert can recommend more efficient solutions, help with new configurations, offer advice on materials and more. Investing in safety today prevents costly violations tomorrow. By proactively scheduling an on-site safety assessment, issues can be solved prior to an OSHA inspection to keep business operational.