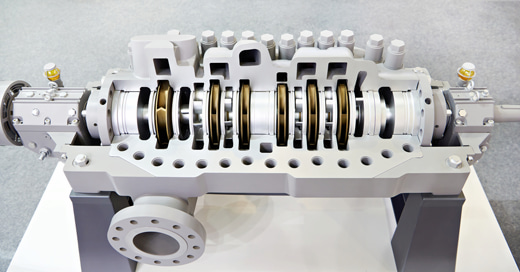
One of the biggest contributors to pump failure is issues related to rotor-bearing systems. Today, pumps are often designed to operate at increased speeds and loads to improve efficiency. These operating requirements demand that special attention be paid to rotor dynamics analysis during the design stage. This includes simulations of bearings, seals and other components of a pump.
There are numerous pump types available for industrial applications. These pumps can be classified based on design, operating principles, special features, characteristics of the working fluid, configuration (centrifugal, axial, screw, helical, positive displacement) and much more. With each type of pump, there are challenges in terms of modeling and analyzing the rotor-bearing system. On the other side of the coin, many rotor dynamics methods and principles are similar for every rotating machine.
This article will focus on two basic types of pumps: horizontal and vertical, without further specification of the design, to outline common approaches and differences with respect to rotor dynamics, bearings and seals simulations.
Vertical vs. Horizontal Pumps: Design Differences
The primary difference between vertical and horizontal pumps is the orientation and the shape of the shaft. A horizontal pump has a shaft that is placed horizontally (Top Image), between the bearings or overhung position. The shaft in the vertical pump is positioned vertically. The most common type of vertical pump is the vertical turbine pump (VTP)—Image 2. Vertical pumps (like VTPs) usually have long, spaghetti-like shafts that are connected to the motor (above or below) through the coupling and supported by a thrust bearing at the top or bottom. Another design feature of vertical pumps is the column pipe casing that influences pump dynamic characteristics. These design specifications make a difference in how to approach rotor dynamics modeling and vertical pump analysis.
What Makes Vertical Pump Rotor Dynamics Different?
Flexibility
Vertical pumps have long shafts that cause more flexibility. These flexible shafts have closely spaced modes and a dense range of frequencies. In this case, resonance vibrations with elevated amplitudes may occur, especially if the pumps operate in a wide range of rotating speeds.
The casing structure of vertical pumps (pipe) is also flexible. With that in mind, the pipe casing flexibility, as well as bowl assembly, should be considered when calculating the stiffness characteristics of intermediate radial shaft supports. Additionally, the casing structure of a vertical pump may experience high vibrations due to its flexibility, so frequencies of the pipe should also be analyzed.
Axial forces
Overhung vertical pumps supported by a thrust bearing located at the top of the machine are loaded with axial tensile force resulting from gravity loads. Conversely, if the thrust bearing is placed at the bottom of the machine, a compression force acts along the shaft. Thrust force from the impellers is an even higher contributor to the shaft tension and stiffening. All these forces change rotor bending stiffness, natural frequencies and critical speeds, so it is important to account for these factors through rotor dynamic analysis before a machine ever gets put into operation.
Bearings and seals
The bearing is one of the most critical parts of any pump. Bearings support the shaft and reduce friction on the pump’s moving parts by maintaining smooth rotation of the rotor. Bearings also bring stiffness and damping to the rotor-bearing system. Bearings that are used for pumps can be classified as radial (support the shaft in the lateral direction) and axial (suited for axial loads). The most common types of bearings that are used for pump applications are ball and roller bearings, hydrodynamic oil film (babbitt) journal bearings and pivot shoe bearings (axial thrust load support).
In the context of pumps, seals are no less important. Like bearings, pump seals are the source of stiffness, damping and additional “mass” coefficients to the rotor-bearing system, which change the entire system’s dynamics. A pump’s natural frequencies for systems with bearing and seals differ compared to systems on rigid supports.
Modeling the bearing-seal system differs in vertical pumps compared to horizontal pumps. One difference is a potentially high number of radial bearings that support long shafts in vertical pumps. In many cases, a high number of stages (for example helical/spiral stage types) in a pump increase the number of bearings and seals—the total number of bearings and seals may reach dozens. Image 4 gives an idea of how many elements will need to be modeled to obtain accurate rotor dynamic results. The combination of a long shaft, increased tolerances and misalignments with what is objectively a large number of radial bearings may result in a rapid, nonlinear change in bearing stiffness in bearings where the shaft line gets close to the bearing wall.
The second difference, and potentially even more important than the above, is that radial bearings in vertical pumps are lightly loaded (no gravity force in the radial direction), which makes the estimation of dynamic bearing coefficients more complicated. Unloaded cylindrical bearings are a cause of stability issues in vertical pumps. Thus, nonlinear analysis is essential for an accurate assessment of the rotor behavior of vertical pumps with long shafts and unloaded bearings.
Finally, in submerged pumps, which are mostly VTPs, the bearings are in a pressurized environment and lubricated by the process fluid, often with contaminations. Additionally, the working fluid mixture may change the composition, and the operating conditions of a pump (rotational speed) are often variable. Thus, these radial bearings experience accelerated wear, and the prediction of their characteristics is complicated considering the random characteristics of applied conditions. A worst-case model approach can be used to predict the dynamics and reliability to avoid critical failures.
Which Effects Should Be Considered Regardless of Pump Type?
There are areas where analysis is similar. Some other effects that are important and should be considered in rotor dynamics analysis of both vertical and horizontal pumps are:
- static and dynamic radial loads arising in the location of the impeller due to uneven clearance distribution between impeller and volute
- inertias and hydraulic imbalance forces that should be introduced at the impeller location
- effective added mass at the impellers and along the shaft
- dry, wet and process fluid conditions, as well as “as new” and “worn” clearances considered during bearing and seal analyses
- the Lomakin effect: a force created at the wear rings and throttle bushings within a centrifugal pump
- other general effects and techniques that are similar for most rotating machines and presented in American Petroleum Institute (API) 684 standards2
Though the approaches and methods for modeling and analyzing horizontal and vertical pumps are often similar, vertical pumps have their own set of features that make rotor dynamics analysis and bearing and seal simulations more complex. The major challenges found in vertical pumps relate to the construction and operating specifications including:
- long shafts
- a high number of stages
- its bearings and seals
- unloaded radial bearings
- axial forces due to gravity
Because of these design features, vertical turbine pumps are more prone to vibration problems and structural/lifetime issues. This can lead to headaches for the rotor dynamics analyst who is dealing with these kinds of pumps. Luckily, today’s engineers have access to digital tools that can be used to solve these headaches. Through advanced simulation software, dynamics standards and technical publications (for instance references 1 and 2 below), these effects can be modeled and analyzed to ensure safe and reliable operation.
References
- API, 684, 2019. API Standard Paragraphs. Rotordynamic Tutorial: Lateral Critical Speeds, Unbalance Response, Stability, Train Torsionals, and Rotor Balancing, American Petroleum Institute, Washington, DC, USA.
- API, 610, 2010. Centrifugal Pumps for Petroleum, Petrochemical and Natural Gas Industries, American Petroleum Institute, Washington, DC, USA.
- SoftInWay Rotor Dynamics and Bearings User Manual: softinway.com/software-applications/rotor-dynamics/